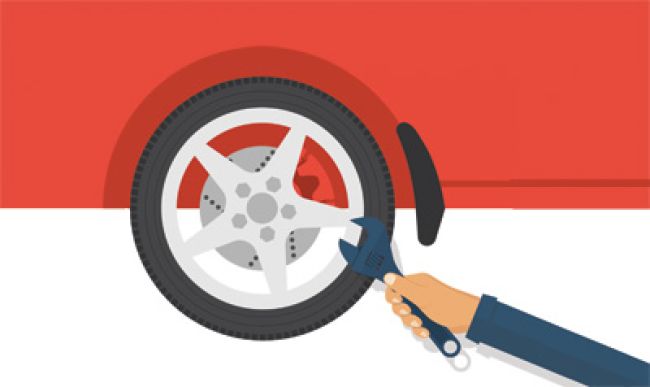
Invest in the Right Training for Your Fleet Technicians
Matt Gilliland, director of operations support for Nebraska Public Power District (NPPD), understands the value of investing in training for fleet mechanics.
“There is an old cliché that says, ‘The only thing more expensive than training is not training,’” he said. “Training is one of the most important tools in the technician’s toolbox.”
And it’s even more so these days in an industry that, according to Gilliland, “changes rapidly, and the technology within the industry grows ever more complex. Training is paramount for success.”
To stay on top of changes with OEM specs, NPPD sends its fleet team to training on an ongoing basis. That, said George Survant, senior director of fleet relations for NTEA – The Association for the Work Truck Industry (www.ntea.com), is necessary today.
“The most challenging change we see in new-model equipment is the rapid and pervasive introduction of electronic control systems and subcomponents,” Survant said. “An issue that can make these systems challenging is they may impact several different elements of the vehicle when in use.”
But it isn’t really just one issue, Survant noted – and he should know. Before joining NTEA in 2017, Survant worked in fleet at Florida Power & Light, Charter Communications and Time Warner Cable. “The volume of change can be overwhelming. The … use of electronic controls and the integration of electronically controlled subsystems replacing traditionally mechanically driven devices is increasing, and several changes often occur with a new-model release,” he said.
Charlie Guthro, vice president of global strategic services for fleet management services provider ARI (www.arifleet.com), said the challenges are greater for utilities. “Manufacturers of the upfit equipment – such as booms, cranes, material-handling devices, etc. – continue to evolve and automate, complicating the repair and service of these units for technicians. If you take into consideration the chassis as well, there’s more and more equipment each year (more cameras, sensors, technology, etc.), and they all have to be diagnosed and fixed.”
Guthro noted that utilities have the added complexities of attachments and the integration of those attachments to chassis.
Training Tips
Training and other efforts can help utility fleet technicians stay on top of changes. In particular, Survant and Guthro offered the following guidance.
Make training a priority. In his roles as a fleet professional, Survant made training part of the requirements for internal promotions. He also made sure to recognize team members who demonstrated “how they value technical skills development through participation in the training and mastery of their new skills.”
Take advantage of OEM resources. “If a fleet is (and utilities often are) an established warranty center for its selected OEMs, keeping that relationship typically requires mechanics to have a predetermined number of annual training hours,” Survant said. “This gives the fleet access to the same type of training dealers usually have, which allows them to stay current with factory training.” Fleets that aren’t warranty centers may need to look to vendors that sell diagnostic equipment, which requires annual OEM updates.
Develop internal training programs. Guthro noted a lack of third-party vendors who “offer a viable option for outsourcing repairs. Operator safety is a critical aspect of utility fleet operations, so it is vital that you have highly trained and skilled technicians working on your vehicles. This puts utilities in a unique position of having to train and develop their own in-house talent to support consistent, long-term maintenance solutions.”
Know when to outsource. When Guthro was director of operations for a large utility in Canada, his fleet used a plan that balanced outsourced and in-house services – and incorporated focused training for those in-house specialties. “We committed to getting our technicians the best-in-class training, and that typically included a variety of resources, including support from the various OEMs for both the equipment and the chassis,” he said.
Connect with those who know. Survant pointed to training that NTEA offers during The Work Truck Show and Truck Product Conference, both of which include OEM chassis update sessions. Guthro noted that fleet management companies can help, too.
Make the right initial choices. “During your tender or selection process, be sure to use your leverage and buying power to mandate training for your technicians,” Guthro said. “Additionally, having consistent specifications helps to minimize potentially unnecessary complexities across your fleet.”
About the Author: Sandy Smith is a freelance writer and editor based in Nashville, Tennessee.
*****
A Shortage of Mechanics Heightens Challenges
Changing equipment specs is just one of the challenges that utility fleet professionals face. Today, a shortage of mechanics is complicating matters. Diesel mechanics in particular are in short supply.
George Survant, senior director of fleet relations for NTEA – The Association for the Work Truck Industry, still sees bright spots, however. “It’s equally true that many of the newer entries into the workforce are bringing new skills with them,” he said. “They are often far more comfortable with emerging technology than some seasoned professionals. And as many of them are joining the workforce with recent training skills, those can be leveraged to develop them into well-rounded contributors.”
One of the challenges to overcome, Survant said, is the “all-too-common misconception that these jobs are relatively low-skilled and low-paid with minimal growth opportunities. Rather than this perception being factual, the growth of new technology is changing the landscape where fleet professionals contribute by driving up the value of high-skill team members, creating a well-rounded employee set with opportunities for future promotion.”
Charlie Guthro, vice president of global strategic services for ARI, pointed to the need to retain existing mechanics. “If you lose them, you’ve lost all the value of your initial recruitment efforts and the training you’ve invested in them,” he said. “It’s vital that you view your technicians as a critical part of your business and make retention a top priority.”