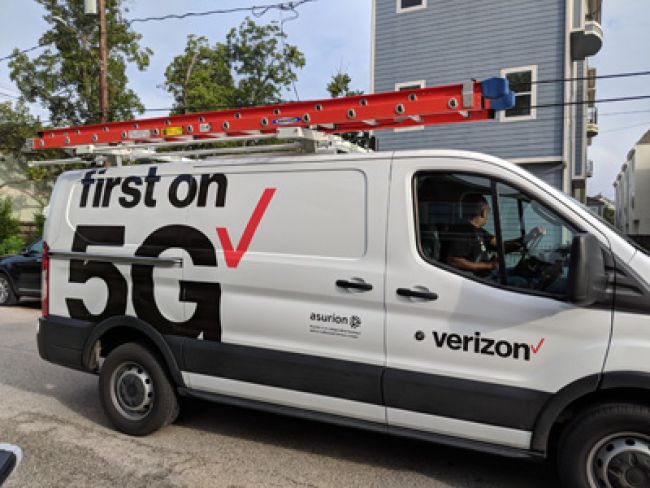
Shop Talk: Verizon Communications
In February, as the novel coronavirus spread overseas and cases began to trickle into the U.S., Verizon Communications, as a company, started grappling with how the pandemic might impact its operations.
“Before the media and most people were talking about what you should do, we’re thinking, ‘How would we operate? How do we keep our people safe?’” said Herb Pruitt, director of fleet operations for Verizon Communications.
UFP recently spoke with Pruitt to learn about the adjustments Verizon’s Fleet Operations team of over 400 employees, mostly mechanics, has made to ensure worker safety while maintaining a large fleet of about 29,000 vehicles during a pandemic. Here are the key takeaways from our conversation.
Home Garaging
One major change was a shift to home garaging. “The field technicians are ‘essential services’ and need to be out servicing customers,” Pruitt said. “So, we asked ourselves, ‘Can we lessen their exposure [to the virus] by not having them come to the garage at the end of their shift?’ This meant that our fleet would need to go from having vehicles parked at centralized locations, where the garages – the repair facilities – are, to being parked at home.”
But this new approach could create a logistics nightmare with scheduling preventive maintenance service and repairs if it’s not executed properly. “We knew we would need to really work smart to schedule those vehicles in this new environment,” Pruitt said.
That’s because, before home garaging, the field technicians would drive their vehicles during the day and park them at a facility, where the garage is, at the end of their shift. Then the mechanics would do the maintenance on those vehicles in the evening, without the end users having to take any action.
But now, drivers must be more deliberate about ensuring that PMs get done on their vehicles, and shop mechanics have adjusted their work hours.
Pruitt said that, before home garaging, nearly 90% of his mechanics worked the evening shift, which was either 2 p.m. to 10 p.m. or 3 p.m. to 11 p.m., depending on the location, because that’s when most of the work would get done.
Today, however, that ratio is closer to 60-40 – day shift to evening shift – with day shift hours being 6 a.m. to 2 p.m. or 7 a.m. to 3 p.m.
“We talked with our customers and asked, ‘What works for you?’ And many of them would say, ‘If the vehicle is parked at home, we’d prefer not having to drop it off at night.’ So, we made adjustments where we brought more mechanics to day shift to accommodate – to do more of the PM and repair work during the day at a time the field technicians could bring their vehicles in.”
Communication and Coordination
Despite the logistical challenges that come with home garaging Verizon’s tens of thousands of vehicles, Pruitt said that his team has still been able to achieve a PM compliance rate – the percentage of PMs completed by the due date – of 98%.
How? One reason, Pruitt said, is because of a greater emphasis on communication and coordination between fleet and the user groups.
“We send an email to the supervisor along the lines of, ‘These 10 vehicles need to come into this location within this one-week period of time.’ And then the supervisor directs their technician to that garage,” Pruitt said.
Those technicians can also use Verizon’s self-service app for scheduling repairs.
“They open the app from their tablet, smartphone or PC and put in their vehicle number,” Pruitt said. “There’s a box with systems and components listed – brakes, lights, windshield and so forth. They click on the relevant issue and there’s a subset of boxes that gets more specific. For example, if it’s a light, which light? Where? And then they type in specific comments for the mechanic. When they submit the request, they get an email confirmation that fleet has received it, and their supervisor gets an email confirmation that somebody on their team has submitted a work request.”
Each morning, Pruitt’s team reviews and prioritizes the work requests, assigns them to the appropriate mechanics, and schedules the repairs with the end users.
“If a dome light is out, it’s not really an imminent safety issue, but we need to fix it,” he said. “So, we’ll put that in the queue. But if someone submits a request along the lines of, ‘Brakes are spongy,’ we take the vehicle immediately out of service before we see or touch it.”
Shop Sanitization Safety
In a COVID-19 environment, it’s essential to effectively communicate new procedures and expectations when employees drop off their vehicles for service.
“When you come to the garage, there is no contact between you and the mechanic,” Pruitt said. “We are going to wipe down the high-traffic areas – the door handles, exterior, interior, seats, steering wheel and shifter – before we get into the vehicle. We perform the maintenance, service and repairs and repeat the wipe-down process before we give it back to the user group. We also tell the user group, ‘We want you to do the same thing when you bring in the vehicle – to wipe it down.’ This way, any time there’s a change of user of a vehicle, it’s wiped down.”
The Bottom Line
Pruitt’s advice to other fleet professionals as it relates to shop management in a COVID-19 world?
“First, focus on being excellent at the basics of fleet management because that gives you maximum flexibility when dealing with unexpected events like COVID-19,” he said. “When you’re properly managing your fleet with efficient day-to-day shop operations, developing effective relationships with your user groups, and setting high expectations around shop safety and cleanliness in normal times, you have greater capacity for dealing with situations like the one we’re in.”
And if you’re not sure what to do, reach out to your peers at other companies, Pruitt said. “I’ve been in [fleet management] for 37 years, and I don’t know everything. So, I pick up the phone and call people: ‘What are you doing? How did that work? Did you get the desired result?’ Sometimes I may continue in the direction I was headed. But many times, they either give me some advice that improves my idea, or I change course completely based on the advice they’ve given me.”