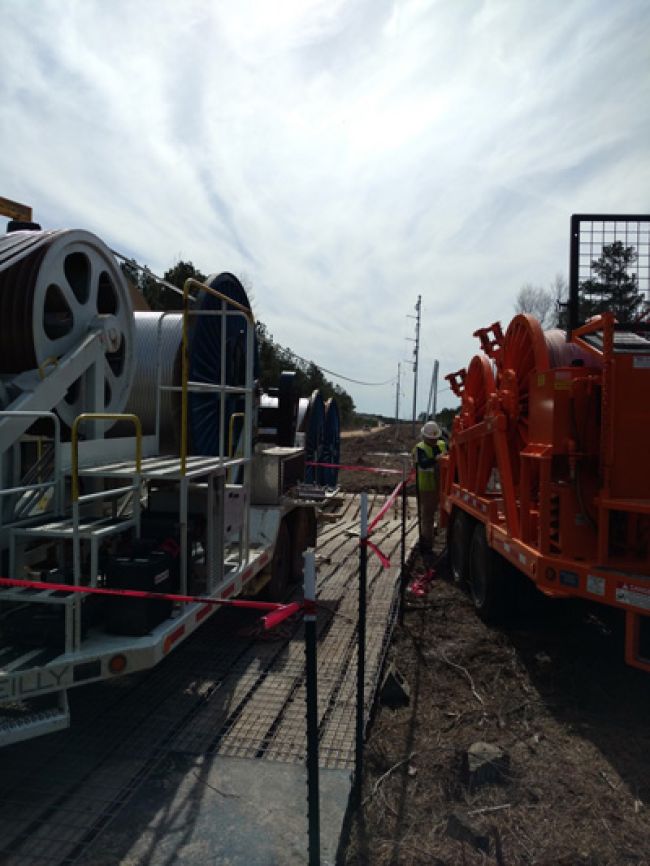
The ABCs of Grounding Mobile Equipment
Across our industry, I have found all kinds of policies for grounding trucks. I also have found that in many cases, employers’ rules for grounding trucks are not based on OSHA requirements and – even more concerning – are not based on sound principles of protection. I believe the grounding policies are well intentioned, but they fail to achieve two important goals: (1) meeting the OSHA standard and (2) protecting workers where electrical contact hazards exist. So, let’s take an ABCs approach to the issue because even though some detailed explanation is required, it really is that simple.
A Defensible Plan
You must be able to defend your plan or policy. This is the case for every plan or policy. Defense is built around establishing and accomplishing a goal, understanding the hazard, understanding the mitigation of the hazard, training at-risk employees, and conducting periodic audits to ensure the plan or policy is properly employed.
The Goal
In our case, the goal is protecting workers from electrical hazards created by contact with mobile equipment. Let’s agree here that mobile equipment is anything that is moved into a work site. In addition, it is mobile equipment that can become energized. If it can’t become energized, it is not a hazard.
Understanding the Hazard
The hazard is energizing mobile equipment and the transfer of hazardous energy to an employee who is on, in contact with or near the equipment that has become energized. The hazard involves unintended or inadvertent energizing. There can be several energizing sources, but we can classify them as follows: direct contact with an energized source, capacitive coupled voltage or inductive coupled current (I’ll explain this a little later), and inadvertent energizing by grounding to a current-carrying source. Let’s start with this one first.
The Rule
There is one rule – OSHA 29 CFR 1910.269(p)(4)(iii)(C) – that singularly establishes all of the employer’s responsibilities for protection of workers from electrical injury by contact with an energized piece of equipment. Paragraph 1910.269(p)(4)(iii)(C) requires the following: “Each employee shall be protected from hazards that could arise from mechanical equipment contact with energized lines or equipment.” The rule also requires that the “measures used shall ensure that employees will not be exposed to hazardous differences in electric potential.” Here we need to define “hazardous differences in electric potential.” It was probably written this way for clear understanding, but “electric” and “potential” are the same thing. The hazard of potential difference does not only come from contact with an energized line. OSHA does not define the mechanism of energizing except to say “mechanical equipment contact with energized lines or equipment.” “Energized” is a poor word choice because it may make the reader think of an aerial boom in contact with an overhead bus. That simple explanation does not take into account sources of steady-state current, such as inductive coupled current or even current coupled to a truck body by grounding to a current-carrying neutral.
Inductive Coupling Hazard
There are two forms of induction: capacitive coupling and inductive coupling. Capacitive coupling is an electrical charge onto an isolated conductive surface. There is no current component. With capacitive coupling, grounding the object that has received the charge will collapse (discharge) the voltage, and the voltage will not appear again as long as the surface is grounded. If the ground is removed, the conductive object will regain a charge. The speed at which the surface regains the charge is determined by the nearness and intensity of the electric field from the nearby energized line. With capacitive coupling, there is no current component because there is no complete pathway for a current to flow. You only have voltage, and you receive a shock if you contact that surface. There is very little risk associated with a capacitive coupled shock from a vehicle that is subject to mutual induction by a nearby electric field. However, if you ground equipment to a structure or a ground rod that is being used to control mutual induction, there could be a risk associated with inductive coupling.
Let’s use this example: At one structure, a crew with buckets aloft and a grounded bus have grounded their trucks to a ground rod that also is being used as the ground for the newly installed transmission conductors. Nearby in the same right-of-way is an energized 345-kV line. A span away, a second crew is aloft. The newly installed lines at that location are grounded to a rod installed at the foot of the new pole. Those two ground sources have created a path from the grounded bus to earth at the first structure, across earth between the two structures and up the second ground path back to the bus. Grounding at the two structures created a path for current to flow. It’s as basic as your introduction to electrical theory, using the loop from the battery’s positive terminal to the battery’s negative terminal, through a light bulb and a closed switch. A complete path is necessary for current to flow and the light to burn.
With inductive coupling, there must be at least two ground connections for current to flow. A single ground collapses the voltage so that it cannot be detected and no current flows. If a second ground path is connected, there is now a complete path to remote earth and – because of the adjacent ground – a path from ground, creating the looped pathway. If the magnetic field is strong enough, a current will flow through the two pathways, circulating in the pathway. There will still be no detectable voltage because it is a grounded circuit, but current will still flow in the pathway. This is circulating current (see IEEE 1048-2016, “IEEE Guide for Protective Grounding of Power Lines,” Section 42, “Induction”).
At the first pole, the crew grounded their truck to the ground rod that also was used to ground the newly installed bus. That bus was loaded with current because of mutual inductive coupling from the nearby 345-kV line and the completed pathway through the two adjacent ground systems. Grounding the truck to the ground rod put the truck in a parallel path to ground with the ground rod that was carrying induction current. That truck on rubber tires and outrigger pads becomes an isolated conductive surface. Because of the resistance between the truck body and the earth, there is a voltage in the gap between the truck body and the ground. The next worker who walks up to that truck and touches it will close the gap between the isolated truck body and ground with their body, risking a fatal injury. This scenario – a difference in potential – is one that OSHA requires us to control.
Grounding to the System Neutral
In Appendix C to 1910.269, OSHA answers the question as to what the agency means by “best available ground” for grounding trucks. The system neutral is the best available ground at most distribution work areas. It is a multigrounded continuous pathway that represents a very low-resistance path to earth.
The problem here is that the neutral, like the case of induction, represents a steady-state current source. Just as with induction, a truck connected to the neutral where current is present becomes a parallel path to ground. The body of the truck is at a different potential than the earth around the truck. So, is OSHA wrong? No, OSHA is correct. However, you have to understand the big picture to get this right.
Let’s start with the OSHA standard itself. Wherever OSHA requires grounding to protect employees from an electrical hazard, the rule always includes requirements to arrange the grounds so that no employee is exposed to a hazardous difference in potential. As mentioned earlier, 1910.269(p)(4)(iii)(C) states, “The measures used shall ensure that employees will not be exposed to hazardous differences in electric potential.” Paragraph 1910.269(p)(4)(iii)(C) is followed by paragraphs 1-4. Paragraph 1 requires “using the best available ground to minimize the time the lines or electric equipment remain energized”; paragraph 2 requires “bonding mechanical equipment together to minimize potential differences”; paragraph 3 requires “providing ground mats to extend areas of equipotential”; and paragraph 4 requires “employing insulating protective equipment or barricades to guard against any remaining hazardous electrical potential differences.” This is the definition of bonding and isolation to protect employees from differences in potential.
Grounding Does Not Ensure Protection
Grounding is for one particular purpose and that is to trip the circuit that is the source of energizing so that an unintended contact or inadvertent energizing does not occur. Bonding ensures that there is no potential difference that would create risk to the employee. Grounding does not protect the worker; bonding does, and it’s the law.
Federal OSHA Does Not Require Grounds
A warning here: I cannot address all state OSHA plans, and some may have mandatory grounding requirements. Even if they do, everything else here applies for the protection of the worker.
Now, back to 1910.269(p)(4)(iii)(C). This rule does not mandate grounding of trucks except under one condition. Read the whole rule in the breakout box below and notice the word “methods.” The rule requires that “the employer can demonstrate that the methods in use protect each employee from the hazards that could arise if the mechanical equipment contacts the energized line or equipment.” You have to interpret “methods” to create a defensible procedure to protect employees. What is a method? The rule doesn’t say to demonstrate that grounding in use protects employees. So, a method can be something other than grounding. Here’s an example: If touching a truck can get you electrocuted, a rule prohibiting touching the truck is a method of protecting the employee. There are numerous other effective methods available, such as positioning at setup, using dedicated observers and barricading. The requirement is that the employer can ensure the methods in use protect the employees. If the methods in use cannot ensure the protection of the employee, then (1) grounding, (2) bonding, (3) matting and (4) barricading are mandatory.
Step Potential
For those of you who have heard me address step potential, you know it is a very detailed recitation of the nature of the hazard, the history of research modeling and measuring, and a history of exposures and methodologies of protection. The problem is that theoretical modeling and measuring show a high degree of step potential hazard around an energized truck sometimes 30-plus feet away. The second part of the problem is that decades of experience among craft workers – and very few incidents of step and touch shock – say that isn’t the case. The result is an unwillingness on the part of industry to address the issue. OSHA expects you to have a plan to address step-and-touch hazards as shown in 1910.269(p)(4)(iii)(C)(3) (matting) and (4) (barricading), and as discussed in Appendix C to 1910.269. If you haven’t done so, you should read Appendix C and consider it well.
I know from experience that equipotential matting is a great way to ensure walking surface tripping hazards. Cattle panels are my favorite solution for step-and-touch hazards. I have used them extensively for 20 years and seen them in action. They work, but that’s a whole article in itself for another day.
Principles of Current in Grounds
Here are three valuable principles we need to understand to protect workers from electrical injury through equipment.
1. Current flows in every available path inversely proportional to the resistance of the path. That means everything you bond your equipment to – pole bonds, neutrals, statics, anchors on bonded guys – has a source of current that can energize a truck.
2. If you insert a resistance in a current-carrying path, a voltage will appear across that resistance. That means if you ground a truck to a current-carrying source, the truck is a parallel path. If that path is isolated by outrigger pads and rubber tires, a gap (resistance) exists between the truck and the ground, creating a potential difference.
3. If a potential difference is high enough to penetrate the resistance of a worker’s skin, current can flow, endangering the worker. That means that most exposures to a grounded truck in normal conditions may not be high enough to cause injury. But a fault current or high induction current coupled onto the truck can create a potential difference that could be a hazard. Those conditions can appear anytime.
The Bottom Line
You must assess the hazard of energizing trucks and the risk to your workers. You must have a plan to mitigate that hazard. You must train your employees on the plan and how to recognize the hazard. You also must train them to mitigate shock hazards according to your plan. If you ground trucks, you must have a plan to control exposure to differences in potential.
About the Author: After 25 years as a transmission-distribution lineman and foreman, Jim Vaughn, CUSP, has devoted the last 22 years to safety and training. A noted author, trainer and lecturer, he is a senior consultant for the Institute for Safety in Powerline Construction. He can be reached at [email protected].
*****
OSHA 29 CFR
https://www.osha.gov/laws-regs/interlinking/standards/1910.269(p)(4)(iii)(C)
Each employee shall be protected from hazards that could arise from mechanical equipment contact with energized lines or equipment. The measures used shall ensure that employees will not be exposed to hazardous differences in electric potential. Unless the employer can demonstrate that the methods in use protect each employee from the hazards that could arise if the mechanical equipment contacts the energized line or equipment, the measures used shall include all of the following techniques:
https://www.osha.gov/laws-regs/interlinking/standards/1910.269(p)(4)(iii)(C)(1)
Using the best available ground to minimize the time the lines or electric equipment remain energized,
https://www.osha.gov/laws-regs/interlinking/standards/1910.269(p)(4)(iii)(C)(2)
Bonding mechanical equipment together to minimize potential differences,
https://www.osha.gov/laws-regs/interlinking/standards/1910.269(p)(4)(iii)(C)(3)
Providing ground mats to extend areas of equipotential, and
https://www.osha.gov/laws-regs/interlinking/standards/1910.269(p)(4)(iii)(C)(4)
Employing insulating protective equipment or barricades to guard against any remaining hazardous electrical potential differences.
Note to paragraph (p)(4)(iii)(C): Appendix C to this section contains information on hazardous step and touch potentials and on methods of protecting employees from hazards resulting from such potentials.