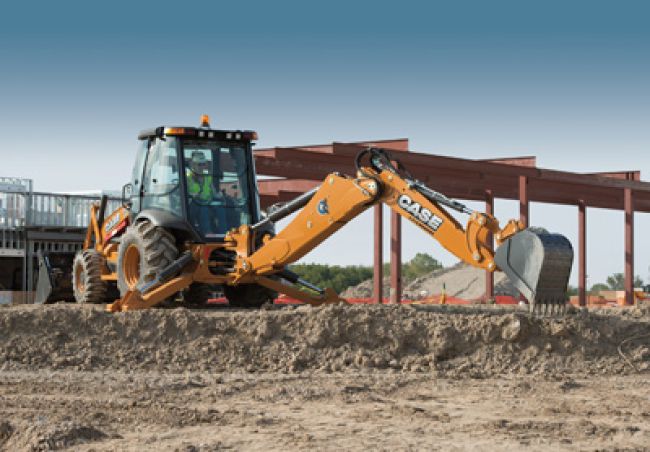
3-Point Checklist for Spec’ing the Right Backhoe
A backhoe is not likely to be the asset most often purchased for a utility company’s fleet. For example, Duke Energy – which has more than 15,000 fleet assets – “may only purchase three or four a year,” said Chris Jolly, Duke’s director of regional operations for Carolinas West.
That means a purchaser may not be as familiar with the required specs for a backhoe as he or she may be with, say, the specs for a standard pickup truck used by the utility.
But it is just as important to get the specs right, said Eric Zieser, NAFTA product manager for backhoes at CASE Construction Equipment. “Buyers really do need to understand their entire fleet and how a backhoe plays into it. By under-specifying a machine, you may actually be creating more work and cost for yourself in the future by having to bring in/rent/transport additional equipment to do the job.”
So, when spec’ing the next backhoe for your fleet, keep these three points in mind.
1. Know what you need.
At Duke Energy, an acquisition team works closely with crews in the field, despite having a corporate agreement with one manufacturer for a standard backhoe, according to Jolly. Even with that standard equipment, there are options.
“Listen to your customers and work closely with the manufacturer. They’ve got the history of what the product can do,” Jolly said.
And skip the idea that a bigger engine or greater dig depth is always the answer. Zieser points out that large backhoes provide greater digging depth and power, but their size may limit their access to worksites. In addition, wide tracks may provide more stability yet may be more difficult to transport. “That’s why it’s so important for backhoe buyers to understand their application – and how that backhoe fits into the overall flow of their fleet,” Zieser said.
2. Consider more than price.
While price is certainly an important consideration, utility also must be factored into the equation when spec’ing a backhoe. “Not understanding how that backhoe will be utilized and optimizing the asset to its greatest potential can be even more costly,” Zieser said.
He points to the option of auxiliary hydraulics as an example. “By not adding greater auxiliary hydraulic options to a backhoe, will you now have to bring in other machines to operate certain attachments and perform certain tasks?”
Even with the standard backhoe configuration, Duke Energy permits an integrated tool package to be added, which allows the bucket to be changed out for forks. “It makes the unit a little more versatile,” Jolly said.
Warranty, preventive maintenance and ongoing upkeep also must be considered during the spec’ing process, Zieser said. “Each manufacturer has its own warranty and conditions. It’s important to understand that, and to understand how the local dealer representative works with you to carry out the terms of that warranty.”
In terms of maintenance, Zieser points to CASE’s SiteWatch telematics, which monitors equipment performance and tracks engine hours to ensure maintenance is done on time.
3. Enhance safety features and operator comfort.
Clearly, utility fleet managers have a number of items to consider when spec’ing backhoes, and operator comfort is one that cannot be forgotten. At Duke, Jolly said that could include allowing some modifications based on operator desires. Florida backhoe operators may want an open cab with a fan while those in the Midwest may prefer a closed cab.
Safety also is important, and Duke is always on the lookout for new enhancements. Jolly said manufacturers are open to input about safety features that utility fleets would like to see, such as the inclusion of ladders on the side of bulldozers, which is something Duke discussed with Caterpillar. “Now we can spec and order that,” Jolly said.
Ultimately, an important key to a strong backhoe spec may be reaching out to other utility fleet professionals, Jolly said. “Don’t hesitate to call on other utilities to ask what our experience has been and how things are working for us. We’re open to share that type of information to help others out.”
About the Author: Sandy Smith is a freelance writer and editor based in Nashville, Tenn.
*****
Key Questions to Ask
Eric Zieser, NAFTA product manager for backhoes for CASE Construction Equipment, suggests that fleet managers ask the following questions in order to select the best backhoe for their operation.
1. How will the backhoe be transported? Your current trailer may determine the backhoe size – or bring the added costs of buying a new trailer.
2. What is the anticipated digging depth? Zieser recommends going beyond your average operating conditions to ensure you can tackle typical jobs that come your way.
3. What types of auxiliary hydraulics are needed? “If you are running multiple attachments, a combination hydraulics setup is ideal, as owners can then switch back and forth between unidirectional and bidirectional, as needed,” Zieser said.