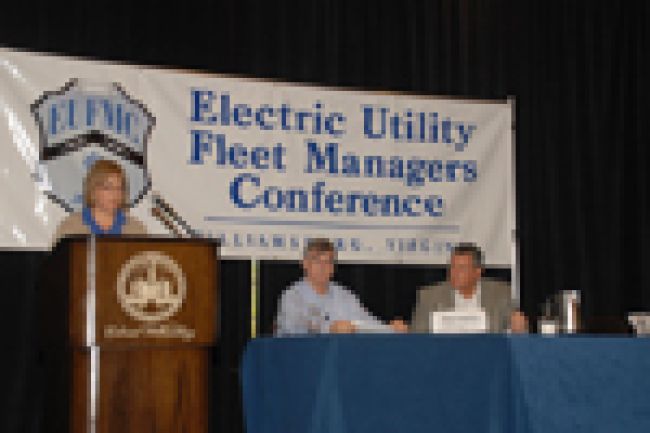
Progress Report
Successfully implementing new technology into fleet operations is a major challenge for managers. In the past few years, perhaps no greater challenge has been faced than the adoption of 2010 emissions-compliant diesel engines. During the 2011 Electric Utility Fleet Managers Conference (www.eufmc.com), two fleets detailed their programs and the performance of these engines in their operations.
Since the most recent diesel engine emissions standards took effect at the beginning of 2010, trucks equipped with selective catalytic reduction (SCR) engines have been fitted with diesel exhaust fluid (DEF) tanks. DEF is a necessary component of emissions compliance using SCR technology.
Georgia Power Company
A subsidiary of Southern Company, Georgia Power Company (GPC) is an investor-owned utility serving 2.3 million customers in the state of Georgia. Its fleet includes 4,500 units, half of which are vehicles. Steven Hopkins, manager, fleet technical services, oversees engineering, maintenance, testing, procurement and financial issues for the fleet, and serves as the team leader for Southern Company’s fleet engineering team.
“By 2011,” Hopkins said, “about 10 percent of our total diesel fleet of 1,128 units had 2010 and newer engines. That included 96 Cummins-powered Freightliners and 17 Fords. By 2015 we project that half of the diesel fleet, or about 573 vehicles, will have engines that require DEF.”
Diesel-powered trucks at GPC typically travel 12,000 miles and run on-site for 1,200 hours per year. Average per day idle time for these vehicles is six hours.
To meet its DEF needs, Hopkins reported, GPC awarded a contract to Brenntag North America, the manufacturer and distributor of TerraCair Ultrapure DEF. Brenntag, an OEM supplier for GM, Ford, Chrysler, Freightliner, VW and BMW, offers its product in 2.5-gallon containers, 55-gallon drums and 330-gallon bulk totes.
“For the next couple of years we’re providing DEF in 2.5-gallon containers at our fleet service centers,” Hopkins related. “We will also be installing heated cabinets at fuel islands in higher usage locations to make it more easily available. DEF tanks are usually filled every three or four weeks, or after approximately 1,000 miles and 100 hours of idling.
”As usage increases we plan to upgrade to 55-gallon drums or 330-gallon totes,” Hopkins continued. “Replenish intervals will be a moving target as more emissions-compliant units are added to the fleet and are something our fleet parts department will be monitoring.”
DEF handling concerns at GPC follow Southern Company safety and health rules. Dispensing always takes place in well-ventilated areas. All employees are already required to wear safety glasses in the work environment, which includes the fuel island, and when adding DEF, the use of impervious gloves such as nitrile, Viton or butyl for DEF handling is recommended. Hopkins also pointed out that the 2.5-gallon DEF containers are equipped with a tubular spout that inserts into the filler neck of the DEF tank to minimize the possibility of splashes and spills during the filling process.
“We have not had any maintenance issues with the 2010 engines and no drivability concerns have been reported,” Hopkins said. “The use of DEF has not presented any issues for our vehicle operators, except for adding the product as needed. It’s just another thing to be responsible for monitoring.”
AmeriGas Propane
A supplier of services to more than 1.3 million customers in nearly 50 states, AmeriGas Propane provides home and commercial deliveries of bulk fuel and cylinders. In the company’s fleet operation are more than 7,900 units, including 5,158 vehicles. By the end of 2012 there will be almost 700 AmeriGas units with newer emissions-compliant engines, including 190 vehicles purchased in 2010, 352 added in 2011 and 388 projected in 2012.
AmeriGas is moving ahead to transition its fleet, noted Jay Massey, corporate fleet manager, in part because the rules changed in California. “We needed to replace 32 trucks in California by the first of this year and will need to replace 138 trucks by 2013,” he said. “Our plan is to move 2007 and newer units into California throughout the year, in addition to sending new trucks.
“That needs to happen soon,” Massey added. “As the order cycle continues to get elongated with OEMs and with builders, it’s urgent we place orders as early in April as possible to meet a fall build schedule.”
For its 2010 and newer models, Massey related several upfit issues that had to be addressed. “We needed clear inside and outside frame rails, and had to determine DEF, air and fuel tank, along with air dryer and battery locations,” he said. “We standardized on a vertical exhaust, but some emissions component routing conflicted with air suspension placement, forcing us back into spring ride on some initial units. We also had a PTO access issue to resolve.”
Driver training was also on the fleet’s agenda. Included was helping drivers interpret system alerts and understand how to respond to protect the asset. On the fleet’s 2010 models, the DEF tank was positioned where batteries and air tanks were previously located, and each unit was equipped with a separate DEF fuel gauge.
“We anticipated about 2 percent DEF consumption, or about 1 gallon of DEF for every 50 gallons of fuel,” Massey reported. “Based on the number of units in the fleet, that lets us plan for inventory needs. Initially, we purchased DEF from truck dealers and some retail outlets. Now, virtually all major truck stops and some large fuel providers are carrying DEF. We also have to consider on-site storage based on the number of units at a domicile location consuming DEF and the ability to store it in a climate-controlled environment.”
Massey explained that different vehicles have different size onboard DEF tanks ranging in capacity by OEM and vehicle type. For example, straight chassis units had 6-, 9- or 13-gallon tanks and tractors are equipped with 23 gallons of DEF capacity. All DEF tanks in the fleet are heated plastic models.
“It’s too early to see if one manufacturer or another has a better truck from a maintenance standpoint,” Massey stated. “Routine maintenance on these vehicles has been primarily preventive and, compared to non-DEF units, has been cost and time neutral.”
Potentially offsetting the higher cost of the latest emissions-compliant engines – as much as $6,500 more for trucks and $9,500 more for tractors in 2010 – is the indication of a slightly better half-mile per gallon increase in fuel efficiency and less non-PM maintenance. Analyses have also revealed a cost per mile for 2010 and 2011 models about equal to or less than 2008 and 2009 trucks.
“Performance is still to be determined,” Massey said, “but we have noticed some improvement and we’re getting good indications about throttle response and fewer occurrences of system regenerations based on driver feedback and other reporting.”
DEF and Storage, Dispensing and Testing Technologies
Nontoxic but corrosive to aluminum and carbon steel, DEF must be stored onboard and on-site in tanks made of stainless steel or plastic. In addition, DEF is sensitive to both extreme cold and high ambient temperatures, requiring adequate climate-controlled systems. Available today are the following:
Old World Industries offers BlueDEF for use in on-highway engines in 1- and 2.5-gallon containers, 55-gallon drums, and 275- and 330-gallon totes. The company also provides a variety of dispensing systems and offers the BlueDEF Equipment Program, an installation, service and maintenance network, as well as a DEF Equipment Training Program for service and support technicians. Visit www.bluedef.com for more.
Terra Environmental Technologies (TET) produces DEF that is sold under the TerraCair brand name, including the newly introduced TerraCair Ultrapure DEF, in 1- and 2.5-gallon jugs, 55-gallon drums, 330-gallon totes, 5,000-gallon tankers and 20,000-gallon railcars. TET also offers dispensing equipment installation and training services to DEF users, including fleets with in-house systems. Visit www.tet-terra.com for more.
Colder Products Company is offering its DrumQuik PRO closed-dispensing solution for extracting DEF from drums, small containers and totes. The system is in use by DEF suppliers, including Airgas Specialty Products and Balcrank Corporation, who offer it as a stand-alone component or as part of a package in both fixed and portable pumping systems. Visit www.colder.com/Specialties/DrumQuik/DrumQuikHome.aspx for more.
Gilbarco Veeder-Root offers its Encore S DEF and Encore S DEF + 1 along with the new Atlas DEF dispenser. The products are fully compatible with the company’s Gasboy dispensers and other existing fuel management systems. The DEF dispensers are installed in a thermostat-controlled, heated cabinet that prevents DEF from freezing or crystallizing. Visit www.gilbarco.com for more.
Powerblanket wraparound DEF heaters are available for totes, pumps and dispensing units. Utilizing the company’s GreenHeat Technology, the heated enclosures can be used on metal and plastic containers. Standard models are available for 275- and 330-gallon tote sizes, and custom sizes are offered. The heaters can provide several hours of protection in the event of a power failure. Visit www.powerblanket.com for more.
Reichert Technologies DEF-Chek testers for measuring the correct concentration of DEF can be used to perform quality control checks on bulk supplies and vehicles. The tester accurately measures DEF for the right urea content, providing a digital measurement in seconds. The Reichert Digital DEF-Chek tester is powered by two AAA batteries. Visit www.reichertai.com/automotive.html for more.