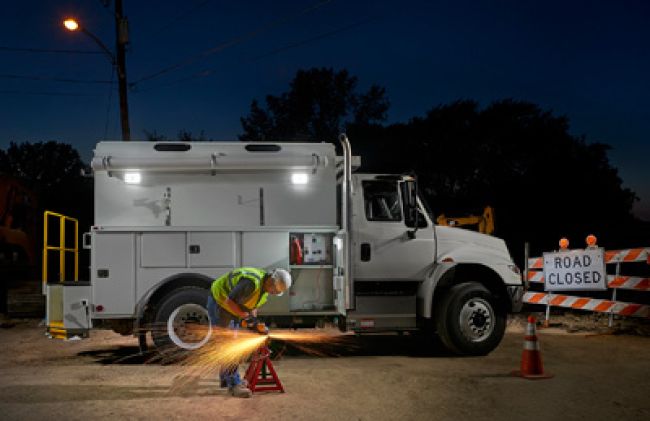
Spec’ing the Right Truck-Mounted Air Compressor for the Job
Today’s utility fleet managers have numerous options to choose from when it comes to truck-mounted air compressors. But how do you go about spec’ing the right one for the job?
One of the biggest mistakes that utility fleets make is using bid specs from previous years, according to Dean Gary, national sales representative for VMAC (www.vmacair.com), which designs and manufactures mobile air compressors and multipower systems.
Ralph Kokot, CEO of mobile power solutions provider Vanair Manufacturing (https://vanair.com), agreed. “Don’t assume what you put on your truck last time is what you should put on this time,” he said. “Before you start working on a bid specification for your fleet, reach out to the experts for guidance. Advancements are happening every day that increase ROI and productivity for your fleet.”
Both Gary and Kokot also shared some other helpful ideas for spec’ing the compressor that best suits your fleet needs.
Understand the Operating Environment
First, it’s crucial to understand the operating environment and conditions. Fleet managers must fully engage with their business units to understand operational field needs and work practices, Kokot advised. For example, he noted the significant weather-related differences between operations in Phoenix in August versus Alaska’s North Slope in January that could compromise system components.
“Arizona may require additional cooling, while Alaska may require winterization options,” Kokot said.
It’s also important for fleet managers to understand what type of pneumatic tools are being used and what CFM volume is needed. Gary recommended that fleets work with a qualified professional to determine the amount of air required to meet the needs of those pneumatic tools as well as the duty cycle and climate they’re operating in. Kokot said Vanair currently offers an air tool consumption guide to help with this.
“For example, a 90-pound pavement breaker consumes approximately 70 to 85 CFM at 100 PSI. Are multiple tools being used simultaneously? If the crews are using more than one pavement breaker, the minimum compressor spec would be 160 CFM. Are the crews pressurizing services and mains? If so, 185 CFM in dual pressure 100/150 PSI might be in order,” Kokot explained.
Convenience and Other Factors
Gary noted that VMAC has seen “a significant trend of customers switching from tow-behind air compressors to UNDERHOOD compressors.” That’s primarily due to convenience – an UNDERHOOD compressor is always in the truck, so there’s one less engine to maintain and one less piece of equipment to haul around.
Beyond convenience, compressor weight and cost are critical factors to consider in the spec’ing process.
“A typical cross-mount compressor is large and heavy, weighs over 2,400 pounds, takes up considerable real estate on the truck and entails another engine to maintain, plus it costs twice as much as a PTO-driven compressor,” Kokot said.
He noted that underdeck air compressors appear to be the most popular with utility fleets, emphasizing that the advantages of such compressors are significant. They offer a lower cost and Tier 4 compliance, free up valuable room on the vehicle, and are lower in weight with high reliability and durability. PTO underdecks meet higher CFM outputs, from 50 to 200 CFM, and are designed to run at the lowest engine speed, reducing noise and fuel consumption.
“Integrating a PTO underdeck air compressor onto the truck chassis turns the vehicle into a vital tool for gas, electric, telecommunication, water utilities and utility contractor companies,” Kokot said.
For one VMAC utility customer, switching to an UNDERHOOD air compressor helped solve its space and weight challenges. The utility crew wanted more space on their trucks and something more compact and lightweight than their bulky diesel-driven air compressor. The under-the-hood placement of the VMAC air compressor resulted in thousands of pounds of weight savings and about an extra 3 feet of storage available in the back of the truck, according to VMAC.
About the Author: Grace Suizo has been covering the automotive fleet industry since 2007. She spent six years as an editor for five fleet publications and has written more than 100 articles geared toward both commercial and public sector fleets.
*****
Common Spec’ing Errors to Avoid
It’s important for fleet managers to know what to look for in a truck-mounted air compressor – but understanding what not to do also can prove helpful.
A common mistake fleets make when spec’ing a compressor is basing the decision strictly on the upfront cost of the unit without looking at the life-cycle cost or application, according to Dean Gary, national sales representative for VMAC.
Ralph Kokot, CEO of Vanair Manufacturing, said total life-cycle costs must be taken into consideration when evaluating a possible purchase.
“The total cost of ownership can be more than the initial purchase price,” Kokot explained. “Many utilities have 20, 50 or even hundreds of compressor trucks. The total life-cycle cost differential between compressor manufacturers can be measured in the hundreds of thousands and, moreover, 10 years for most fleets,” Kokot said.
Fleets also must stay up to date on the latest equipment advancements, sometimes making the mistake of not knowing about or fully understanding recent advancements and improvements designed to help eliminate downtime.
“If the job gets shut down, you’ve got downtime and idle workers. It can equate to thousands of dollars per hour in downtime or worse,” Kokot said.
Redundant thermistors and transducers are one example of technology that may not be widely known about.
“The dual-sensor redundancy option provides backup if a fault exists on the primary transducer and thermistor, for uninterrupted operations,” Kokot said.