Grace Suizo
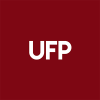
Grace Suizo
Grace Suizo has been covering the automotive fleet industry since 2007. She spent six years as an editor for five fleet publications and has written more than 100 articles geared toward both commercial and public sector fleets.
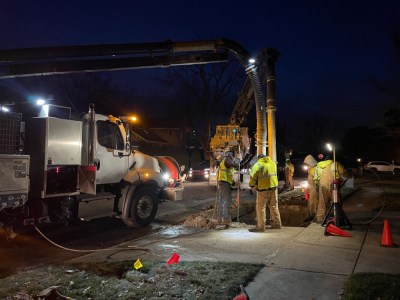
Spec’ing Truck-Mounted Compressors: Errors to Avoid
| Grace Suizo | Equipment
Two activities are critical to a fleet manager’s successful search for new truck-mounted compressors. First is gaining a full understanding of the application, vehicle constraints and long-term needs. Second is determining the correct specifications – based on the application – to ensure equipment performance, efficiency and longevity. In a recent interview with UFP, Vanair’s John […]
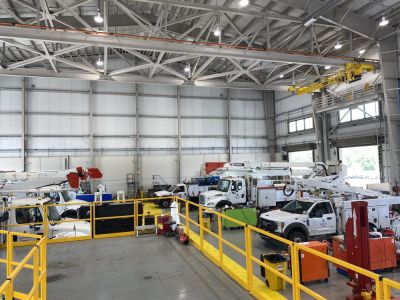
Crafting an Effective Shop Safety Policy
Creating and maintaining a comprehensive shop safety policy is essential for any utility fleet. Both James Kuha, transportation operations supervisor at Central Hudson Gas & Electric (CenHud), and Brian Johnson, fleet engineering and technical services manager at Alabama Power Co., emphasize the importance of a robust safety framework that prioritizes employee well-being and operational efficiency. […]
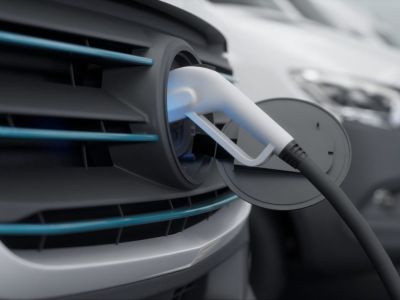
Best Practices for Developing an In-House Maintenance Policy for EVs
Although some utilities outsource electric vehicle maintenance, those fleet managers exploring the idea of handling it in-house can follow best practices and industry standards to create a comprehensive maintenance policy tailored to the unique needs of EVs. The first step in developing such a policy is to conduct a thorough assessment of the fleet’s specific […]
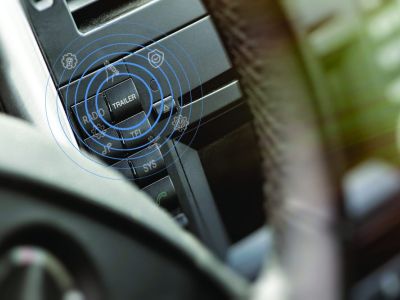
The Latest Developments in Trailer Telematics
| Grace Suizo | Equipment
The strategic implementation of telematics in utility fleet trailers is not just an upgrade – it’s a transformative step toward smarter, safer, more sustainable utility fleet operations, according to Greg Spiropulos, business development manager for Geotab (www.geotab.com) “All of the benefits extend to the bottom line,” he said. “Telematics can generate considerable cost savings by […]
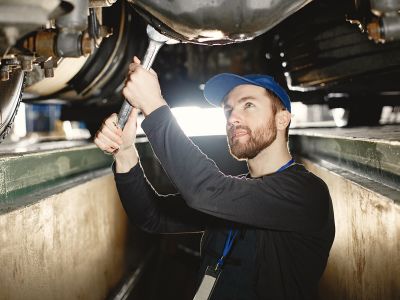
Maintaining Productivity Amid the Challenge of Extended Lead Times
Fleet managers continue to see some of the longest lead times in decades, with supply and delivery disruptions significantly hampering the industry. Across the board, every size of truck and car and every type of rolling asset has been impacted, according to Matt Gilliland, director of operations and business support for Nebraska Public Power District […]
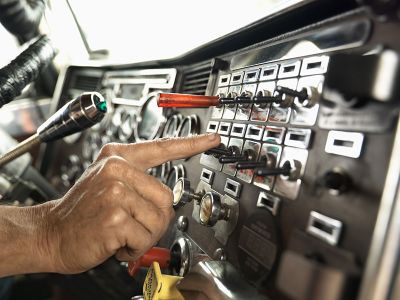
Addressing Ergonomics in Utility Fleet Vehicles
| Grace Suizo | Equipment
It’s no secret that there are myriad items a utility fleet manager must consider when spec’ing vehicles for their fleet. Among those are the vehicles’ ergonomic features, which are intended to provide greater operator comfort and efficiency. According to Pete Gnatowski, director of sales, manufacturing and distribution for global automotive services organization Holman (www.holman.com), “When […]
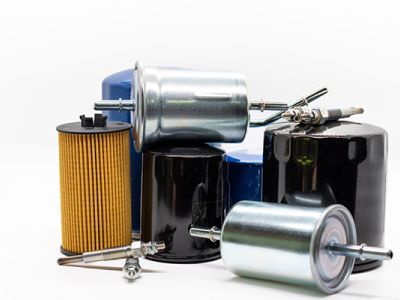
OEM vs. Aftermarket Parts: What’s Best for Your Operation?
When it comes to purchasing parts, how do fleet professionals decide whether to take the OEM route or explore aftermarket options? UFP recently spoke with Alan Cunningham, superintendent of fleet maintenance for Ameren Illinois, and James Kuha, transportation operations supervisor for Central Hudson Gas & Electric, to gain some insight on how they make these […]
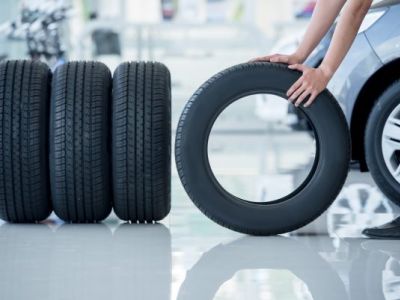
Tire Procurement Strategies for Utility Fleets
Con Edison, headquartered in New York, operates a fleet of approximately 8,100 active assets ranging from light- to heavy-duty vehicles, including digger derricks, flush trucks, bucket trucks, tankers, tow trucks, buses and trailers. The utility’s tire procurement decisions are made by an internal tire committee, whose members include engineers from the transportation department as well […]
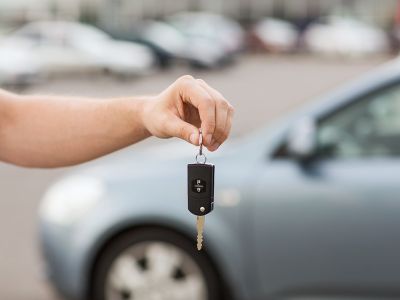
Best Practices for Managing a Shared Vehicle Pool
How many vehicles does your organization use every day? What about weekly? Monthly? According to Mike Hicks, vice president of marketing for Agile Fleet (www.agilefleet.com), these can be challenging questions for prospective clients to answer. “For many organizations, it can be difficult to track what vehicles are owned, where they are, their condition and mileage, […]
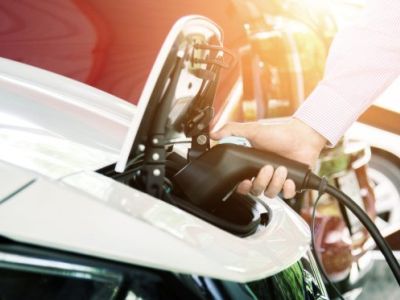
Retooling Your Shops for EVs
Electric vehicles have been rolling out in more and more utilities as fleets continuously strive to green up their operations. But making the transition from combustion to electric involves more than just getting operators on board. Among other things, it also means making sure shops and technicians are well-equipped to properly service these units. According […]