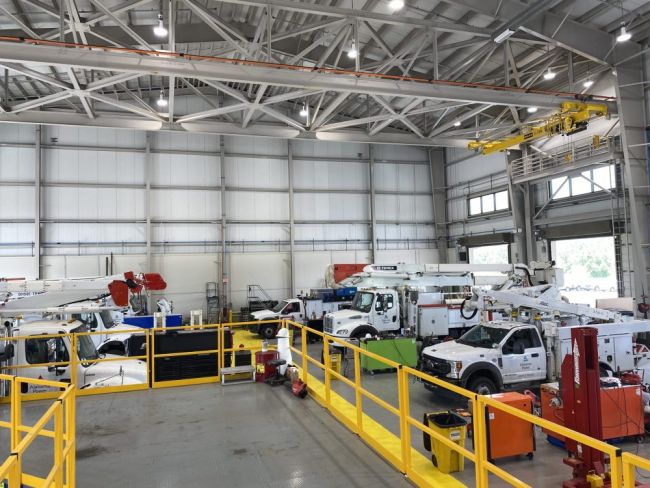
Crafting an Effective Shop Safety Policy
Creating and maintaining a comprehensive shop safety policy is essential for any utility fleet.
Both James Kuha, transportation operations supervisor at Central Hudson Gas & Electric (CenHud), and Brian Johnson, fleet engineering and technical services manager at Alabama Power Co., emphasize the importance of a robust safety framework that prioritizes employee well-being and operational efficiency.
Policy Components
According to Kuha, there are four critical elements that every safety policy should include.
1. Personal protective equipment protocol: Ensuring that employees have access to and properly use necessary protective gear is fundamental to minimizing workplace injuries. “If proper PPE is not available, employees should stop and locate what’s needed,” he advised.
Johnson added that a “safe technician starts with a safe work environment, including the tools and equipment available to them.”
The diversity of fleet equipment – from golf carts to 150-foot aerial lifts – necessitates access to the right tools and training. To aid in this, Alabama Power developed a PPE matrix that guides technicians on the safety equipment required for specific tasks, ensuring they know what protective gear is necessary for their work.
2. Safety procedures: Clearly defined procedures that outline how to safely perform tasks should be established and effectively communicated to all employees.
Often, fleet technicians find themselves in awkward physical positions, such as working under vehicles on lifts or swinging sledgehammers. Kuha noted that “heavy lifting, overhead awareness and proper body mechanics” are critical considerations when developing safety procedures.
3. Housekeeping: Maintaining a clean and organized work environment reduces hazards and promotes safety.
4. Risk assessments: Ongoing evaluations of potential risks associated with tasks can help identify and mitigate dangers before they can result in incidents.
Johnson emphasized the significance of identifying critical risks present in the work to be performed. “A critical risk is one that exists when performing a job task with high potential for serious injury or death due to a specific hazard,” he said.
Alabama Power focuses on three main critical risk areas:
- Falls from height: Employees must maintain three points of contact when working at height. If that’s not possible, fall protection measures must be implemented.
- Working on and around mobile equipment: Crucial to safety is the proper setup of equipment, using tools like wheel chocks and support stands while following lockout/tagout procedures.
- Driving: “It is expected that we will always fasten seat belts and store distracting devices in a safe place,” Johnson said.
Effective Communication and Enforcement
For a safety policy to be effective, it must be clearly communicated and consistently enforced.
“Patrol your areas and speak directly to employees,” Kuha advised. Regular morning meetings encourage open discussions about safety issues. Additionally, quarterly safety meetings allow for a deeper analysis of incidents, enabling collective learning from mistakes.
Johnson emphasized the role of leadership in setting the safety tone: “It is important for fleet managers to be present and set a good example. Show by example that safety rules are expectations, not suggestions.”
Regular safety training is crucial to keeping safety policies top of mind. Kuha advocates for promoting a strong health and safety culture by providing continual training and encouraging employee engagement. Regular discussions to identify hazards and determine mitigation strategies foster a proactive approach to safety.
Johnson’s team holds daily tailgate discussions and monthly safety meetings, providing ample opportunities for ongoing dialogue around relevant safety topics. He noted that “at the start of each year, we hold a safety kickoff meeting to discuss focus areas and set the tone for the year.” This proactive approach helps to maintain a strong safety culture throughout the organization.
Policy Reviews and Updates
Safety policies must be regularly reviewed and updated. Kuha recommended using risk assessments and incident analyses to evaluate existing policies. “Looking at each incident and analyzing them carefully can help prevent similar incidents,” he said.
Kuha also suggested that policies be reviewed no less than once per year as well as whenever new hazards are introduced into the shop environment.
Johnson added that involving frontline employees in the development and review of safety policies is essential for gaining buy-in and ensuring that the policies are practical and relevant.
“No one knows what happens on the shop floor more than the technician who experiences it daily,” he said. “Empowering our employees to help identify risks and review our safety policies produces an understanding of the importance of and ownership in the safety program.”
About the Author: Grace Suizo has been covering the automotive fleet industry since 2007. She spent six years as an editor for five fleet publications and has written more than 100 articles geared toward both commercial and public sector fleets.
Photo courtesy of Alabama Power Co.
- Unlock the Power of Effective Communication: 3 Must-Read Books for Fleet Managers
- Ambitious Vehicle-to-Everything Technology Deployment Plan Likely to Hit Roadblocks
- Crafting an Effective Shop Safety Policy
- When EVs Run Dry: Is Mobile Emergency Charging the Answer?
- Dielectric Testing for Insulating Aerial Devices
- Spec’ing Bucket Trucks to Improve Roadside Safety
- The State of Fleet Electrification: Plug-In Hybrids vs. All-Electric
- Best Practices for Developing a Safe Driving Program
- ATSSA to Debut New Show Format at Upcoming Annual Convention