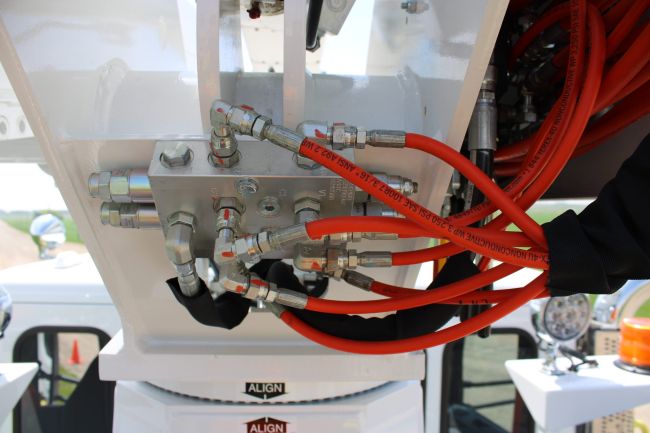
Extending the Life of Hydraulic Hoses
Hydraulic oil, when confined within the hydraulic system and properly maintained, is nonconductive. However, failure of a hose creates numerous hazards that have the potential to harm personnel and damage equipment.
Personnel may suffer burns from contact with hot oil. If the hydraulic line failure creates a mist of oil, it can easily be ignited by various outside sources, such as electric arcing, sparks and flames. And if the hydraulic reservoir is drained, the equipment will become inoperable. In addition to posing a safety hazard for operators, this could also lead to expensive hydraulic pump repairs.
Another safety concern is that, when a hydraulic line fails, a vacuum may be created in the line that breaches the insulating portion of the boom, causing the aerial device or digger derrick to be conductive at voltages above distribution voltages. This is known as vacuum flashover.
Leaks are also problematic, negatively affecting function pressures. Vigilance is key. Inspections – both daily and at intervals prescribed by the manufacturer – will help fleet personnel keep hydraulic lines in good working order on bucket trucks and digger derricks.
When checking for leaks, always wear safety glasses and gloves. Never use your hands to check; instead, use a long piece of cardboard or wood to look for the leak. If fluid is accidentally injected into your body, it is important to act quickly. Apply a cold pack to the injection site and seek medical assistance immediately, preferably from a doctor familiar with injection hazards and incidents. First responders and emergency room medical personnel will want to know what type of hydraulic fluid was injected and at what pressure.
Common Causes of Hose Failure
Hoses most often fail due to overheating, weather degradation, wear from flexing and use, being improperly assembled or installed, or being operated at the wrong pressure setting.
Insulating aerial lifts and digger derricks use two types of hydraulic hose: orange nonconductive and wire braid. Insulating hose will be used for tools, at the boom tip and through the insulating sections of the boom. Wire braid hose will be used at the turntable and below rotation.
The temperature limit of the hydraulic oil is determined by the manufacturer’s limits of the orange nonconductive hose. The jacket on the hose will start to soften at 180 degrees Fahrenheit. At temperatures above 180 degrees, the orange hose will begin to turn brown. For this reason, do not exceed the maximum operating temperature stated by the equipment manufacturer. It is important to routinely monitor the oil temperature gauge, if equipped, especially when working in ambient temperatures over 100 degrees. If it is suspected that the hydraulic oil is getting too hot, stop operations when it is safe to do so and allow the oil to cool. The best defenses to prevent overheating the oil are to operate intermittently; verify the machine has the correct hydraulic oil for the temperature range; make sure the hydraulic system is functioning properly; and add oil coolers.
Users should also know that orange nonconductive hose is more susceptible to UV light, exposing the fiber braid inside the hose. Once the braid is exposed, the orange hose is no longer considered nonconductive because the braid can wick water. This presents additional safety concerns for the dielectric qualities of the insulating aerial device or digger derrick. Although wire braid hose is tougher against UV light, it will eventually harden and crack. Once it does start to degrade, it can rust, becoming less flexible. Cracks will affect its ability to retain proper pressure.
All exposed areas – especially at the elbow and boom tip – should be inspected each day for UV degradation. It’s a good idea to use a nylon hose covering at all exposed areas to provide an additional layer of protection from UV degradation. The hoses under the deck to the outriggers and controls may be damaged from road debris or snagging on obstacles if traveling off-road; they should also be inspected daily. Hoses on the inside of the boom can be affected as well. These should be inspected annually.
Cuts, nicks, gouges and abrasions are all signs of wear. Hoses that exhibit any of these conditions must be evaluated to determine if replacement is necessary, and the cause of the damage must be corrected to maintain the integrity of the hose.
Avoid Assembly Errors
When replacing hoses, there are two issues that can cause damage: hoses that are misaligned to the fittings and hose ends that are improperly crimped.
Hydraulic hoses are usually secured with two fittings that spin in opposite directions. If the hose is not properly aligned with the fittings, its life expectancy is significantly shorter. The two-wrench method is a best practice for avoiding misaligned hoses and fittings. Hold the fitting closest to the hose with one wrench and use the other wrench to loosen or tighten as needed.
In addition, the ends of hoses differ from manufacturer to manufacturer, and they also vary based on whether you are working with orange nonconductive hose or wire braid hose. The crimp die, hose and fittings must be compatible with one another to achieve a properly crimped fitting. Crimp dies may also become worn, causing an incorrect crimp. Under-crimping can cause the end to blow off during operation, and over-crimping can cause damage to the hose, leading to future failure.
If you are doing your own hose replacements, Terex customers can order the correct hose assembly by part number through the online parts portal at www.terex.com/utilities/en/support/parts.
About the Authors: Jim Olson is senior product engineer for Terex Utilities. He has a mechanical engineering background and has been working in design and engineering for aerial devices and digger derricks since 1986.
Craig Ries is a product safety engineer for Terex Utilities. He has a mechanical engineering background and has been working in design and engineering for aerial devices and digger derricks since 2005.
Hydraulic Line Failure? Here’s What to Do.
Regardless of your equipment’s make or model, it’s important to quickly stop oil flow caused by a hydraulic line failure to prevent an environmental hazard, further damage to the unit and injury. The following sequence can be used to stop the flow on an aerial device.
From the Platform
- Release the function being operated. Shut off the tool valve if the tool, tool hoses or tool connections are involved.
- Activate the stop control, which will divert the flow back to the tank.
- Activate the engine stop/start switch, if equipped. This will stop the engine driving the pump.
- Get ground assistance if all these measures fail.
From the Vehicle Bed
- Move the control selector at the lower controls to the lower control position. This will stop all flow to upper controls.
- Push the engine stop/start switch, if equipped. This will stop the engine driving the pump.
From the Ground
- Shut off the pump engine. This will stop the pump.
- Disengage the power takeoff. This will stop the pump.
- Move the control selector at the outrigger control valve to the opposite position it is in. This will stop all flow to the failed function.
- Push the engine stop/start, if equipped. This will stop the engine driving the pump.
- Once the flow is stopped, determine where the line failure is located. Then determine if it is safe to approach the vehicle. Be sure to use appropriate PPE.
- If the line failure is between the upper and lower controls, overriding the upper controls and only operating from the lower controls may reduce the rate of hydraulic oil loss. The intermittent loss of hydraulic oil may allow the aerial device to be lowered.
- It may be necessary to use another aerial device to bring down the occupants.
- Contact qualified personnel to stow the unit for repair.
EUFMC 2024, held in June in Williamsburg, Virginia, was attended by a record 175 fleet representatives from electric utilities, contractors, co-ops and municipal operations, including over 50 new members and eight new companies. Joining the fleet professionals at the industry’s premier annual event were more than 360 attendees from almost 100 manufacturers and suppliers that offer vehicles, equipment, products and services for utility fleet operations. … Motiv, a leading OEM of medium-duty electric trucks, has announced the appointment of Scott Griffith as its new CEO and board member. Griffith has spent the past 30 years founding, leading, scaling and advising technology-based companies that have often been market disrupters operating at the intersection of technology and mobility. Immediately prior to joining Motiv, Griffith served as CEO of Ford Motor Co.’s autonomous vehicles and mobility businesses. … The Shyft Group Inc. – a North American leader in specialty vehicle manufacturing, assembly and upfit for the commercial, retail and service specialty vehicle markets – has signed an agreement with Amerit Fleet Solutions to provide 24/7 maintenance and support services for Blue Arc EV trucks across the U.S. Blue Arc EVs will soon be available through a select network of dealerships, each staffed by technicians trained and certified by Shyft’s Blue Arc engineering team, ensuring customers can conveniently service their vehicles at dealership garages.
Images courtesy of Terex
- APWA’s Public Works Expo Returns to Atlanta
- The Long and Winding – Yet ‘Inevitable’ – Road to Electrification
- Cybersecurity Best Practices for Utility Fleets
- EPA Tightens the Screws on Harmful Vehicle Emissions
- The Latest Developments in Trailer Telematics
- Extending the Life of Hydraulic Hoses
- What’s New in Utility Construction Equipment in 2024?
- 6 Factors to Consider When Developing or Updating Your Fleet’s Idling Policy
- Don’t Abuse OSHA’s Digger Derrick Exemption
- If You Missed the 71st EUFMC, Here Are the Highlights