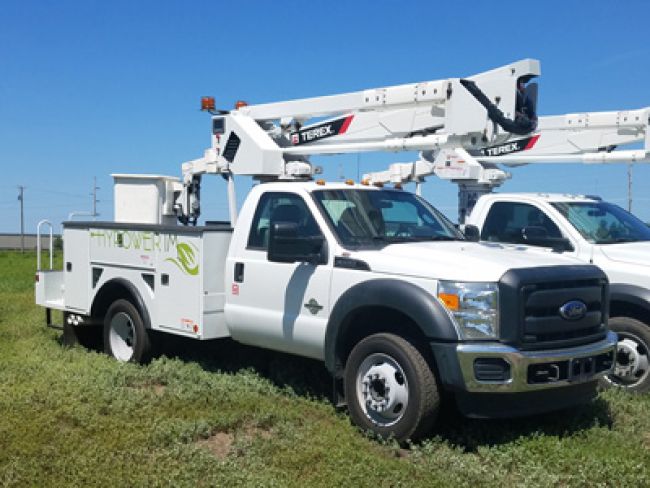
The Latest Developments in Idle-Reduction Technologies
Idling work trucks can be an annoyance to those who have to listen to them, damaging to the environment and, increasingly, they are unnecessary and undesirable in the field.
For one thing, the Environmental Protection Agency’s Phase 2 greenhouse gas emissions and fuel-efficiency standards for medium- and heavy-duty engines and vehicles will be in place relatively soon, impacting work trucks beginning with the 2021 model year.
But fleets don’t even need to wait that long to address the issues that idling vehicles present. Already, a number of new anti-idling technologies are ensuring that workers can do their jobs without their vehicle’s engine running.
While anti-idling technologies have been around for a while, the last year has brought several advances that are providing better results at a lower cost. Perhaps the greatest technology that could lead to successful adoption in the field is one that powers heating and cooling.
“That’s a neat next step,” said Bill Van Amburg, executive vice president of CALSTART (www.calstart.org), the nation’s leading clean transportation technology organization. “That has been a limitation. If you’re in a hot or cold climate, shutting down the engine is good. But you’re getting into a cold or hot cab. Who wants to do that? To be able to say, ‘You’ll not lose the ability to stay comfortable while doing your job’ will help people be willing to comply.”
He also has seen worksite idle-reduction technology in which the electronic control module offers a countdown of sorts, signaling the engine to shut off so that fuel can be saved and power can be drawn from batteries for use with power tools and cabin needs.
It is something of a sweet spot with anti-idling technologies. Rising diesel prices, advances in energy storage and cheaper batteries are poised to drive these technologies forward, Van Amburg believes. “Some of these systems were expensive when diesel was cheap,” he said.
Driving Down Costs
That is not the only cost of idling, of course. Today’s engines require maintenance based on operational hours, not miles – and idling can significantly drive that up.
“Idling is very hard on engines, on emission parts,” said Bill Needles, sales director for Stealth Power (www.idlereduction.com), which offers retrofit options that power auxiliary and hydraulic electrical loads without engaging the truck’s primary engine. “It really extends the preventive maintenance cycles out.”
Stealth works with partner Microsoft to power a data dashboard for each of its customers, detailing fuel savings, engine hours saved, maintenance savings and the reduction in carbon dioxide emissions.
The company is just starting to pursue opportunities in the utility industry with several alternative energy solutions. Its technology has been proven with emergency services like ambulances – which have their own need to power equipment when not idling – as well as military and long-haul trucking.
Stealth has installed systems on bucket trucks and other utility vehicles. Recently, the system has been upgraded with lighter batteries and components, pushing the technology further ahead, Needles said.
Another Option
While Stealth may be new to the utility industry, Terex’s HyPower has been on a “long journey,” said Ted Barron, vertical market manager for Terex Utilities (www.terex.com/utilities). “We have learned a lot with plug-in electric hybrid vehicles.” The company’s latest offering is the HyPower IM, which is currently available on Terex aerials with a platform height of 40 to 45 feet.
HyPower IM automatically switches from engine operation to battery and back again. “The logic in the control system knows when to utilize battery power and when to go to engine power in order to balance the operator’s requirements with the economic benefits of reducing idle time,” Barron said.
As Terex personnel talk to utility fleet professionals about their needs, they tend to request cabin comfort, lightweight solutions that maintain payload and sound reduction on the job site, Barron said. But foremost is the need for reliability – and much of that comes down to the battery.
“A big challenge OEMs face is the current availability of battery technology,” Barron said. “Cost, capacity, weight, performance in extreme temperatures, heat generated by the system and packaging considerations for installation on the truck chassis are all factors we must consider when designing emissions-friendly utility trucks.”
And while the last year has brought improvements, “there is a lag between those new technologies and a manufacturing-ready package,” Barron noted.
Ultimately, many technologies already are in place. Van Amburg pointed to the fact that a California-compliant engine is preprogrammed by the OEM to shut off after five minutes of idling. “The technology is there,” he said. “What we need to see is more fleet willingness to source it. They have to be convinced that there’s a payback for them.”
About the Author: Sandy Smith is a freelance writer and editor based in Nashville, Tennessee.
*****
Idle-Reduction Policies vs. Technology
For years, fleets have been encouraged to develop and adopt policies that require operators to shut off vehicles in certain circumstances.
But policies are only as good as their enforcement, said Bill Van Amburg, executive vice president of CALSTART. “If you have a policy to shut down the engine after 15 seconds, one minute, whatever, you have to track that and make sure it’s being followed. In the past, there wasn’t always the ability or willingness to track it.”
While telematics solves the ability issue, policies still come up short when compared to the technology. “What the technology now can do is take away choice in certain circumstances,” Van Amburg said.
At the end of the day, a technology solution “should be seamless and add value to the mission in order for it to be adopted and employed,” said Ted Barron, vertical market manager for Terex Utilities. “We believe it is better to employ technologies that allow the operator to concentrate on the job at hand, rather than on managing idling.”