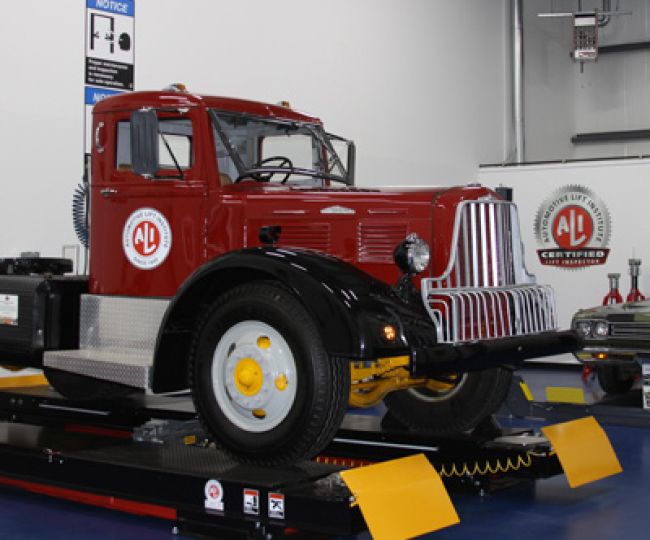
3 Pitfalls to Avoid When Purchasing Automotive Lifts for Your Garage
When operating heavy lifting equipment, like forklifts and cranes, there should be no one underneath the lifted load.
But there is one exception to that rule: automotive lifts.
“The automotive lift industry is the only one where operators are encouraged to go underneath a lifted load,” said R.W. “Bob” O’Gorman, president of the Automotive Lift Institute (www.autolift.org), a trade association of North American-based lift manufacturers that promotes the safe design, construction, installation, service, inspection and use of automotive lifts.
“For every other type of lifting equipment out there, the message is clear: ‘Don’t do it. Don’t get under that load.’ But in the automotive lift industry, the message is, ‘Go forth and perform your job with 10,000 to 50,000 pounds above you,'” O’Gorman said. “That’s why choosing the proper lift is so important – so that operators can feel comfortable in performing their jobs under such capacities.”
With a lot of money and your technicians’ safety at stake, O’Gorman recommends avoiding these three pitfalls when purchasing a new automotive lift.
Pitfall 1: Neglecting to spec an ALI-certified lift.
As you evaluate automotive lifts, beware of claims like “ANSI certified,” “Meets all ANSI standards,” “OSHA certified,” “Meets all OSHA requirements” and “Certification pending.”
According to the Automotive Lift Institute (ALI), those claims are misleading because ANSI does not perform product compliance evaluations, provide inspection services for hire or certify products. Neither does OSHA. And ALI’s certification program does not allow for any wording that indicates a certification of a lift model is pending.
The most stringent safety and performance requirements for automotive lifts are outlined in the current ANSI/ALI ALCTV safety standard.
But how do you know if a lift meets that standard?
Look for the ALI gold certification label.
“For any piece of equipment that is installed in the commercial workplace, like automotive lifts, there’s an OSHA requirement that the equipment be listed,” O’Gorman said. “And ‘listed’ refers to the electrical safety qualification of the product against known standards. So, for automotive lifts, big or small, that boils down to being an ALI-certified lift. The only way to know that lift in your shop is ALI certified is to go close to the [lift] controls and look for the ALI gold certification label.”
Keep in mind that ALI’s gold certification label pertains only to that particular lift model and does not necessarily apply to the lift manufacturer’s full product line. To search a directory of ALI-certified lifts, visit www.autolift.org/ali-directory-of-certified-lifts/.
Pitfall 2: Going it alone.
“If you haven’t considered the electrical requirements for more than 10 lifts, for example, and you wind up installing 14, you’ll significantly drive up the project cost in a manner that neither you nor anyone else had accounted for,” O’Gorman said. “You could blame your vendors all day long, but as the fleet manager, you’ll likely be the one held responsible.”
So, how do you minimize your risk of making costly errors? And how do you ensure that you’re installing lifts that best fit your garage operations?
“Build and work with an experienced team that can help you fully assess all your needs as you’re setting up a new shop or renovating or updating your lifts,” O’Gorman said.
Who should be on your team?
O’Gorman recommends including people from:
- Health and safety – either in-house or outside consultants.
- Operations – those who are going to manage the shop.
- Key management – someone who has visibility into where the shop needs to be in terms of capacity and efficiency, not only in the near term but also a few years down the road.
- An ALI member company – experts to help you match your objectives with the right equipment and investment.
The critical point here is to seek input from key stakeholders throughout the specification and purchasing process to help you shape – and sanity check – your lift requirements and point out any potential blind spots before investing in the equipment.
Pitfall 3: Overlooking training.
When it comes to putting a new automotive lift into service, don’t rely on technicians “figuring it out.” Instead, make sure your techs receive proper training on that specific piece of equipment.
“There are many lift manufacturers and distributors that will provide fleets with the training required for the safe operation of their equipment,” O’Gorman said. “But if you’re unable to get that training assistance through the vendor, you can reach out to an ALI-certified inspector who should be able to provide training as an extra service.”
To find an ALI-certified lift inspector, visit www.autolift.org/find-a-certified-auto-lift-inspector/.
O’Gorman said that ALI also has developed a general lift safety certificate program that can be taken online.
The Bottom Line
There’s a lot at stake when purchasing an automotive lift. As O’Gorman put it, “Would you want to send your employees under the cheapest lift you can find? Or, do you want to do your homework to make sure you’re sending your employees under a lift that you would go under yourself?”