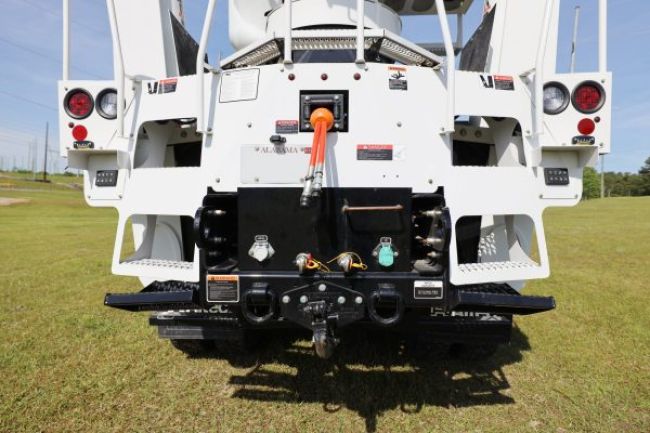
4 Safety Tech Options to Consider for Aerial Devices and Digger Derricks
As you spec your next round of bucket trucks and digger derricks, what are some safety technologies that may not have been available for your previous orders but are now?
UFP spoke with Altec’s (www.altec.com) Michael Newman, digger derrick market manager, and Ryan Hulleman, aerial device market manager, to get their advice. They recommended considering the following four safety tech options.
But before we dive in, a quick disclaimer: Although Newman and Hulleman speak specifically about their company’s products, you can look for similar safety systems from other manufacturers. This article aims to build awareness about the latest developments in safety technologies that can save lives, reduce job site injuries and extend the life of your equipment.
1. Lanyard Detection System for Aerial Devices
A lanyard detection system reminds lineworkers to clip in before they work from the platform. Altec’s system is available in two configurations. One provides an audible alert if the lanyard is not attached. The other disables the upper controls in addition to issuing an audible warning.
Why consider a lanyard detection system?
“Job sites are busy,” Hulleman said. “Workers are thinking about what they just talked about in their pre-op meeting or have other things on their mind. And folks can sometimes forget to clip in. So, this solution helps prevent somebody from getting into that scenario where they want to operate the equipment safely, but, for whatever reason, they forget to clip in.”
2. Load Monitoring
A load-monitoring system helps prevent overload incidents, extend equipment life and determine what adjustments need to be made to vehicle specs.
Altec’s system is connected to the company’s telematics offering that sends wireless notifications to fleet owners when a platform or boom overload event occurs.
Hulleman said that Altec’s system issues both visual and audio alerts. The visual warning is a four-color light bar attached to the unit’s turntable that changes color based on the load.
What are the colors?
“The visual indicator has four colors: blue, green, yellow and red,” Hulleman said. “Those colors correspond to a certain percentage of the rated load capacity. If the light is green, you’re in a good position. As you approach the total rated load, that color will change from green to yellow. Once you reach the rated load and slightly exceed it, you’ll see the red indicator on the light bar come on and hear an intermittent chirping alarm. If for some reason you were to worsen the overload, the light would turn blue, and you would hear that chirping sound become a solid tone. That indicates to the operator that the condition has worsened.”
3. Telematics
Telematics is nothing new for trucks. But receiving alerts remotely on the performance of truck-mounted equipment, like aerials and derricks – that’s a more recent development.
“Altec Insights is a digital [telematics] product for our physical products. It takes the raw data our customers may see as noise and processes it into consumable, actionable information,” Newman said.
What’s an example?
“Consider digger derricks with hydraulic overload protection, or HOP – a backstop system to prevent excessive machine overload,” Newman said. “The telematics insights come in to help determine the severity of the overload. This way, we can provide our customers with appropriate recommendations or actions. Depending on this situation, we might recommend the operator re-perform their daily inspection. Or, if they had a severe overload event, that might require a technician to perform a more detailed inspection.”
Telematics can also provide insight into whether to make specification changes. “You can look at this data to help make better decisions on whether a certain region or user group needs a larger machine,” Newman said. “We know the infrastructure is getting taller and heavier. So, our customers have to respond.”
4. Outrigger-Deploying Steps at the Tailshelf for Digger Derricks
This is an option on Altec’s new DT85 model digger derrick. The system enables the steps at the tailshelf to deploy and retract as the outriggers are raised and lowered.
How is it relevant to safety?
“The steps at the tailshelf make ingress and egress to the back of the truck bed much easier and safer for the operator,” Newman said. “If they didn’t have this step at the tailshelf, the operator would have to walk around the outrigger to where there is a dedicated set of steps or a ladder on the side of the bed. So, when you’re working on the derrick and rotated off the back of the truck, the tailshelf steps allow the operator to cut their steps in half to get to the ground. While that doesn’t sound like much, you’ve cut your risk significantly when getting in and out of the riding seat. The fewer steps on the truck mean a lower risk for slip-and-fall accidents.”
Why is it important for the rear steps to deploy automatically?
“It means that nobody has to remember to set up the steps and put them away when the operator is done,” Newman said. “The steps stow automatically at a good departure angle, so you’re not having to worry about someone forgetting that they deployed the step and tearing it off when leaving the job site.”
- 4 Safety Tech Options to Consider for Aerial Devices and Digger Derricks
- Looking at Fleet Management Through a Legal Lens
- How Fleet Maintenance Can Advance Driver Safety
- Con Edison: Fleet Safety Performance is a Collaborative Effort
- The State of EV Wireless Charging
- Top Trends in Utility Fleet Maintenance
- 10-Point Checklist for Spec’ing Strobe Lights for Utility Fleet Applications
- Crash Analysis: A Personal Story
- 3 Books for Building the Right Habits for Growth in 2023 and Beyond