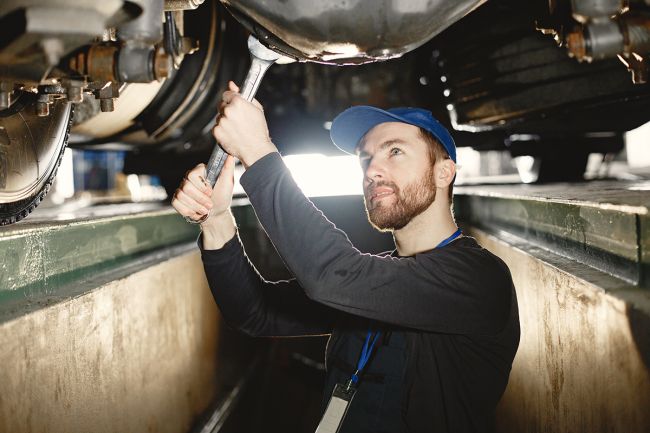
Maintaining Productivity Amid the Challenge of Extended Lead Times
With lead times forcing utilities to keep their existing vehicles longer, fleet personnel have had to adapt to ensure those assets remain reliable.
Fleet managers continue to see some of the longest lead times in decades, with supply and delivery disruptions significantly hampering the industry.
Across the board, every size of truck and car and every type of rolling asset has been impacted, according to Matt Gilliland, director of operations and business support for Nebraska Public Power District (NPPD).
“Orders have been outright canceled, delayed, or required alteration of specifications and/or the acceptance of different features,” he said.
James Kuha, transportation operations supervisor at Central Hudson Gas & Electric (CenHud), noted that new builds can now take up to two years versus just one.
“Keeping heavy-duty vehicles longer is our reality,” he said. “Bucket trucks and digger derricks have been difficult to obtain. Orders are placed two years in advance now. However, there is no guarantee that you will see the units in that time frame.”
The lack of available new units has resulted in keeping equipment longer, which has led to transmission failures, more expensive repairs and even breakdowns.
In a recent interview with UFP, Gilliland and Kuha shared how they are managing operations while dealing with these challenges.
Making the Most of Current Assets
For NPPD, the impact of extended lead times has led to a variety of mitigating steps on both the procurement/sourcing side and the maintenance side.
On the procurement side, these steps include examining specifications for what is truly needed versus what is “nice to have,” Gilliland noted. In some instances, smaller engines, fewer features and less customization are worth pursuing.
“From an operation standpoint, we have slowed our remarketing efforts to better provide overlap between assets arriving and leaving, basically creating a pool of equipment we can pull from since equipment is being kept longer and/or deliveries delayed,” Gilliland said. Additionally, the utility increased its inventory of parts by approximately 20%.
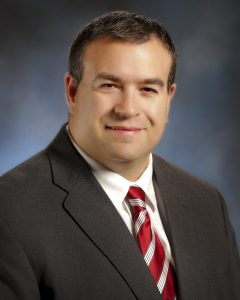
Gilliland also shared this advice: “Try to find the opportunities during all this. For example, perform a deep-dive analysis regarding inventory – is it the right stuff, do we need it and so forth. Rewrite specifications to better match what is absolutely needed and what isn’t.”
NPPD has seen significant costs and the degree of problems increase as pieces of equipment that should have already been remarketed face end-of-life issues.
“Rather than replacing consumable or wear items, we are now replacing more ‘hard parts,’ which are expensive and take time,” Gilliland said, noting that larger, more expensive items such as a cracked boom section or turret can cost more than $20,000 to replace.
The fleet has also seen stress to booms/aerials in the form of cracks in welds, broken weldments, and worn-out pivot points and bearings – issues typically not seen because units are usually replaced before they occur.
Asset care is always important, but it is especially so now. NPPD sends a newsletter to every operator, providing education about the status and causes of disruptions as well as best practices to adjust.
Gilliland advised utility fleets to adjust their preventive cadence and the preventive maintenance checklist. For example, he said items that would typically be examined yearly could be examined semiannually.
Prioritize Repairs
Looking at replacement plans and knowing the lead times are critical to the daily decisions CenHud must make concerning repairs.
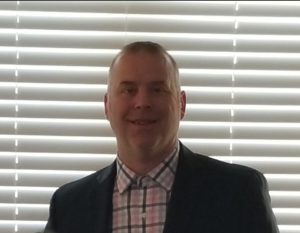
“If a unit cannot be replaced, the repair should be done properly,” Kuha said. “This may affect downtime, and that is not always received well. Additionally, this could affect expenses. However, making the proper repair will help ensure the safe operation of the equipment.”
He recommended evaluating the cost difference between outsourcing and keeping repairs in-house.
“Is it cheaper to farm out the oil change and have technicians concentrate on larger, more expensive repairs, or perhaps farm out larger repairs and keep oil changes in-house? These are the questions we must start asking ourselves,” Kuha said.
In the past, if a unit was expensive to repair, CenHud would look at replacement costs.
“With excessive lead times, we now are forced to make those repairs as needed,” Kuha said. “Unfortunately, costs have risen; however, the units must be repaired. We look at cost-saving options of repairing vehicles in-house as well as aftermarket parts when possible. We have replaced transmissions on medium-duty vehicles that we would have potentially auctioned in the past. These replacements can cost up to $6,000.”
Stay in the Know
Kuha, who was a technician for 25 years before moving into fleet management, said shifts in inventory management and parts-buying patterns can also help smooth issues.
“Watching vehicle trends and stocking the necessary parts will allow us to be more efficient with our repairs,” he explained. “Doing so can make sure we have parts on hand to complete our task. Having been a technician for many years myself, waiting for parts was always the worst part of a job.”
Gilliland noted the value of having a quality assurance process. “There are both good and bad things about the same tech seeing the same asset over and over; the same is true of not seeing the same asset over and over,” he said. “So, a combination approach makes good sense – different eyes for a new perspective, yet the same eyes so as not to lose historic trending.”
Telematics and diagnostic tools can also help monitor vehicle health to optimize maintenance planning.
“These systems offer the data needed to make informed assignment decisions. For example, it might be best to swap two assets between sites or operators given utilization rates so that overruns on age, miles and hours are kept as low as possible,” Gilliland explained.
Today’s telematics can also notify fleet managers when vehicles have active drivetrain codes, Kuha said. “If the fleet manager is aware of the code, that person can order the necessary parts to repair the unit before the vehicle arrives. Having parts on hand to repair the unit beforehand can result in faster turnaround times. Of course, this is not all cases, but we can use telematics to help make some of those decisions,” he explained.
About the Author: Grace Suizo has been covering the automotive fleet industry since 2007. She spent six years as an editor for five fleet publications and has written more than 100 articles geared toward both commercial and public sector fleets.
- Electric Utility Fleet Managers Conference Marks 71 Years
- Maintaining Productivity Amid the Challenge of Extended Lead Times
- Are Vehicle Order Lead Times Improving?
- Get Set for an Electric Chain Reaction
- Understanding Wind Speed Limitations on Utility Equipment
- When Fleet Management Becomes Change Management
- The Fleet Department’s Role in Curbing Distracted Driving Incidents
- Switching and Tagging
- 6 Takeaways from the 2024 Green Truck Summit