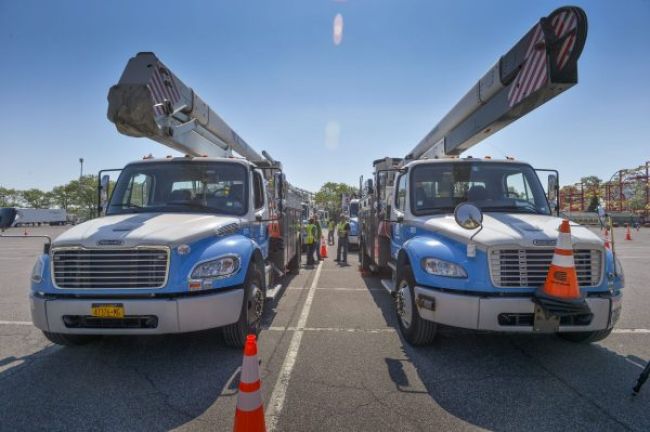
Con Edison: Fleet Safety Performance is a Collaborative Effort
A “close call” in late 2020 set things in motion to address a slip-and-fall hazard shortly after New York City’s energy provider, Con Edison, replaced 10 steel trailers with aluminum trailers.
“An employee was trying to secure a load on a very windy day. But the aluminum surface was wet and slick,” Richard Stewart, ConEd’s environmental, health and safety (EHS) manager, recalled. “When this incident was brought to our attention, we had to find a solution.”
In many types of organizations, you’ll see a lot of finger-pointing, blame-shifting and throwing people under the proverbial bus when things go wrong. But the utility industry has become known as a sector that promotes a collaborative culture, especially when solving problems that impact worker safety.
And ConEd’s experience provides a valuable behind-the-scenes view of what a collaborative culture looks like when confronting fleet safety challenges.
Why did ConEd switch from steel to aluminum trailers? What caused the increased slip-and-fall risk with the new aluminum units? How did the fleet, EHS and other departments work together to find a solution?
UFP spoke with Stewart and ConEd’s chief automotive engineer, Fortunato Gulino, to learn more about their story. Here’s an edited version of our conversation.
UFP: What factors led ConEd to change from steel to aluminum trailers?
Fortunato Gulino: At ConEd, we have four pillars to product design, whether a vehicle or trailer. The pillars represent the automotive engineering group, the garage operations maintaining the assets, the safety group and the operator. All four of us get together in a committee meeting to collaborate, whether it’s about a new product, a redesign of an existing product, or just confirming that the old product and specification are acceptable.
In this case, the steel trailers were causing problems – rotting and corrosion to the point where we had to condemn some of our trailers. So, our initial thinking as a group was that aluminum trailers would be the best solution for the corrosion issues.
But the aluminum presented a tradeoff?
Gulino: Yes. The tradeoff was the actual decking. The aluminum deck didn’t have the same anti-slip performance as the hardwood decking on the steel trailer. We learned about the issue shortly after the operators started using the new trailers.
What was the starting point for addressing the issue?
Richard Stewart: We started with administrative measures to mitigate the initial concern. Things like: “Don’t do any cargo load securement in the rain or on a windy day. And let’s move the trailer to inside the distribution bay.”
But then another safety concern arose. We transport pad-mounted transformers on our trailers. And sufficient friction – in addition to proper strapping – is critical to prevent losing loads. Naturally, the last thing you want is to lose a load, like a pad-mounted transformer, on a busy New York street.
With all the safety concerns presented, we needed to do something to improve the anti-slip performance of these new trailers.
What did you do?
Stewart: We had already been engaged with a company called Form-A-Tread (https://form-a-tread.com) on other projects to address slip-and-fall concerns at our warehouses and other facilities at ConEd.
We’ve applied their anti-slip solution to various decline and incline ramp areas throughout the company. And it has proven to be robust in preventing these types of hazards. So, we approached that company to see what solution they could create for our aluminum trailers.
What was the process for developing the requirements for the anti-slip trailer solution?
Stewart: Some of the company’s anti-slip products are rigid, and others are flexible. We needed the flexibility to compensate for the bowing of the load on the trailers. And we needed a product that could handle the robust nature of what Con Edison does to trailers. We don’t transport one universal load. We transport everything on our trailers. So, we had to ensure it could stand up to rigorous use and maintain flexibility.
[The vendor] asked for the specs, which we got from Fortunato’s automotive engineering group. They wanted to know the trailer dimensions, material, weight, load and so forth. And they did the calculations on their end to determine what it would take to properly coat our trailers with a solution that would hold up for us with the bending and flexing and the various weather changes.
Once we had a solution we thought could work, we approached Fortunato’s automotive group and asked them if we would be permitted to proceed with it. That’s the first thing we must ask: “Will you permit us to do it if we can?”
Earlier, you mentioned that the anti-slip solution is a coating on the trailer. What type of coating is it?
Stewart: It’s a two-part epoxy that’s very fast curing for the initial set, and then it requires an overnight cure – about eight hours.
Does the manufacturer install the coating, or is ConEd equipped to do it in-house?
Stewart: They did train us how to do it. However, with the high-profile nature of the project, we wanted to ensure that we got it right.
What advice do you both have for how fleet and safety can collaborate more effectively with each other and across other departments to improve overall safety performance?
Gulino: The first thing is to develop strong relationships and have good communication between the departments.
The second thing is understanding that many things don’t go as planned. You try one thing thinking it’s going to fix a problem, only to find that it has caused another problem to appear. So just be prepared for any aftereffects from any solution.
Stewart: We’re a very safety-focused and collaborative company where we’re meeting consistently for discussions on safety. We think it’s essential to involve all the stakeholders and get everybody’s opinions to ensure we’ve covered all our bases.
Mutual Assistance Drill at Rye Playland in Westchester on May 18, 2017.
- 4 Safety Tech Options to Consider for Aerial Devices and Digger Derricks
- Looking at Fleet Management Through a Legal Lens
- How Fleet Maintenance Can Advance Driver Safety
- Con Edison: Fleet Safety Performance is a Collaborative Effort
- The State of EV Wireless Charging
- Top Trends in Utility Fleet Maintenance
- 10-Point Checklist for Spec’ing Strobe Lights for Utility Fleet Applications
- Crash Analysis: A Personal Story
- 3 Books for Building the Right Habits for Growth in 2023 and Beyond