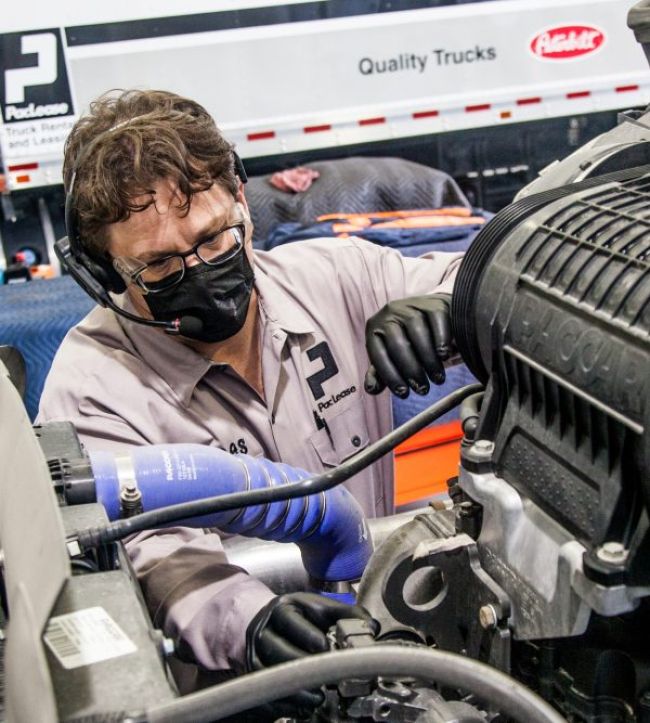
The State of Fleet Maintenance in 2023
While some familiar challenges will likely lessen this year, the technician shortage will remain a pressing issue.
The outlook for fleet maintenance costs and shop operations in 2023 is again influenced by the state of the economy and the supply chain, as well as by the ongoing nationwide tech shortage. To help pinpoint the leading challenges the year ahead poses to utility fleet managers, UFP spoke with Chris Foster, manager of fleet management services for Holman (www.holman.com), one of North America’s largest providers of fleet management services.
Supply Chain Kinks
Starting out with the remaining kinks bedeviling the supply chain, Foster pointed out that while “the entire automotive supply chain has been severely disrupted the last several years, there’s certainly positive momentum. That comes particularly in terms of new vehicle production, and conditions continue to slowly improve. The key to the supply chain beginning to stabilize has been the OEMs’ ability to steadily increase production capacity.”
Still, the supply chain was severely restricted during the first two to three years of the pandemic, which has prevented most fleet operators from being able to order new units, he pointed out. “As a result, older vehicles had to remain in service much longer than originally anticipated and needed additional repairs, quickly creating a parts shortage. Add to that the long-standing labor shortage and you quickly see the perfect storm of disruptions this creates.
“Today, as a growing number of new vehicles roll off the assembly line, fleets are able to begin replacing these older, high-mileage units, and this is starting to help mitigate parts and labor shortages,” Foster continued. “There are certainly still gaps in the market and lingering challenges, but generally speaking, the supply chain is headed in the right direction and will likely continue to improve throughout 2023.”
Costs: Up or Down?
Turning to which types of maintenance and repair costs are likely to increase or decrease the most in 2023, Foster said that for the last year or so, “supply chain disruptions, labor shortages and inflationary pressures have pushed operating costs significantly higher. In some segments of the industry and certain geographic regions, costs spiked as much as 20%.
“Fortunately, we’re beginning to see the industry stabilize, and price increases are leveling off a bit,” he continued. “As we look ahead, we’re likely to see maintenance and repairs continue to increase slightly in certain areas. Tire prices is one area that comes to mind, but costs are unlikely to climb at the same rate as last year.”
Techs Still Wanted
As for the technician shortage that predates the pandemic and has been growing steadily, Foster stressed that “without question, there is a critical shortage of qualified technicians throughout North America.” He said that puts the onus on utility fleets to recruit, develop and retain technicians to support their in-house maintenance programs.
Foster also observed that hiring skilled technicians is “a competitive process, and keeping them long term is often just as difficult. It is critical that you view your technicians as an integral part of your business and make their satisfaction, training and retention a top priority. Additionally, most utility fleet operators should leverage strong partnerships with their fleet management provider and/or external vendors to help supplement their in-house program and mitigate the risk of prolonged downtime due to technician turnover.”
Jeff Sproat, director of Wheels Donlen’s Maintenance Contact Center, contends that the rising cost of everything from fuel to tires, as well as the impact of widespread parts delays and labor shortages on shop operations, makes a compelling case for being proactive about maintenance.
“The first step in proactive maintenance is to understand the specific needs of your business,” he advised in a 2022 blog post. “You must know what kind of equipment you have and how it operates in order to make informed decisions about when to service or replace a system or part. By focusing on prevention rather than reaction when something goes wrong, you’ll increase uptime while saving money.”
Here is a condensed version of Sproat’s top five tips for leveraging proactive maintenance practices:
1. Assess your fleet. Align vehicle maintenance schedules with OEM guidelines that correspond to how your vehicles are being used. Check the OEM’s schedule recommendations against your usage patterns (e.g., whether a vehicle is being driven more often than average, has a higher number of stops-and-goes than normal, or is driven farther distances each day). In each case, more frequent service intervals may be indicated. Also, evaluate how long you plan to keep your vehicles to determine if any post-100,000-mile services should be scheduled, such as a transmission or coolant flush, or re-evaluated based on OEM recommendations.
2. Follow OEM guidelines. Sticking to OEM guidelines is a good way to reduce costs and keep your fleet running smoothly, especially when it comes to such aspects as routine maintenance schedules and maintaining fluid levels and tire pressures.
3. Check your drivers’ compliance. Are drivers performing their scheduled maintenance? Does it comply with local regulations? Is it in line with your fleet policy? If you find your drivers are continually getting services performed late, this can lead to higher repair costs as vehicles age.
4. Keep maintenance schedules current. Ensure you have the latest version of your vehicles’ maintenance schedules and service information, in addition to receiving any updates issued by manufacturers. The last thing you want is for an emergency to arise when no one knows how to respond.
5. Plan for planning. Fleet maintenance is a task that requires planning. It is important to understand how much maintenance work your fleet needs and when that work must be done. To gain that understanding, set aside time every year to complete an audit of all vehicles in your fleet to build a schedule for minor and major repairs.
“Don’t wait for a problem to occur; work with your drivers to schedule regular maintenance appointments,” Sproat wrote. “This will enable you to address minor issues before they lead to larger ones that could cost thousands of dollars and delay business operations. Not only will this ensure better safety but also lower costs in the long run.”
About the Author: David Cullen is an award-winning journalist who specializes in covering the trucking industry. Based in Connecticut, he writes for several business publications.
Image courtesy of Pac Lease
- What’s New in Truck and Van Upfits for 2023?
- Pitfalls to Avoid When Transitioning to a Fleet Management Information System
- Despite the Momentum for Electric Vehicles, the Future is Still Uncertain
- ATVs and UTVs: Minimizing the Hazards
- Work Truck Week 2023 Heads Back to Indy
- Spec’ing Truck-Mounted Air Compressors
- The Latest Developments in the Hydrogen Fuel-Cell Truck Market
- ‘The Checklist Manifesto’ for High-Performing Fleet Professionals
- 6 Lessons Learned (So Far) on the Fast Track to an All-Electric Fleet
- The State of Fleet Maintenance in 2023