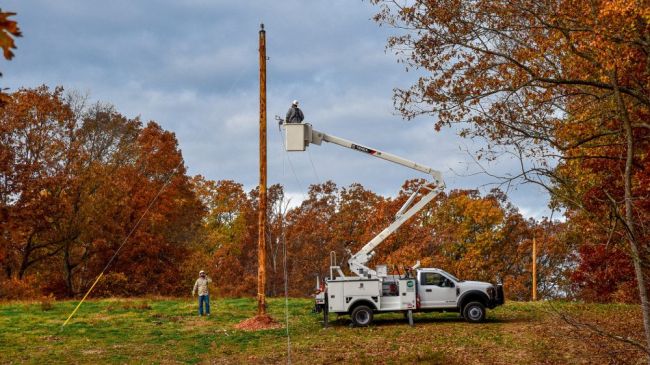
Leveraging OEM Expertise to Improve Fleet Equipment Reliability
From employee safety to equipment uptime in the field and managing costs, electric utility operations managers are entrusted with a great number of responsibilities.
Recently, when fleet personnel at Branson, Missouri-based White River Valley Electric Cooperative started noticing recurring problems in both the shop and field, John Combs knew something needed to be done. The cooperative’s chief operations officer wanted to empower his team to learn more about the equipment they operate and the best ways to minimize downtime and unplanned repairs. White River provides electrical service to more than 48,000 member meters and manages over 5,300 miles of power lines across five counties in Southwest Missouri. Combs manages the fleet, which consists of approximately 80 vehicles.
That’s when he reached out to White River’s sales account manager at Terex – the OEM of most of the fleet’s digger derricks and bucket trucks – to share some of the cooperative’s challenges.
“I continually stay in close contact with the equipment OEMs. They know their equipment inside and out and have resources that can help when it comes to properly operating and maintaining the equipment,” Combs said. “As [the sales account manager and I] spoke, it became apparent that we needed more training on certain maintenance and application practices.”
Shortly thereafter, a team from Terex traveled to Missouri, where Dale Putman, product support manager, delivered digger derrick and aerial device training to White River personnel. The training covered need-to-know information about performing proper inspections, maintaining and repairing critical components, and the importance of equipment decals and placards.
According to Combs, “Dale’s training helped shed light on why recurring issues were happening. As a result, we have changed some of our work practices and implemented tools to help our crew be as efficient, effective and safe as they possibly can.”
Improving Inspections
For the White River team, the essential nature of conducting regular equipment inspections was not a new concept – and the training Putman provided reinforced the necessity of open communication between the field and the shop.
“Dale’s training reminded us that when an inspection turns up any deficiency, our in-house mechanics must immediately be pulled in to determine next steps,” Combs explained. “We had been playing with a job-planning app and decided to fully utilize it by customizing an inspection checklist – using items from the Terex training – for our field operators to use. The app automatically sends a report to the mechanics team, our safety manager and me when operators complete the checklist.”
He also shared that app usage has “allowed for the equipment operators to be more mindful of what they are looking for as they are performing the inspections. Now that we’ve been using it for a while, the app has educated the mechanics to the point where they are proactive on regular maintenance items that don’t need to be reported.”
In his leadership role, Combs said he strives to ensure that White River employees don’t hesitate to report damage once it has been identified. “I make it clear from a management perspective that there will be no repercussions for reporting a damaged piece of equipment. We’re going to do our best to keep our crew’s equipment in the best shape possible, and it starts with [crew members] inspecting their equipment every day.”
Additional Training
The Terex training also shed light on the importance of inspecting critical components (i.e., those that support the boom, platform and load) to verify equipment’s structural integrity. Further, Putman addressed recurring issues with shop repairs, such as when retaining bolts break during tightening. “In this industry, there is a common misconception of ‘the tighter, the better,’” Combs said. “Dale helped explain why they kept breaking, and we now know to follow the defined torque value from the OEM quick reference guide.”
During the training, White River’s field crew gained greater insights into load charts and hydraulic limitations. “When you’re at a jobsite and just want to get the job done, it can be very frustrating when the lifting functions quit while you’re trying to lift a load,” Combs said. “Back in the day, this never happened on the old machines. Dale’s explanation of HOP, or hydraulic overload protection, was perfectly logical. He broke down what happens to the machine when an overload occurs, underlining the importance of the HOP system.”
Essentially, an operator who uses a winch to lift a load heavier than what’s stated on the load chart causes an overload on the lift cylinders, which in turn increases pressure in the base of the cylinders. This overload could potentially result in structural damage to the boom or loss of stability.
Conclusion
Since the Terex training, Combs said he has noticed heightened awareness and improved efficiency and communication among his team. “Dale’s willingness to break things down and educate on even the little things helped greatly. When you continue to learn the little details, it helps build logic behind the equipment applications and maintenance. Evolution versus revolution is key.”
About the Author: Tori Worley is a senior manager of customer experience for Terex Utilities (www.terex.com/utilities).
Photo courtesy of Terex
- Five Core Capacities for Sustainable Safety Excellence
- The Power of Mood in Leadership
- Public Works Professionals to Gather in Chicago for APWA’s PWX
- Spec’ing Cable Reel Trailers: 12 Common Errors to Avoid
- Selecting the Right Fuel Card Program for Your Fleet
- 5 Professional Development Resources for Utility Fleet Managers
- Leveraging OEM Expertise to Improve Fleet Equipment Reliability
- The Latest AI Advancements for Utility Fleets
- 7 Utility Construction Equipment Developments for 2025
- Is Your Fleet Prepared for the Next Economic Disruption?