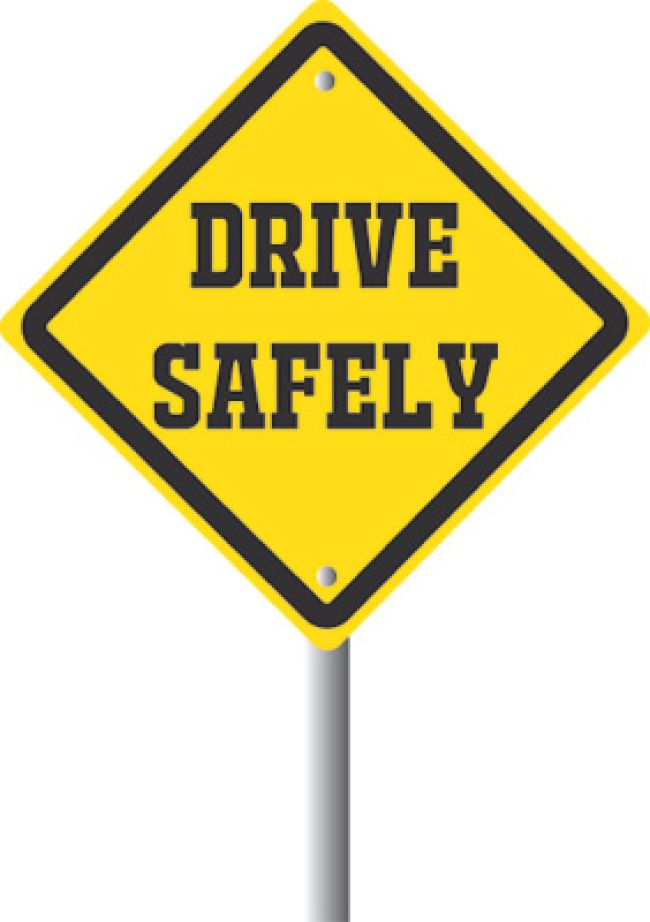
Preventing Future Driving Incidents
Fleet management economics are not just about predictive scheduling, inspection and maintenance. Yes, you can predict and control operating costs by keeping and analyzing records. But one thing you can’t do is predict accidents, other than predicting you will have one at some point. However, accidents – especially expensive ones – don’t have to be an unpredictable liability. In fact, most accidents don’t have to happen at all, although sometimes we as managers enable them.
A few years ago, I got a call from the sheriff of a small town in Tennessee. I was working for a contractor at the time, and one of our trucks had been found on its side in the trees off a small two-lane road. The cab was crushed and our driver was deceased, his body trapped in the wreck for several hours. This was not just a matter of having to cut away the cab. The driver, who was not wearing a seat belt, had been thrown below the steering column in the crash. The cab folded in and around him, and the truck was a total loss.
The reason I chose this story to make the following points is due to how the incident played out within the organization. Everyone was devastated by the loss of the driver. That was expected. But after a few weeks, the incident became the focus of accounting, and that’s when the safety department came under scrutiny. That’s because the highway patrol had completed the incident investigation, and they discovered three enabling elements that – had any of them been changed – would have prevented the accident from occurring. The driver would not have died, the truck would not have been totaled and the financial loss would have been avoided.
These three elements won’t be common to all incidents, but I’ve detailed them here to demonstrate to readers that most incidents are avoidable. In addition, I’ve also identified some cultural initiatives that can prevent the enabling of future incidents.
Element 1: The Route
The truck was a Freightliner twin-axle, 20-ton digger derrick. There were three main routes from the yard to the project site. It was 7:45 a.m., and the driver voiced concerns about traffic. According to his crewmates, he knew a faster route that was rarely used and would bypass the morning traffic. So, what was the value of the time saved? The incident investigation indicated the backroad route could have saved time only if the 35-mph speed limit was exceeded by 30 mph. The other two routes – an interstate and a four-lane highway – had fewer turns, fewer stops and speed limits of 55 to 65 mph. Perhaps more important was the construction of the roadways. In addition to having fewer turns, the two higher-speed highways had shoulders that varied from 26 inches at the narrowest to 96 inches at the widest. The shoulders became the most important issue because the rural road the driver had chosen had no shoulder. In several places, the road dropped off into rocky ruts just inches off the white line. The highway patrol’s analysis of the cause of the incident was that the right front wheel of the digger derrick dropped off the road into a rut, causing the driver to lose control of the vehicle.
Element 2: Seat Belts
There was never any doubt that the truck driver lost control of the vehicle. A FedEx driver following the truck prior to the crash said the truck lurched to the right and continued to pull farther down the slope until it careened left back toward the highway. The crash analysis indicated the truck’s path clearly followed the FedEx driver’s description. When the truck re-entered the highway, it entered at an angle almost 15 degrees out of line. The re-entry was so hard and fast that the truck went airborne for 22 feet, and then bounced and careened onto its side before plowing into the trees. Evidence from the crash analysis also indicated that the driver never touched the brakes and that, once the turn back toward the road was made, no effective driver control was maintained. Because the driver was not wearing a seat belt, the movement of the cab dislodged him from behind the seat at some point after the vehicle had left the road.
Element 3: Driver Fitness
The autopsy of the driver indicated he likely was impaired by drug use at the time of the incident. The yard where the driver worked from was a small operation in a small town. Everyone knew each other, and in fact, three of the office employees, including the local manager’s secretary, were related to the driver who died in the crash. That may have played a role in the employer’s failure to remove the driver from safety-sensitive functions when it was discovered that he had become addicted to opiates following a back injury the year before. The manager of the operation learned that the driver was abusing opiates when police had come to serve warrants a month earlier. A local pharmacist had discovered that the driver was seeing several doctors and getting hydrocodone prescriptions from each of them. Had the manager reported the discovery to the employer’s DOT manager, the driver would have been removed from safety-sensitive duties and would not have driven on the job again until he had received the help he needed for his condition. It is certain that, had the proper action been taken, he would not have been driving that day.
Driver Safety Training
This sad story becomes even more unfortunate when we realize that simple pre-emptive steps could have prevented it. How many drivers do you have who don’t use seat belts? How many of them know that if you can’t stay behind the wheel, you can’t maintain control of the vehicle? How many of them realize how violent a ride becomes when a truck gets out of control? There is no reason for any employer not to have control of seat-belt use by drivers, but it is one of the top driver-safety deficiencies found in third-party safety audits of utility drivers.
Drivers and DOT compliance officers know the rules, but do your managers? Managers, supervisors and foremen should be given annual refreshers on DOT policies beyond the required reasonable-suspicion training. Supervisory staff also should be aware of DOT requirements for carrier registration, driver qualification and employer/driver policies. Your supervisory staff is the front line. They are the ones who interface with the workforce and are more likely than anyone to be the first to witness risk behaviors that indicate problems.
Driver safety training is key at companies with the best driver performance. This training is not about smooth shifting, inspections or hours-of-service logs. Driver safety programs can be as rigorous as the Smith System or as simple as offerings from your insurance company. Your drivers may be professionals, but that doesn’t mean they have a natural capacity for recognition of risks that can be avoided. Good choices by drivers improve the safety aspects of operating on the road. Drivers need to operate in an environment of control and avoidance. Training to achieve that in your driver force is not difficult or expensive. In the long run, it will be far less of an expense than the next avoidable crash.
About the Author: After 25 years as a transmission-distribution lineman and foreman, Jim Vaughn, CUSP, has devoted the last 20 years to safety and training. A noted author, trainer and lecturer, he is a resident subject matter expert for the Incident Prevention Institute. He can be reached at [email protected].