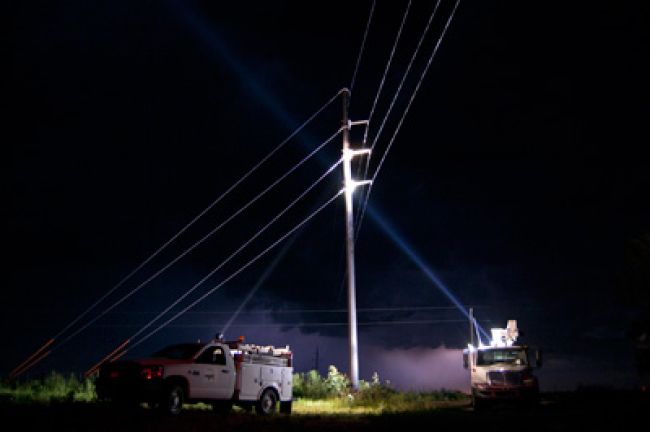
3 Factors to Consider When Retrofitting LED Lights on Work Trucks
It makes sense that most truck OEMs, body manufacturers and upfitters have made the switch from conventional incandescent bulbs to light-emitting diode (LED) lighting for their latest models.
After all, LEDs last exponentially longer, shine brighter, burn cooler and draw less power. And although LEDs are more expensive upfront, the cost drops significantly over the bulb’s life.
But what about the older vehicles in your fleet that still use incandescent bulbs? Would it pay to retrofit those lights with LEDs? How do you decide? And what factors should you consider before you make the switch?
UFP recently caught up with Ken Gillies, senior work truck consultant at Element Fleet Management (www.elementfleet.com), who offered these three considerations.
1. Cost benefit: Will the LED retrofit be a good investment for the application?
How much work will be involved? Will it be worth the cost?
“Is it a situation where you can do a simple plug-and-play LED switch-out? Or will it require a deeper look?” Gillies said. “This is critical because if you need to change a wiring harness, that will require more expenditure of labor hours and money. So, in some cases, you might want to ask, ‘If my [truck] body is X number of years old, and I’m considering doing a retrofit, how close am I to replacing the body?’ Maybe it doesn’t make sense to do a wholesale conversion. We could just switch the taillight bulbs or a couple of high-use compartment lights and leave the rest as they are.”
2. LED type: Solid state or resistor?
One of the least understood considerations with switching from incandescent to LED is the heat generated by the LED replacement, nullifying the benefits you’d expect from the retrofit.
“Depending on the situation, it might require a resistor to drop the voltage from the nominal 12 volts in the vehicle down to roughly five or six volts for the LED,” Gillies said.
Why does that matter?
“While it seems like the LED would draw less power, in some cases, it can draw as much power as the incandescent bulb. It’s just that some of that voltage needs to be converted downward. And that creates heat, where the LED light and fixture can run hotter than they did with an incandescent bulb,” Gillies said.
In what types of LED retrofit situations do excessive heat issues typically occur?
“It’s usually when you go with the less expensive LED replacement and try to use the existing style of the incandescent bulb as the connection point,” Gillies said. “Take a taillamp assembly, for example. It has small wires that extend around a plastic insulator base that plugs into the socket. Because of the voltage drop necessary for the LED bulb, that area heats up and starts to melt the plastic. The connection becomes loose, and you lose your light.”
The solution?
“Go with a solid-state LED bulb that doesn’t use a voltage resistor; they’re using switching technology with a microchip inside the bulb assembly,” Gillies said.
So, what exactly is the difference between a solid-state LED and one with a voltage resistor?
“With the solid-state bulb, the voltage drop is done with a microchip where it’s switching the power on and off electronically – and it’s so fast that it brings the overall voltage output down to the range needed without generating all the heat,” Gillies said.
How does that compare to LEDs with resistors?
“The resistor operates no different than, say, an electric stove, for example,” Gillies explained. “The coil element on the top of the stove is a resistor. And when you pump electricity through it, it heats up. The same thing happens with a resistor to drop voltage. It has to do something with that energy. So, it creates heat.”
The bottom line: If your retrofit objective is to improve performance, reduce the power draw (and heat), and cut the overall cost of ownership, go with LEDs that utilize solid-state circuitry.
3. Placement: Is the lighting designed with the operator in mind?
A common mistake that fleet managers make with LED retrofits is not thinking about how bulb positioning impacts the end user until the new lighting has been installed.
“I see this regularly where the LED’s placement is not optimized for the operator,” Gillies said. “They’ll have it mounted in such a way that when you open a door – whether it be to a cargo van, a utility body or crane body – the lights shine more in the operator’s eyes than they do in the cabinet.”
So, when you’re working with the upfitter to spec out your LED retrofit, what questions should you ask to ensure they mount the lighting at an angle that helps the operator – and doesn’t blind them?
“It’s a simple question of that supplier: ‘What are your considerations for the light’s mounting angle? Are you accounting for the possibility of the operator opening the door and getting a shot of that LED light right in the eyes?’” Gillies said.
How do you write that in the spec to make sure it gets done right?
“I would recommend writing something along the lines of, ‘Minimize the light that will be directed at the user’s face. Angle it for a view into the interior,’” Gillies said. “The simpler, the better. You could get into what specific angle it should be and all that sort of stuff. But, at the end of the day, somebody’s going to eyeball it when they put it in anyway.”
Summary
LEDs offer the promise of better lighting with fewer bulbs and greater energy efficiency. But when it comes to retrofitting LEDs on work trucks, one size does not fit all fleet applications. So, consider these three factors to realize the full benefits of LEDs in your next lighting retrofit.