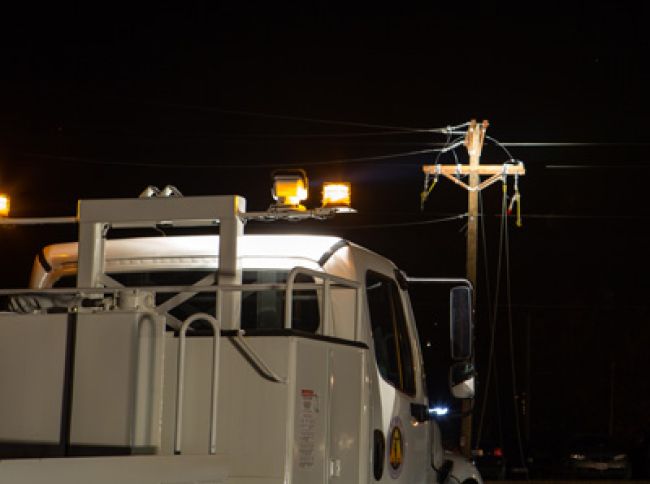
Making the Switch to LED Lighting in Utility Fleets
Lighting via the use of light-emitting diodes – more commonly known as LEDs – has been around for over five decades. But only in recent years has the technology surged in popularity, especially among utility fleets.
According to the U.S. Department of Energy, LEDs use 75 percent less energy and last 25 times longer than conventional incandescent lighting. That’s a big difference in terms of energy consumption and longevity. But historically, LEDs have been too expensive for fleets to justify making the switch.
That is, until the past five years or so, as the price gap has narrowed significantly, presenting a more compelling business case for fleets to convert to LEDs.
Getting Started
Take PPL Electric Utilities based in Allentown, Pennsylvania, for example. The fleet department began to expand its use of LEDs in 2014 for safety reasons.
“Our initial push was the safety factor of the brightness of the LEDs for better visibility when working at night,” said John Adkisson, transportation manager at PPL. “And the prices were starting to come down at that time, making LEDs more prevalent. So, we decided to give it a shot and see how it goes. So far, the change to LEDs has been well-received by the operators and the crews.”
Dale Collins, fleet services supervisor at Fairfax Water in Fairfax, Virginia, said that his organization started spec’ing LEDs on a larger scale about seven years ago.
“The lower power consumption [with LEDs] was a no-brainer,” Collins said. “We could get better illumination and more reliability with less power. This way, we could use the lights without draining the battery or having to idle the engine, which saves fuel.”
What’s the difference in power draw between LEDs and conventional lighting systems in a real-world setting?
“In an LED strobe, the power draw is about 2.5 amps. But a conventional strobe with a power unit could draw anywhere from 8 to 12 amps,” Collins said.
And that difference in power consumption directly impacts crew productivity in the field.
That’s because, if your first-responder vehicles, for example, are equipped with conventional strobes, you’ll need to idle the engine to keep those warning lights on or you’ll drain the battery quickly.
“You better get back to start that engine up in about 20 minutes or the truck is going to fail to start,” Collins said. “But with LEDs on our crew trucks – and I’ve tested it myself – I can turn on all the ancillary lights, warning lights, compartment lights and everything else and shut the engine off. And four hours later, I can come back and still be able to start the truck up.”
LEDs also offer significantly better visibility in daylight than their conventional counterparts, which is an important safety consideration for vehicles with strobe or beacon warning lights.
“You have service tech vehicles with a beacon light on the vehicle to let other drivers know that the vehicle is stopping and starting,” Adkisson said. “The rotary beacons [equipped with conventional lights] aren’t as effective during the daytime – because they’re harder to see in sunlight than they are at night. But with an LED light, whether it’s day or night, you can see it flashing with no problem.”
Opportunities for Conversion
So, for what applications does it make good economic sense to switch to LEDs? Here are four to consider.
1. Warning lights.
“We use LEDs a lot in any vehicle that requires a strobe light, like the amber strobes that you put on, say, pickup trucks or the SUV-type vehicles for the meter readers,” Adkisson said. “The LED systems are programmable and don’t have the failure rates that we saw in the old rotary beacon lights.”
2. Electrified trucks.
Adkisson said that LEDs work well for electrified trucks, such as those equipped with electric power take-off systems, because they provide maximum light for crews in the field while minimizing the drain on the battery, allowing crews to work longer on all-electric power.
3. Workspace lighting.
“We use LEDs for scene lighting on our bucket trucks to provide lighting to the ground or on the deck at night,” Adkisson said.
Besides offering better visibility in the field at night, LEDs also emit very little light in the UV spectrum, which makes them less likely to attract insects in the summertime.
“[Not attracting bugs] might seem like a small benefit, but there’s something to be said for it, especially when your crews are working in an insect-rich environment,” Collins said.
4. Portable shop lighting.
“It’s easy to think that LEDs are just for the vehicle, but the shop is an area of opportunity to use LEDs that we don’t typically think about,” Adkisson said. “LEDs can have the same safety and productivity impact in the shop as they do in the field. And when you think about it, LED flashlights and droplights are not that expensive.”
The Business Case
How much more do LEDs cost upfront compared to conventional lighting systems? And what kind of payback can you expect?
“When we first started purchasing LED lamps [about 2011], they were considerably more expensive, costing at least a third – if not a half – more,” Collins said. “But now, because they’re more commonplace and have achieved economies of scale, LEDs are much more competitively priced, maybe 10 to 20 percent more. I can easily justify paying 10 to 20 percent more for LEDs just for the improved uptime and lack of maintenance.”
The Bottom Line
According to Collins, “We use LEDs wherever they’re available and wherever we can – everything from warning lights to job illumination to scene lights to interior lights at nighttime when our folks are filling out their paperwork. Wherever we can use an LED, we do it.”