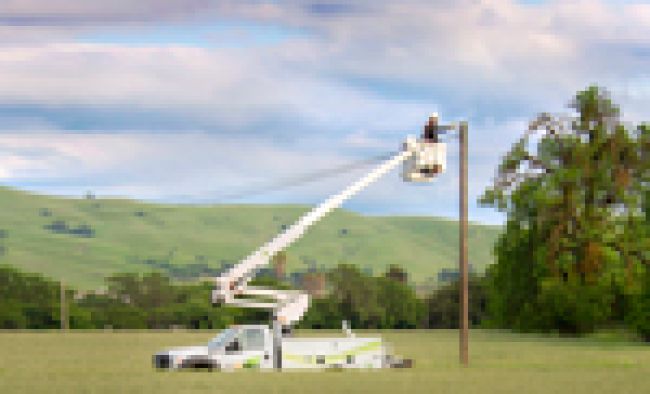
Three Mistakes to Avoid When Spec’ing Aerial Platform Trucks
Considering that aerial platform trucks, also known as boom or bucket trucks, often carry a hefty six-figure price tag, it pays to confirm that the chassis, body and aerial equipment specifications fit the job before issuing the purchase order. The stakes are high because spec errors result in disruptive downtime, lost productivity and increased safety risks, taking a chunk out of a fleet’s bottom line.
And fixing the issue isn’t as easy as picking up a replacement truck at the local dealer because turnaround time on these trucks – from purchase order to delivery – can take anywhere from six months to a year and a half, depending on market conditions and chassis manufacturer lead times.
So, how can utility and telecom fleets ensure that they craft a spec that suits the application – to enhance productivity, worker safety and profit per truck? Steer clear of these three mistakes.
1. Assuming yesterday’s spec will work today
“The replacement cycle on aerial platform trucks is easily a decade, sometimes longer. So a lot can happen since you last bought a truck,” said Dave Blanding, order technical support, Terex Utilities (www.terexutilities.com), a global manufacturer of aerial work platforms.
One area of change that’s often overlooked is the impact of new diesel emissions technologies, such as diesel particulate filters and selective catalytic reduction systems, on chassis weight. “Trucks are getting heavier, not lighter,” Blanding said. “And the heavier the truck, the less you can put on the truck and stay legal. The fleet could be in the position of not having enough truck to carry all that they need to carry if they haven’t thought through the changes in the chassis and adjusted the requirements accordingly.”
Another factor to consider is any change in utility pole setback – the distance between the pole and the road surface – since the last truck spec was written. “Today, with the way the roads are being designed with traffic safety in mind, roadside structures are being moved farther from the traveled road surface to avoid having cars come in contact with them, causing fleets to consider taller aerial devices with extended reach,” said Josh Chard, Ph.D., director of product and corporate safety, Altec Inc. (www.altec.com), an aerial equipment manufacturer and service provider for the electric utility, telecommunication, tree care, lights and signs, and contractor markets.
The impact on truck specs?
“While a company may have been able to get away with a 40-foot or 50-foot or 55-foot aerial [in the past], they may need a taller unit or one with extended side reach or both so they can get to the same work area they used to get to,” Chard said. “With telecom companies, they’re having to reach the same 20 to 25 feet they used to reach, but now they need to do it 10 feet farther off the side of the road.”
Also review platform capacity to ensure it’s current with how the vehicle will need to be used today. “The last time you might have spec’d a 300- or 350-pound [platform] capacity, but after a job or task analysis, you might find that operators also need to lift materials [inside the platform],” Chard said. “If the workers themselves combine for 300 pounds or more, they wouldn’t be able to take the tools up with them if the platform is spec’d at the same capacity.”
2. Underestimating functional and weight requirements
Here are common areas of under-spec’ing aerial platform trucks that put workers at greater risk of injury and can lead to premature truck repairs and shorter truck life.
Height and reach capacity. “The risk, if spec’d incorrectly, is that workers will try to extend the reach of the unit through some sort of alternative work practice at the job site, which is unsafe and unproductive,” Chard cautioned.
Payload capacity. “Sometimes the fleet doesn’t factor in the weight of all the gear that they’ll haul in the truck, beyond the weight of the body and aerial unit,” Blanding said. “They may not have taken into consideration that they need to put a 500-pound transformer on there. Or they haven’t thought about the generators, air compressors or water tanks [to wash down equipment] that will go on the vehicle. Water weighs 8 pounds per gallon. So if you have a 100-gallon tank, you have 800 extra pounds there. All that can add up fast.”
Trailering capacity. “Weight not only has to do with cargo,” Blanding said. “The truck often needs to tow something from time to time – whether a chipper or generator trailer or pole trailer. Fleets often don’t think about that roughly 10 to 15 percent of the trailer’s weight that will be borne by the hitch. So you may have a situation where the rear axle is in good shape until you put that trailer on.”
3. Spec’ing an aerial unit with too much height and reach for the job
More boom is better, right? Not necessarily. “You don’t want to buy the biggest unit if you don’t need it,” Chard advised. “Otherwise, you’re hauling all that weight of the extra boom, so you’re spending more money on fuel, and you’re having to buy a bigger chassis to carry that bigger [aerial] unit.”
Blanding agreed. “Don’t overreach. You may think it’s better to have a 50-footer instead of a 45-footer. If you don’t actually need it, don’t spend the money for it. And that’s also an extra 5 feet to have to deal with. It may mean that you have to change the truckload to accommodate that extra size and weight. You could run into a whole slew of issues that you don’t want to deal with. The assumption is that more is better, but more could be a start of a set of problems you didn’t anticipate.”
The Bottom Line
Match the spec to the job – no more, no less. “Work closely with equipment manufacturers early in the spec-writing process,” Blanding advised. “They will be able to walk you through the changes that have occurred since your last truck purchase and what adjustments in specs you might need to meet the truck’s job requirements moving forward.”
About the Author: Sean M. Lyden is a nationally recognized journalist and feature writer for a wide range of automotive and trucking trade publications, covering fleet management strategies, light- and medium-duty trucks, truck bodies and equipment, and green fuel technologies. He blogs at Strategy + Writing (www.seanmlyden.com).