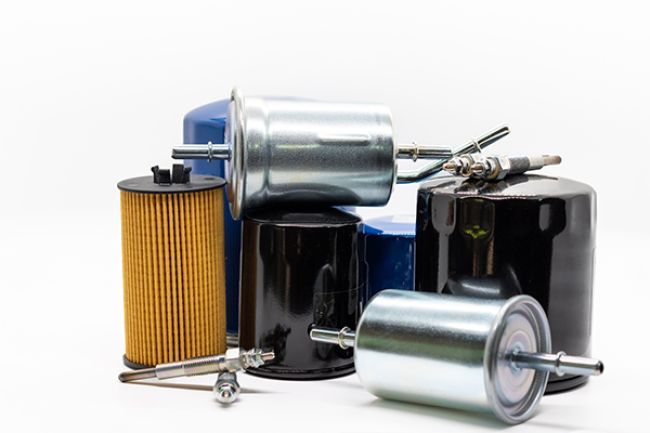
OEM vs. Aftermarket Parts: What’s Best for Your Operation?
Two utility fleet professionals share guidance on making the optimal choice.
When it comes to purchasing parts, how do fleet professionals decide whether to take the OEM route or explore aftermarket options?
UFP recently spoke with Alan Cunningham, superintendent of fleet maintenance for Ameren Illinois, and James Kuha, transportation operations supervisor for Central Hudson Gas & Electric, to gain some insight on how they make these decisions.
Involve the Experts
According to Cunningham, relying on your frontline team is critical when making parts purchasing decisions.
“Our fleet technicians and frontline supervisors are the best resources for knowing which part works best, how best to source those parts, and how to get the job done in a safe and timely manner,” he said.
The Ameren Illinois fleet consists of approximately 3,700 assets, ranging from small pickups and SUVs to large digger derricks and aerial units, trailers and off-road construction equipment, and a growing number of hybrid and fully electric vehicles.
The supervision team meets virtually every week. These meetings provide a forum for team members to bring up issues related to parts availability that may also affect their peers. Shop visits are conducted throughout the week, and the team usually meets in person every one to two months.
“We will always review the data and compare costs, but it’s equally important to create and maintain open two-way communication with our fleet technicians and supervisors,” Cunningham said.
Central Hudson shares the same perspective. The utility’s fleet consists of 1,089 assets, including tracked equipment, bucket trucks, digger derricks, dump trucks, light-duty vehicles and pickups, and a variety of off-road equipment.
“The employees performing the work should be involved in the discussions surrounding these decisions,” Kuha said. “They will be able to tell you about the quality of the materials/parts they are using, as well as offer insight into the durability of the parts over lengths of time. Additionally, first-line supervisors should be engaged in these decisions.”
He suggested reviewing analytics as well. “Having a better understanding of your fleet, how the equipment is used and the ramifications of not having that equipment available will allow fleet managers to make more informed decisions.”
It’s also helpful to have employees who are well-versed in fleet maintenance and aware of aftermarket options.
“We do have a parts person who orders parts needed for our technicians,” Kuha said. “This person is aware of the parts that should be bought as aftermarket, such as preventive maintenance items. She will look at availability when making larger decisions. Since she deals with vendors and parts daily, she is acutely aware of the offerings.”
Shop Around
Both Ameren and Central Hudson have a mix of OEM and aftermarket parts in stock.
One of the most important drivers for Ameren is getting the correct part for the job at hand. Price, availability and turnaround time are other factors taken into consideration.
“Ensuring our fleet equipment is safe and ready to use when needed are our primary goals,” Cunningham said.
Quality and availability are the most important factors for Central Hudson. In addition, the utility looks at the ease of obtaining the part and the associated costs.
According to Cunningham, the main advantage of stocking OEM parts is knowing they will work correctly as designed. However, cost and availability do come into play.
“Over the past two to three years, we’ve seen an increase in back-ordered parts, with some OEM electronic modules having lead times approaching a year or even more,” he said. “In these cases, we’ll work with our suppliers in finding alternatives and purchase aftermarket parts when those are an option. Early on we had problems sourcing some fairly common filters and tires, but for the most part, those have been resolved now.”
Central Hudson has been impacted by the focus on warranty work provided by OEMs.
“Since OEMS won’t use aftermarket parts, in most cases, this has extended the wait for some warranty repairs,” Kuha said. “For example, we have had several units waiting on rear differentials. Some wait times have exceeded several months.”
Finding Workable Solutions
Cunningham said that service after a sale plays a part in Ameren’s decision on whether to use OEM or aftermarket parts. While OEM is the preferred choice, aftermarket parts can also help fill in the gaps.
“If we run into an availability problem, we’ll first contact the supplier and request they work to find a part elsewhere in their system, although that may take somewhat longer,” he said. “In some cases, if a unit is out of service awaiting a part, our technicians will work with their supervisor to research possible alternate parts available from an online supplier.”
However, Cunningham emphasized the importance of sticking with only high-quality parts from a reputable source.
“There are many look-alikes of lower quality that equate to a shorter life span that should be avoided,” he said. “On occasion, we’ve had quality issues with some aftermarket parts that were marketed and sold as replicas of the OEM part but then failed early. When this happens, we’re often stuck with no recourse for service. Using trusted OEM suppliers that we’ve built relationships with over the years has greatly helped alleviate this challenge for us.”
For remanufactured driveline parts including engines, transmissions and third members, Ameren tries to purchase from the equipment manufacturer as much as possible.
“This helps ensure the rebuilt part contains any revised or updated components, meets the latest industry standards and generally includes a more robust warranty,” Cunningham said. “Normally, aftermarket and OEM warranty coverages will be similar, but working through some aftermarket return/credit processes can take more time and cost more than the potential savings.”
Lighting products and filters are some of the aftermarket parts that the utility sources.
Kuha said that for Central Hudson, OEM-specific parts work best for aerial devices and digger derricks since the utility has not found good aftermarket support for those products.
The utility does buy many of its preventive maintenance parts from aftermarket suppliers, including brakes, brake components, filters, oil, lighting and wipers.
“We have been doing this for many years now,” Kuha said. “These parts are cost effective and offer good quality.”
But while costs are important, Cunningham and Kuha both advised against looking only at costs when choosing a vendor.
“Avoid the temptation to go with the lowest-cost item or an unknown supplier,” Cunningham said. “Quality parts from a reputable source that provides personal service is still your best bet. It may take time to develop those supplier relationships, but the payoff is well worth it.”
Kuha agreed, noting that buying aftermarket parts doesn’t always translate to lower prices.
“Be careful of costs,” he said. “In some instances, you could be paying more for aftermarket parts than you are paying for OEM.”
Kuha noted that the utility recently discovered an aftermarket vendor was charging double for heavy-duty brake parts. “When we did a comparison to our local dealer, we found we could get these parts directly for 40% to 50% less than what our aftermarket supplier was charging.”
About the Author: Grace Suizo has been covering the automotive fleet industry since 2007. She spent six years as an editor for five fleet publications and has written more than 100 articles geared toward both commercial and public sector fleets.
- Women in Utility Fleet: Lissa Brady
- In Many Ways, Fleet Management is Sales
- Truck-Mounted vs. Towed Impact Attenuators
- Safety Signs and the Importance of Training
- OEM vs. Aftermarket Parts: What’s Best for Your Operation?
- When Will Drunk-Driving Detection Be Mandated on Light Vehicles?
- Exhibits and Education Headline the 54th Annual ATSSA Expo
- 6 Factors to Consider When Spec’ing Onboard Cameras
- The Evolving Fleet Professional for an Electrified Future
- Matted Surfaces: Safety Considerations and Controls