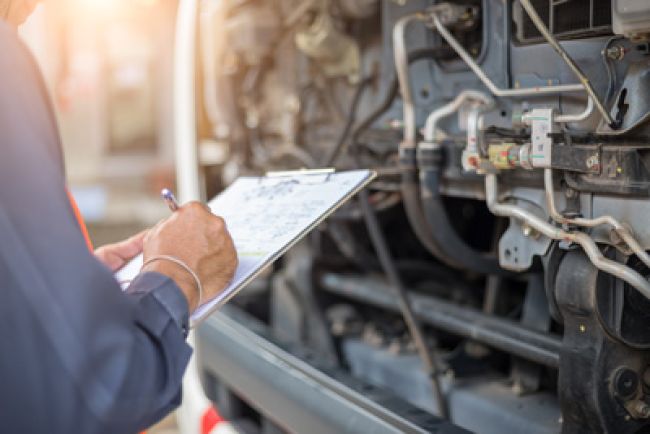
Shop Talk: Reimagining the PM as Predictive Maintenance
A thorough and consistent preventive maintenance (PM) program is a core best practice of any high-performing fleet.
But the challenge is that too many fleets still base their PM schedules on OEM recommendations and not on field-specific data that takes into account higher-idle scenarios, hilly terrain, extreme climate conditions and operator behaviors – all of which accelerate wear and tear on the vehicle.
As a result, you could achieve near 100% PM compliance per OEM schedules and still get blindsided by higher than acceptable failure rates that lead to costly downtime and productivity loss.
So, how can you improve maintenance performance?
George Survant, principal at Fleet Mace Consulting, recommended that fleets adopt a predictive maintenance model, which requires a different way of thinking and operating than traditional PM.
What exactly is predictive maintenance? And how do you execute an effective predictive maintenance program?
Here’s an edited version of my conversation with Survant, a fleet leader in the utility and telecom industry for over four decades, including stints at Florida Power & Light and Time Warner Cable.
UFP: How do you define “predictive maintenance”?
George Survant: Smart fleet operators start with their preventive maintenance routine, account for their specific operating factors and working conditions and the missions they’re using that truck for, and then evolve their PM program into a more complex maintenance routine with their own service intervals.
Now, predictive maintenance would say, “We know from our data that this water pump has a service life of about 3,000 hours.” Well, it’s prudent that if a water pump failure could lead to a significant downtime event or perhaps critical failure, then it makes good sense on your next service routine to replace that $500 part while you have it under your control. It’s already out of service, and you’re not in an additional productivity-loss environment.
So, predictive maintenance is maintenance that you take in anticipation of failure.
What’s an example of predictive maintenance in action?
Take, for example, the joystick on your aerial equipment.
Suppose the vehicle operates in South Florida, where there’s relentless UV light exposure. You can expect the rubber boot around the joystick to age and start to crack after year four. And by year five, that boot is now leaking water down into the control mechanism and shorting these things out.
So, rather than waiting for the failure to happen and replacing the whole $2,700 joystick assembly, let’s buy a new rubber boot and put it on every four years.
The point here is that, with predictive maintenance, you identify the root cause – the sun-damaged rubber boot – and then establish intervals to fix the issue before it leads to a much more costly failure.
How do you execute a predictive maintenance program?
The first step is to ensure accurate data capture.
Fleets that struggle with data capture often struggle not because the technician doesn’t know what failed. They can tell you what they had to replace and with great accuracy. But traditional shops very often have a clerk who inputs data from the technician into the maintenance system. And what happens is that it’s like watching a football game without the color commentator. You see it, but you don’t really understand what happened unless somebody gives you the detail. And all too often, the critical information gets lost in the translation.
With a more traditional maintenance model, where you didn’t really ask your technician to do the direct data capture, you struggle with understanding why you have failures. And if you can’t understand why something is failing, if you don’t understand that root cause, you don’t fix it correctly.
How do you ensure the data capture actually happens?
There are structures available that make it much easier for technicians to capture high-quality data. One is the American Trucking Associations’ failure code system, where you have an extensive array of codes for the power plant system, engine cooling system, exhaust system and so forth.
And the nice thing about the ATA model is that you can put a big laminated sheet up on the wall with the vehicle systems and the failure codes under those systems. The techs can look up the relevant codes and type them in, with no need for a lot of narrative or interpretation later.
When you analyze that data, what do you look for?
You look at the data and say, “Hey, we had this ATA failure code 66AB” – or whatever it was – and say, “All right, why is this part failing? Is it a design deficiency? Is it an application issue? Or is it a service issue?”
An application issue is where we’re using a truck in the wrong way, causing that part to fail.
For example, suppose you notice a spike in transmissions needing replacement. You look deeper into the issue. You notice that a common thread is that the trucks are going off-road, and the guys are getting stuck. If they’re rocking the trucks back and forth, putting a lot of punishment on the automatic transmission, they’ll burn up those transmissions pretty quickly.
So, a counterintuitive – and much less expensive – solution is to put a front winch on the truck, let them winch themselves out and leave the transmission alone.
Predictive maintenance is about understanding why you have the failure. Because once you frame the problem correctly, very often you will arrive at a very different solution that actually fixes the problem.