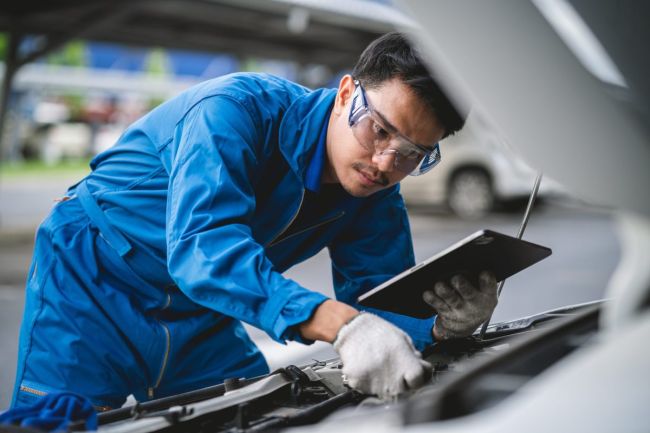
Keeping Your Best: Effective Strategies for Retaining Top Fleet Technicians
With the industry’s ongoing shortage of qualified vehicle technicians, fleet managers need effective strategies to keep their top performers.
Compensation is meaningful, but communication is the real key to retaining technicians, said Paul Jefferson, senior fleet manager for Oklahoma Gas & Electric (OG&E), an investor-owned utility based in Oklahoma City.
The results of an OG&E employee survey found that technicians didn’t like working second shift and that it was a factor in deciding whether they would continue working there. Management listened to those concerns and altered the company’s work hours across 10 service locations.
Instead of running two shifts covering 7 a.m. to midnight, technicians now work until 7 p.m. at the latest. Shifts run nine hours Monday through Thursday, and technicians work an eight-hour shift every other Friday.
“They get off early every other Friday, and we did that to make the hours more appealing,” Jefferson said.
Now, more services are scheduled during the day – rather than drivers dropping off vehicles at the end of the day shift for them to be serviced in the evening. The fleet also added a few spare vehicles to supplement vehicles that are now serviced during the day shift.
Mobile technicians who support new utility construction work four 10-hour days to match the construction crews. Trucks can be serviced on Fridays when the drivers are off.
OG&E crews did get a bit of a pay bump during COVID. During the pandemic, interest rates rose, and a number of technicians took advantage of the increase in their pension plans and decided to retire. About 90% of the technicians eligible to retire made the move, Jefferson said. A salary increase helped retain experienced workers not yet at retirement age.
Jefferson explained that OG&E’s shops have three employment levels: interns, technicians and senior technicians. Most technicians are hired as full journeymen with ASE certifications, but occasionally someone is brought on as an apprentice.
Once technicians come on board, they tend to make a career with OG&E. A few have transferred to other departments within the utility, but other than that, there has been little turnover recently.
When an opening does come up, Jefferson has seen the pool of applicants drop significantly.
“We used to get 50 applications, and now we get 10,” he said.
To stay competitive with commercial repair shops in the region, OG&E has launched a program to add air conditioning to the service facilities.
Jefferson also points out to applicants that the OG&E bays have lifts for medium- and heavy-duty trucks, unlike most commercial shops in the area.
“They can see they won’t be working on a creeper all the time,” he said.
Ameren Illinois
Of course, compensation is probably one of the top reasons technicians choose to stay or go. But there can be more to job satisfaction than money.
At Ameren Illinois, Dan Remmert, senior manager of fleet services, led a compensation review for the more than 50 technicians who work at about 20 locations.
“We discovered the private sector immediately reacted to adjusting technician wages and benefits,” Remmert said. “We’re figuring out how to stay competitive so that we are hiring the best talent.”
As noted earlier, second shift work also drives technicians to look for better hours. Ameren Illinois experimented with creative shift options to give employees the time off they want without impacting operations.
The utility’s shops have two classifications: a journeyman role and a lead/foreman role. They typically hire experienced technicians who are past the apprenticeship phase.
Technicians can pursue career paths within the service group and other departments, such as design and build, quality assurance and frontline supervisors, and the line and substation groups.
“There are many career paths beyond technician that our techs can pursue, but not all of them do it,” Remmert said. “Some people like being a tech.”
Remmert started his 30-year career as a technician, so he knows money isn’t the only motivator.
“Technicians have a great sense of pride in what they do, so we build a team based on the sense that they’re adding value,” he said. “We work hard at making them a part of the solution.”
About the Author: Gary L. Wollenhaupt is a Colorado Springs-based freelance writer who covers the transportation, energy and technology sectors for a variety of publications and companies.
- The State of Self-Driving Trucks
- How Will AI Impact Your Fleet Operations?
- Keeping Your Best: Effective Strategies for Retaining Top Fleet Technicians
- SEMA Predicts Biggest Show in Five Years
- 8 ChatGPT Prompts to Boost Productivity, Improve Your Effectiveness
- The Future of Telematics: Top Trends to Watch
- Maximizing ATUV Uptime: Essential Maintenance Practices for Utility Fleets
- Best Practices for Developing an In-House Maintenance Policy for EVs