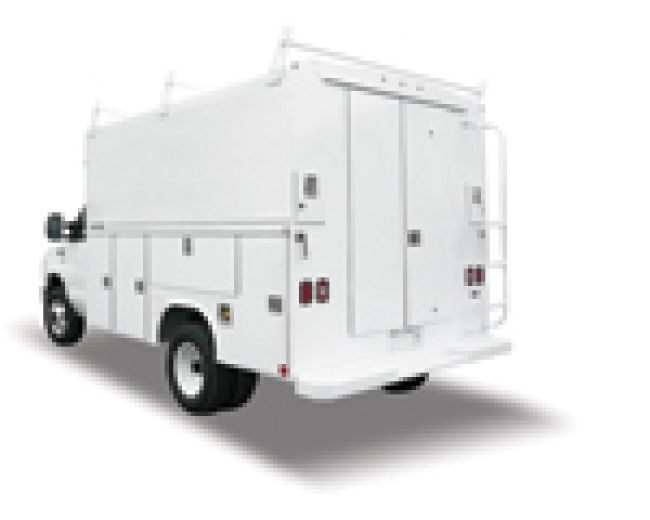
Spec’ing Service Bodies to Boost Productivity and Profit in Utility Fleets
Service bodies, also known as utility beds, mounted onto light- and medium-duty truck chassis provide utility contractors with easy and secure access to their tools, equipment and parts to do their work more efficiently – and profitably.
That is, if the body is spec’d properly for the job. If you’re replacing an existing service body truck, keep in mind that yesterday’s spec may not be optimal for today’s work, potentially impeding driver productivity and increasing fleet operational costs.
“Don’t assume that duplicating the old truck that’s being replaced is the right thing to do,” cautioned Jim Palin, senior truck applications engineer for GE Capital Fleet Services (www.gefleet.com). “Fleet managers need to get down to the driver level and make sure the job function hasn’t changed. And if it has, revise the body spec accordingly.”
How do fleet managers sort through the various body configurations, materials and other options available to ensure their service body spec best fits the job? Follow these three steps.
1. Begin with the truck’s role in mind. What function is the truck expected to perform? Will the truck include body-mounted equipment such as an aerial bucket or telescopic crane? Or will it carry smaller tools and parts? Will it need to haul ladders or wire spools or compressors? What is the expected maximum payload?
Answers to questions like these will help you nail down the big picture of your truck and service body requirements, including:
- Chassis selection based on gross vehicle weight rating.
- Chassis length in terms of inches between cab-to-rear axle.
- Body dimensions and any provisions for mounted equipment.
2. Dig deep for the details. “Seek feedback from drivers,” Palin advised. “You want to drill down to the granular level of how drivers use the truck to do their job to ensure the body is configured to support their work – to equip them to be as productive as possible.”
Craig Bonham, director of business development at The Reading Group (www.readingbody.com), a truck body manufacturer based in Reading, Pa., agrees. “[Drivers] have a lot of different parts and things that they utilize on the service line and so they have different requirements, ranging from a different size door to a way the shelf may be angulated for easy [part] retrieval,” Bonham said. “Sometimes these vehicles work in the evening, so they may want rope lighting inside the cabinet network. Since utility operators are in the load space of the truck bed more often than your common contractor [to access the aerial device, for example], the ease of getting in and out of the load space has to be a priority. You could have a stairwell built into the body, which makes getting up into the body more ergonomically friendly. There are also grab bars and nonslip surfaces to consider because safety is a very, very strong focus involving utility and aerial devices.”
Another important factor, said Eric Paul, vice president of sales and marketing at Fort Worth, Texas-based BrandFX Body Company (www.brandfxbody.com), is the location of the body compartments. “If you’re an infrastructure worker or utility worker that works in a metropolitan area, chances are you will want the tools and products you use most of the time on the curb [or passenger side] of the vehicle. The reason for this is so the operator is not working on the driver side of the vehicle, where there is traffic on the major thoroughfares.”
Also account for any off-road use, advised Bonham. “The body has to be installed in a way that allows articulation of the chassis frame while also protecting the body from structural failure when operating off-road,” Bonham said. “The solution, in many cases, is to spring-mount the body. This method allows proper chassis frame articulation in unimproved road surfaces and helps to eliminate permanent structural deformation to the body structure.”
3. Evaluate the cost benefit of lightweight materials for body construction. Most service bodies continue to be built out of conventional steel because of its attractive price point and reputation for durability. But lighter-weight materials, such as aluminum and fiber composite – heavy-duty fiberglass laid over a durable foam core – have gained momentum and market share in the service body market as fleet managers seek ways to improve fuel economy and squeeze more cost savings from their operations.
“Service body specs for bid often only include steel. But if you can achieve 40 to 50 percent weight savings, fleet managers would be negligent not to scrutinize the spec,” Paul said. “If you take 50 percent out of the weight of the body structure, theoretically you can choose a lighter powertrain or [more fuel-efficient] rear axle. Or it could mean that you spec it out on the same size vehicle, but up your payload, which means you can stock your trucks heavier – and that means fewer trips back to dispatch.”
Both fiber composite and aluminum bodies also tend to be more corrosion resistant than steel, offering fleets a longer service life. “Whereas several years ago, many utility fleets were leasing trucks and turning them back in every five to seven years, we have seen a very big departure from that in the past four years [due to the economic downturn],” observed John Dunn, director of utility services with The Reading Group, which manufactures steel and aluminum service bodies. “Most of these fleets are keeping their trucks as long as 10 to 12 years. And because of that, [corrosion-resistant materials] are a better fit for many of these fleets to ensure the bodies will last.”
A key question to ask is this: Will the higher upfront cost of lightweight materials – versus steel – be offset by potential savings generated by longer life cycles, improved overall fuel economy, downsizing the chassis or increasing body payload? Run the numbers for your application. In a low-mileage scenario where the truck is expected to be replaced within five to seven years, steel may remain the more economical choice.
The Bottom Line
Define the job description for each service body truck. Then ask, how can we spec this truck and body in a way that equips our drivers to do that job faster, safer, with maximum fuel efficiency and at the lowest possible vehicle acquisition cost? Develop a service body spec that achieves all these objectives to squeeze more productivity – and profit – from your fleet operations.
About the Author: Sean M. Lyden is a nationally recognized journalist and feature writer for a wide range of automotive and trucking trade publications, covering fleet management strategies, light- and medium-duty trucks, truck bodies and equipment, and green fuel technologies. He blogs at Lyden Fleet Strategies (www.lydenfleetstrategies.blogspot.com).