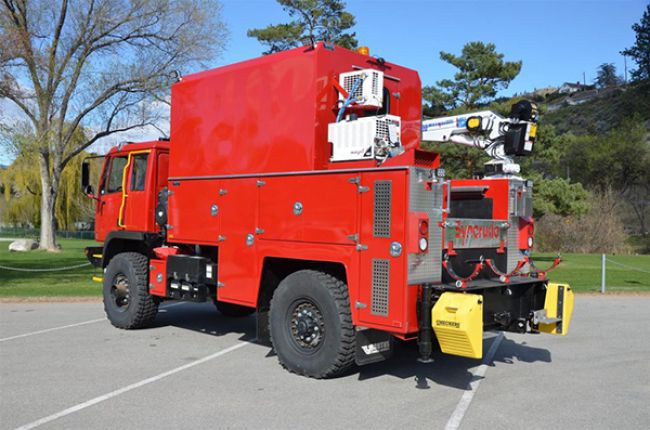
Spec’ing Truck-Mounted Air Compressors
Here are eight considerations for writing the best truck-mounted compressor specs.
Like most everything else that’s installed in the manufacturing and outfitting of a utility truck, there’s no one-size-fits-all choice when it comes to spec’ing a truck-mounted compressor to best meet the demands of a given application.
There’s a lot to think about, ranging from the compressor’s placement on the chassis to ensuring the correct flow rates. Insights for the following eight-point checklist to help fleet managers spec the right compressor are drawn from information from two leading air compressor manufacturers, Vanair (https://vanair.com) and VMAC (www.vmacair.com):
1. Consider all types of air compressors available. Namely, these are cross-mount, engine-driven compressors; engine-mounted, under-hood compressors; and PTO-driven, under-deck compressors. Vanair maintains that the latter is the most popular, as it offers the most power and largest range of CFM ratings (50-405). It can also be combined with a generator, or an SAE B pad to add hydraulics, or it can be a combination of all three.
2. Always calculate total operating costs. Bear in mind the total cost of ownership (TCO) may rise above the initial purchase price. And that TCO can add up depending on how many compressor-equipped trucks you operate. “The total life-cycle cost differential between compressor manufacturers can be measured in the hundreds of thousands, over 10 years, for most utility fleets,” according to Vanair. “Total life-cycle cost considerations must be given when evaluating bids.”
3. Figure on length of life cycle when spec’ing. Rotary screw air compressors have earned a reputation for long, durable life, with some seeing bearing life of over 100,000 hours. With the average vehicle life cycle being 10 to 13 years, expect under-deck air compressors to last well beyond that. Life cycle is a critical consideration when selecting a compressor.
4. Select for airflow. CFM stands for cubic feet per minute, a measurement of the volume of air moved. The correct CFM rating for a truck compressor is determined by calculating how much CFM is needed to run the pneumatic tools required for the job. That total must take into account whether the tools will be operating at the same time. The maximum airflow needed will determine the CFM rating to spec. For higher levels with more than one tool, the solution might be a spec calling for 185 CFM in a 100/150-psi dual pressure configuration. Keep in mind, too, that, according to VMAC, “CFM also correlates to price, the higher the CFM, the higher the price tag. For this reason, you want to choose an air compressor that will meet your demands without being too overpowered. However, if you have tools that … run above 90 psi, you’ll need to confirm the air compressor can handle it. Tools requiring 90 psi or more will likely need a two- or three-stage reciprocating air compressor or a rotary screw air compressor.”
5. Watch the weight. The gross vehicle weight (GVW) rating of the truck that the compressor will be mounted on is critical. A typical cross-mount compressor is large and heavy (2,400 pounds and up), takes up a lot of space, requires maintaining another engine and costs considerably more than a PTO-driven compressor. What’s more, because they require higher GVWs, a cross-mount unit might increase vehicle weight enough to require the driver to have a commercial driver’s license. In contrast, per Vanair, under-deck compressors are available at lower cost; require less space; are Tier 4 emissions-compliant; weigh only around 400 pounds; provide high reliability with typically 110,000-hour life design; make the truck more maneuverable with no towing; and can, for the same reason, lower insurance costs.
6. Power up. Most operators choose their truck-mounted air compressor based on the fuel or power options that are already on the truck, VMAC points out. “Operators who have trucks with hydraulic cranes tend to favor hydraulic air compressors. For trucks without hydraulics, it’s most convenient to match the air compressor to the vehicle’s existing fuel type.”
7. Factor in ambient weather, plus operating and duty conditions. Weather-related conditions can harshly impact system components. So, spec compressors and their mounting with an eye toward avoiding intrusion by water, ice and snow-control chemicals, and ensure ruggedness for any off-road operations. Where a truck works also matters because additional cooling or winterization may be needed in some parts of the country. Also, don’t overlook duty cycles. Per Vanair, powerful redundant transducer and thermistor systems are available to provide uptime, reliability and dependability for PTO-driven air compressors.
8. Throw away the old. Start fresh by first examining all that may have changed in the compressor marketplace since you last put out a bid; those changes might help boost cost-efficiency and productivity. Reach out to your compressor supplier and their competitors to learn what new features are available and their rationale for offering them. All the while, keep both the job requirements and total operating cost front of mind.
About the Author: David Cullen is an award-winning journalist who specializes in covering the trucking industry. Based in Connecticut, he writes for several business publications.
Image courtesy of VMAC
- What’s New in Truck and Van Upfits for 2023?
- Pitfalls to Avoid When Transitioning to a Fleet Management Information System
- Despite the Momentum for Electric Vehicles, the Future is Still Uncertain
- ATVs and UTVs: Minimizing the Hazards
- Work Truck Week 2023 Heads Back to Indy
- Spec’ing Truck-Mounted Air Compressors
- The Latest Developments in the Hydrogen Fuel-Cell Truck Market
- ‘The Checklist Manifesto’ for High-Performing Fleet Professionals
- 6 Lessons Learned (So Far) on the Fast Track to an All-Electric Fleet
- The State of Fleet Maintenance in 2023