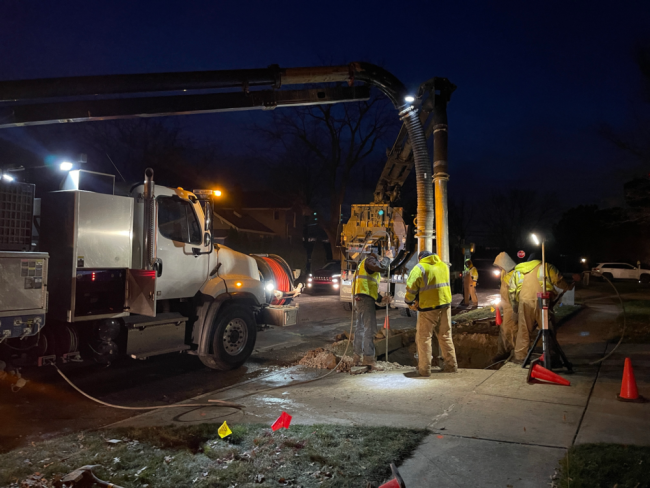
Spec’ing Truck-Mounted Compressors: Errors to Avoid
Two activities are critical to a fleet manager’s successful search for new truck-mounted compressors. First is gaining a full understanding of the application, vehicle constraints and long-term needs. Second is determining the correct specifications – based on the application – to ensure equipment performance, efficiency and longevity.
In a recent interview with UFP, Vanair’s John Dunn stressed that those fleet managers who have educated themselves about their operational needs and tool requirements have already taken an important step toward avoiding compressor spec’ing errors.
“Each company, each region and often the operators themselves work equipment a bit differently,” said Dunn, who serves as national sales manager, government/utility, for the mobile power solutions provider.
Variations in operational practices mean that fleet managers should gather as much detail as possible to select a compressor that fully meets operational needs. Specifically, here are three key questions to ask when assessing and comparing compressors:
- How long does the compressor run before shutting down? Operators who frequently “short-cycle” compressors may have different needs than those who run compressors continuously. This could influence the decision between purchasing a reciprocating or rotary screw compressor.
- What tools will be used, and what are their CFM and PSI requirements? Dunn said assembling a list of air volume and pressure requirements is a must.
- Is dual pressure required? Some tools need greater pressure than others, so a dual-pressure system may be necessary.
Space and Weight Considerations
Here’s another important question to ask: How much space do the trucks have available for compressors? As part of that evaluation, Dunn said, determine where the compressor will be mounted and whether the vehicle body needs reinforcement or additional room for air circulation.
Fleet managers also must consider compressor weight. A heavy compressor could lower payload capacity, reduce operational efficiency and lead to regulatory violations. A lighter compressor may help reduce vehicle weight and save cargo space.
Other Power Requirements
A full understanding of job-site equipment and power requirements is necessary to correctly spec compressors based on the application. Dunn recommended asking these questions: “Will the operator need AC electric power for lighting, drills or other tools? Or hydraulic power for cranes and heavy equipment?”
If the answer to either question is yes, a multifunctional power system may be necessary.
Also keep in mind that whether a compressor’s drive type is hydraulic, engine-driven, PTO-driven or electric, it must align with the vehicle’s other power needs. Dunn suggested that fleet managers identify which power type will be most effective based on the equipment’s use and duty cycle.
6 Common Mistakes
As noted above, a host of things must be done to properly spec compressors – but Dunn also highlighted these common errors that fleet managers should strive to avoid.
- Spec’ing too late in the vehicle planning process. Dunn warned that problems could arise if the chassis is ordered without any consideration given to the compressor, or if the body design doesn’t account for a compressor. It’s best to finalize specs in tandem with chassis and body planning.
- Neglecting space needs. Failure to provide proper airflow around a compressor can lead to overheating and reduced efficiency. Adequate air circulation is necessary for optimal functionality, especially in high-demand environments.
- Poor service accessibility. Don’t overlook how technicians will access a compressor to perform maintenance or repairs. Dunn stressed that ease of access can save valuable time and money.
- Ignoring the local climate. Compressors operated in hot climates may require additional cooling. Fleets that operate in colder regions should be aware that compressors could potentially freeze up; optional cold-weather packages can help with this.
- Overestimating air pressure needs. Increased air pressure doesn’t necessarily lead to improved performance. For example, a tool rated 90 to 100 PSI won’t always perform better at 150 PSI, and it may even fail prematurely. Be sure to match the compressor’s output to actual pressure requirements.
- Failing to plan for future needs. Fleet managers must be observant, regularly review their relevant data and plan for anticipated demands. If a crew currently uses a 125-CFM compressor but expects to take on more complex tasks that require an additional compressor and generator power, it’s wise to specify a higher-capacity unit that combines both functions.
Best Practices
Best practices guidance is one tool fleet managers can use to lower their risk of making spec’ing errors like the ones listed above. Dunn recommended these three tips:
- Engage with operators early in the spec’ing process with the goal of understanding when and how operators use compressed air and other mobile power in their daily work.
- Don’t assume more is better. As noted earlier, a larger compressor won’t necessarily offer improved performance. Fleet managers must focus on spec’ing compressors based on their specific task requirements.
- Collaborating with an equipment specialist early in the spec’ing process can help a fleet manager better refine their specs, increasing the likelihood that they’ll choose compressors that best meet the fleet’s operational needs.
By engaging with operators early in the process, planning for future requirements and avoiding common errors, fleet managers can position themselves to select the best compressors for their vehicles – helping to ensure optimal performance, reduced downtime and long-term operational efficiency.
About the Author: Grace Suizo has been covering the automotive fleet industry since 2007. She spent six years as an editor for five fleet publications and has written more than 100 articles geared toward both commercial and public sector fleets.
Photo courtesy of Vanair
- How to Get Rightsizing ‘Right’ for Your Fleet
- Reduce Risk with New Strategies for Operator Training
- Leading Change in Your Fleet
- On Your Radar: Four Fleet Maintenance Trends for 2025
- Spec’ing Truck-Mounted Compressors: Errors to Avoid
- Grid Capacity Tool Helps Fleet Managers Plan EV Charging Infrastructure
- The 4 Keys to Great (Fleet) Managers
- Navigating the EV Landscape in 2025: Top Trends to Watch
- New Offerings and Returning Favorites Headline NTEA’s Work Truck Week
- Work Truck Week 2025: Industry’s EV Enthusiasm Hits Reality Check