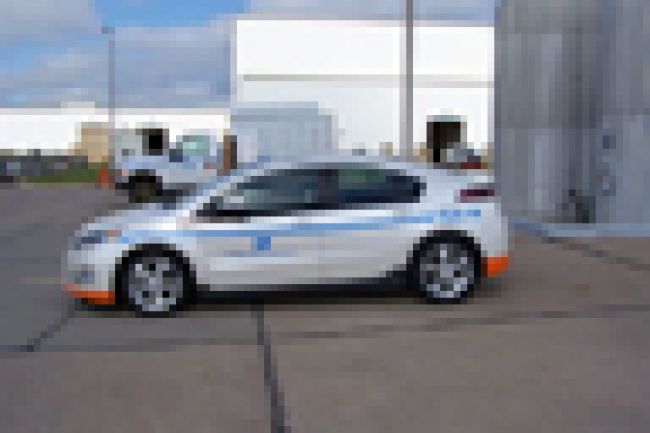
HTUF Report
HTUF REPORT
Held in mid-September in Charlotte, N.C., the 11th Annual High-Efficiency Truck Users Forum served again as an educational and networking event for manufacturers, suppliers, fleets and government officials interested in learning the latest about high-efficiency truck technology.
HTUF has been very successful in helping launch the first production of hybrid trucks and is credited with reducing product development time by up to two years. When the conference was first held, no major truck manufacturer was offering electric or hybrid trucks. Today, there are more than 30 different electric, hybrid electric, hydraulic hybrid and workplace hybrid trucks available.
At this year’s conference, three federal government and private industry representatives took center stage. Heather Zichal, deputy assistant to the president for energy and climate change, discussed policy initiatives to create clean energy jobs, tackle climate change and reduce dependence on oil.
Also on the HTUF agenda was Dr. Dane Boysen, program director at the Advanced Research Projects Agency-Energy, who addressed technology research and development initiatives that ARPA-e is funding and how they are accelerating advanced technology market penetration. ARPA-e has made investments in advanced batteries, electric motors and lightweight materials that could enable fleets to dramatically reduce reliance on oil over the next decade. HTUF also featured David Mohler, senior vice president and chief technology officer at Duke Energy, who covered the increasing connections between vehicles, the grid and saving energy.
“We are very pleased to have secured key leading officials from the federal government and industry at HTUF,” said John Boesel, CALSTART president and CEO. “Clean energy jobs and reducing our dependence on oil are core elements of the president’s energy policy, and the Pentagon continues to focus on energy efficiency as a critical component of the nation’s energy security.
“Beyond conventional clean diesel engines, there are now at least five different advanced propulsion systems for commercial and military trucks,” Boesel continued. “At this year’s conference, fleets learned how each of these new drivetrains can be applied and utilized. Never before have there been such opportunities to cost-effectively transition away from dependence on the highly volatile and unstable world oil market.” Visit www.htuf.org.
Odyne Systems Showcases Plug-In Hybrid Systems
Odyne Systems LLC, a manufacturer of hybrid systems for medium- and heavy-duty work trucks, displayed its hybrid propulsion system on a Ford F-750 chassis at HTUF. Odyne plug-in hybrid systems are designed to interface with a wide variety of truck-mounted equipment. Driven through the Allison 3000 RDS transmission, the system uses a Remy electric motor in parallel with the existing drivetrain to provide launch assist and regenerative braking. At the job site, the Johnson Controls’ lithium-ion battery packs power work site applications. Visit www.odyne.com.
Kenworth Delivers with T440 CNG Truck
Kenworth Truck Co. showcased a Kenworth T440 compressed natural gas (CNG) tractor during HTUF. The T440 CNG is equipped with an 8.9-liter Cummins Westport ISL G engine and a six-speed Allison 3000 HS transmission. The model is available as a straight truck or tractor in a gross vehicle weight ranging from a heavy Class 7 vehicle at 33,000 pounds to a light Class 8 at 68,000 pounds. The ISL G engine uses a maintenance-free, three-way catalyst. Rated at 320 HP and 1,000 pounds per feet of torque, the engine’s torque curve closely matches that of its diesel counterparts. Visit www.kenworth.com.
PG&E REPORTS ON ELECTRIFICATION SAVINGS
The Electrification Coalition, a nonpartisan, not-for-profit group of business leaders committed to promoting policies and actions that facilitate the deployment of electric vehicles on a mass scale, has issued the following report on the electrification of the Pacific Gas & Electric fleet.
In 2011, the Pacific Gas & Electric vehicle fleet racked up 114 million miles of travel, many of them logged servicing lines and other equipment that deliver power to customers. As a critical service provider, PG&E must purchase vehicles capable of supporting its mission in low-probability, high-impact situations like severe unplanned power outages. In these scenarios, vehicles must sometimes travel great distances across the company’s service territory and then operate buckets and other repair equipment once on site. In fact, even routine service calls can vary greatly by distance, necessitating flexibility and putting a premium on range and refueling.
Because its vehicles have a low level of route predictability, PG&E is pursuing an acquisition strategy that prioritizes plug-in hybrid electric vehicles (PHEV) and electric work-site idle management systems (EWIMS), which are plug-in vehicles whose batteries provide power for a range of job site functions, but do not move the wheels. PG&E’s fleet of PHEVs is generally spread throughout its passenger cars and pickup trucks. The passenger cars are typically pool vehicles used by employees for work-related travel. These vehicles tend to travel only short distances. The pickup trucks are primarily work trucks, but are also driven by job site supervisors and foremen. PG&E’s EWIMS are Class 6 trucks and are a mix of bucket trucks and material handlers.
In addition to extended range, PG&E’s emerging fleet of PHEV pickup trucks provides the company with an additional strategic benefit. A typical PHEV relies largely on its onboard battery for power over a given mileage range. When the battery is depleted to specific level, the vehicle then relies on an onboard gasoline-powered generator to provide power to the battery, operating essentially as a gasoline-electric hybrid. PG&E has recently begun deploying a handful of retrofitted PHEV pickup trucks manufactured by companies like Orem, Utah-based VIA Motors. These vehicles currently feature between 15 and 100 kW of exportable power, and there is potential to increase that number. When these vehicles are on a job site, their onboard generator can bypass the battery and export electricity to a different destination like power tools or even a transformer.
Work site management technology is a logical fit for the duty cycle associated with PG&E’s Class 6 bucket trucks. These vehicles, which are typically located at a job site for six to eight hours per day, often consume more diesel fuel idling than driving. This is because work site repair functions – operation of the bucket and associated equipment – normally require the truck to be running, using its engine as a generator. It’s an inefficient use of fuel, but has historically been the only option. Today’s EWIMS technology utilizes an onboard battery to power job site equipment, allowing the engine to be turned off and saving fuel. The battery can be recharged by plugging into the grid or by a secondary onboard alternator that provides electricity to the battery while the vehicle is driving. The savings associated with the technology are substantial: In 2011 alone, PG&E saved more than $700,000 on fuel across its fleet of 178 EWIMS work trucks manufactured by Birmingham, Ala.-based Altec.
Finally, as an electric utility, PG&E arguably has an elevated level of interest in understanding plug-in electric vehicles (PEV) and working to support their commercialization. By the end of 2012, the company will own a total of 400 PEVs, ranking it solidly among the top three U.S. commercial fleets in terms of PEV ownership. Perhaps more interestingly, PG&E’s current fleet of PEVs have been sourced from seven different original equipment manufacturers.
A number of factors were taken into consideration as PG&E explored the possibility of adding PEVs to its fleet. The vehicles carry a great deal of promise due to a number of economic, regulatory and environmental benefits, but there are also a number of important challenges. PG&E offered insight into its decision-making process by ranking various factors and discussing their rationale around each one in detail.
Total Cost of Ownership: A vehicle’s total cost of ownership (TCO) – its upfront capital costs combined with operating costs over a specific number of years or miles traveled – is a standard tool for comparing the economics of various technologies. However, while TCO may provide a useful starting point for comparison in the abstract, a vehicle’s purchase price is a more pressing real-world consideration for many fleet operators, PG&E included. This is particularly the case when it comes to purchasing new technologies like PEVs. Any assessment of TCO will necessarily be based on a series of assumptions about performance, some of which may ultimately be less precise for the first generation of a given technology. This type of uncertainty ultimately increases the level of risk placed on the fleet customer. Utilities like PG&E can be particularly capital constrained, in the sense that budgets are often set several years in advance through regulatory filings. Therefore, the higher capital cost of PEV purchases either has to be justified to the regulator – and ultimately the rate payer – or it has to displace other spending. If a plug-in vehicle carries a cost premium of 25 percent, it means a utility with a fixed budget can only purchase four PEVs for the same cost as five traditional vehicles, leaving one vehicle in need of replacement in the field. This attrition represents an operational risk that no utility would likely take on. Therefore, in evaluating the size and timing of its PEV purchases, PG&E is mostly focused on the impact these acquisitions will have on capital budgets. Whether a fleet manager purchases or leases a vehicle, there is a monthly payment associated with it. For PEVs, this payment is currently higher than the payment for a comparable traditional vehicle. If the net of this capital premium less operational savings (reduced fuel expenditures) results in a higher total monthly outlay, it becomes hard to justify. There is intense competition for capital within PG&E, and the higher payment associated with a PEV purchase is capital that is unavailable to be spent on other projects – or booked as profit.
Access to Competitive Financing: Increasingly, fleet customers are looking to commercial financing entities to help manage the capital cost challenge of PEVs. Of course, financing is not a magic wand that can make something inherently expensive become cheap. So what PG&E is particularly interested in is managing the cost structure of PEV purchases as opposed to managing the actual cost of the vehicles. Actual vehicle costs will decline over time due to some combination of manufacturing scale and technological improvements, but the cost structure – that is, the way customers deal with the price premium on PEVs – could potentially be addressed in the near term. One possible avenue to cost management through competitive financing is an extended term on vehicle useful life. For example, PG&E currently finances its purchases of pickup trucks in line with industry common practice, which typically assumes a six- or seven-year vehicle life. However, publicly available data confirms that the age of the average light-duty truck on the road in the United States has increased every year since 2000 and now stands at more than 10 years. By extending the vehicle useful life assumed in standard financing packages for these trucks by three years, the cost premium would be spread out over a greater term, giving fleet customers more capital flexibility and encouraging more PEV purchases. It’s a challenging proposition for an unproven technology, but it’s one way PG&E is working to manage cost.
Operational Benefits: Another option for managing costs is to make sure you are capturing all the benefits. Generally speaking, in terms of performance, utilities get graded on two things: the number of service outages and the duration of those outages. In measuring the number of outages, there is essentially no discrimination between an outage that affects 10 customers and one that affects 10,000 customers. Moreover, regulators do not discriminate between outages that are unplanned and those that are planned. While unplanned outages arising from weather and other unexpected events account for some of PG&E’s service calls, planned outages to repair lines and upgrade transformers account for a substantial portion of total outages. While VIA Motors’ PHEV pickup trucks currently allow for just 15 kW of exportable power, the company is working to increase that capacity to 50 kW. In larger applications, like a retrofitted Ford F-450 from Electric Vehicles International, PG&E believes it is already possible to get close to 100 kW. Altec’s Class 6 EWIMS truck currently features 3 kW of exportable power. Considering that the power needs of the average home in California today are roughly 5 kilowatts, the possibilities for providing backup power to homes – even whole neighborhoods – during outages could be significant. Put another way, the largest portion of neighborhood transformers in the PG&E service territory are fewer than 100 kW (125 kVA). While reliably exporting this kind of power is still a speculative prospect at this point, PG&E believes it is possible to get there in the near term. If accomplished, it’s a technological milestone that would fundamentally change the utility business, allowing companies like PG&E to virtually eliminate planned outages arising from transformer maintenance and upgrades. In a business built around service reliability, this kind of operational advantage could be a game changer for improving customer relations and strengthening utilities’ standing with regulators.
Vehicle Maintenance Savings: PG&E is realizing real savings on maintenance costs for its fleet of PEVs. Conventional wisdom suggests that the savings on maintenance compared to traditional internal combustion engine (ICE) vehicles will be greatest for battery electric vehicles (EVs). This is because the EV drivetrain has the fewest moving parts relative to internal combustion engine vehicles. PHEVs, which retain the use of an engine and fueling system, still require oil and other fuel changes as well as general engine maintenance. Nonetheless, PG&E reports that spending on these maintenance items for its fleet of Chevy Volt PHEVs is lower than spending on comparable ICE models. PG&E attributes the savings to the relatively high portion of electric miles driven by its Chevy Volts, which have an all-electric range of 30 to 40 miles. Employees’ average trip in San Francisco, where the bulk of PG&E’s Volts are located, is just 11 miles. Two notable categories of maintenance savings being captured by PG&E are reduced spending on brake pads and tires for vehicles in San Francisco. The city’s hilly terrain takes a toll on vehicle brakes, which the company estimates it replaces every six months for traditional ICE vehicles. However, initial experience suggests that the brake pads on PG&E’s fleet of Chevy Volt PHEVs will last as long as two years between replacements under the same conditions due to regenerative braking. By essentially running the vehicle’s electric motor in reverse, regenerative braking slows the Volt as soon as the driver lets off the accelerator, converting this kinetic energy into electricity that helps recharge the battery. During actual braking, the regenerative system augments the conventional braking system, a process that offsets friction that wears on the pads. At the same time, it appears that this process is also reducing wear on tires that occurs normally during harder stopping, leading to less frequent tire replacement.
Electric Vehicle Charging Infrastructure: By focusing on PHEVs and EWIMS work trucks, PG&E’s vehicle electrification strategy fundamentally avoids reliance on public charging infrastructure. However, charging infrastructure located at a vehicle’s overnight parking location is still of high importance for recharging the battery after a typical day’s use. In some cases, PEVs are driven home by employees. But in other cases – such as pool vehicles – a number of units are parked at a central facility. In these cases, PG&E reports that that the cost of installing charging infrastructure can be a significant challenge. In 2011, PG&E installed 35 charging stations for pool vehicles at its downtown San Francisco headquarters. The units were installed in an underground secure parking facility. The hardware cost for individual chargers was extremely manageable at approximately $800 per unit. However, construction costs for running power into the underground facility from the street above are estimated to have been roughly $350,000 – more than 90 percent of the total project cost. PG&E reports that the necessary additional wiring ran only 350 feet, placing the cost at $1,000 per foot. The lesson as always is that cracking concrete for charging infrastructure installation is likely to be expensive in most cases. This is especially true when facilities are being retrofit, particularly in high-cost urban areas. Where companies or government agencies have the opportunity to incorporate charging infrastructure into new construction, costs can be dramatically reduced and better managed.
Sam Ori, director of policy at the Electrification Coalition, recently sat down with Dave Meisel, director of transportation services at PG&E, to get a firsthand understanding of how the company’s electrification strategy is playing out in a real-world project. What follows are highlights from the discussion.
You often talk about the unexpected benefits of PEVs for your broader business. How do EWIMS fit into that?
One of the biggest things that we have seen with our EWIMS is the noise reduction. On our traditional bucket trucks, everything is PTO-driven. A mechanical shaft from the engine runs a pump and that’s what moves the bucket. So to operate the bucket, you have to have the truck running, and it makes a lot of noise. But in residential areas of San Francisco, there are noise restrictions in place that essentially make it impossible for us to do routine work using conventional trucks between 7 p.m. and 7 a.m. That’s no longer an issue with an electric bucket because it’s silent. The engine is off. It’s expanded the workday by 100 percent – from 12 hours to 24 hours. In the past, if a PG&E crew was doing new construction and it got to be 7 p.m., they had to stop. It didn’t matter if there were just two hours of work to go. They had to stop, take the whole site down – which could take about an hour – go home for the night and then come back again in the morning. At that point, they had set everything back up again – which takes another hour – do two hours of work and then take it down again. With an EWIMS bucket truck, they can just work the additional two hours on the first day and be done, avoiding unnecessary time spent getting to and from the job as well as costly setup and takedown hours. The customer is happier and we’re more efficient.
How have the drivers reacted?
I’ll go back to the noise. In the utility business, you often work in pairs. One crew member is up in the bucket and the other is at the ground level. With a traditional bucket, the crew has to communicate over the noise of a running vehicle, which can really be a challenge. But in the case of an EWIMS truck, the engine is off and it’s quiet, so communication is much, much easier. Drivers absolutely love that. I would also add that, especially in our business, an enhanced level of communication actually puts our employees in a much safer situation. When a crew member in the bucket is talking to his colleague on the ground, he is trying to get a handle on critical information that has a material impact on job safety. Making it easier to communicate and have a higher level of confidence in information has been a huge hit with our employees. That enhanced feeling of safety is something that happens every time you go to work. Without question there are other benefits. The work crews certainly appreciate not having to be around the tailpipe emissions of a traditional diesel vehicle idling on a job site over a period of several hours. And the abatement of those emissions is also good for urban air quality. That’s a significant plus for us as a corporation.
The EWIMS technology is really a perfectly customized solution. How did you get there?
The drivers of these vehicles are some of our most highly skilled personnel. They are generally our first responders. What that means operationally is that they do a lot of tickets in a single day – lots of shorter stops to deal with pressing issues. They are at an individual site for an average of maybe two hours. They make a fix and move on to the next job. We wanted a system that would work off the battery and be capable of plugging in to the grid, but that couldn’t be the only way the battery recharged. So we developed the secondary alternator that recharges the battery as the vehicle moves from job to job. We also made sure that the battery was big enough to cover all of the work that would be done in a normal day without running the vehicle at any job site. To get there I would say we worked hand in hand with Altec. They have about 70 percent of the U.S. market for bucket trucks, so they understand our business and have a commitment to customer solutions. Our vehicle design and engineering team at PG&E had an idea for an electric bucket system that we felt would save us money and provide a whole range of operational efficiencies. We sketched out our idea in principle, took it to Altec and six months later the first vehicle rolled off the production line. It has worked out really well.
People often talk about the economics of these technologies in broad generalities. What can you say about your experience?
I can tell you that we are getting about a two-and-a-half-year payback on our Class 6 EWIMS trucks. We make business decisions to make money, plain and simple. So we wouldn’t be doing this if it didn’t work for the company. To me, it all goes back to lining up the right technology with the right application. People think electrification has to be about the propulsion system only. But that isn’t where we are using the most fuel in this particular application. Electrify where it makes sense to electrify. The fleet industry uses PTO shafts in a variety of applications, by the way: dump trucks, refrigerated trucks and more. They’re all shaft-driven, and today they all use a diesel engine to power that shaft. That function could be powered by a battery in all these applications.
I know you spend a lot of time thinking about ways to be creative in terms of integrating these technologies into your business model. What have you learned from your EWIMS deployment?
When we first started looking at these vehicles, we were thinking about them in terms of payback period. So we did a standard analysis comparing current technology costs and fuel consumption to the cost of the new technology and projected fuel savings. But what we have learned is that the operating savings, improved relationship with our customers, the extended work day and the safety improvements dwarf the fuel savings. What we also learned is that, frankly, there is a lot that we as an industry can’t measure when evaluating these technologies with a standard approach to ROI or payback period. So PG&E treats each application as a unique situation and evaluates it individually. Let me also say that the economic impact of these vehicles extends beyond just PG&E. We just had the ribbon-cutting ceremony for a new facility here in Dixon, Calif., where Altec will be expanding its production capacity for these and other advanced vehicles. That’s 150 direct manufacturing jobs in the United States. And when you think about the multiplier for manufacturing jobs, which I think is about five times or six times, you are looking at almost 1,000 new jobs for the local community. That has an impact. Visit www.electrificationcoalition.org.
HYBRID VS. CONVENTIONAL
“There has been no significant change in light-duty vehicles as a percentage of utility fleets,” said Tom Nimmo, a partner with the industry benchmarking firm Utilimarc. “However, we have seen changes within certain light-duty vehicle classes, including an increase in hybrids as a percentage of the fleet. Hybrid data also shows improved mpg and improved operating costs.”
Speaking at the 2012 Electric Utility Fleet Managers Conference (www.eufmc.com), Nimmo covered trends, using 2009, 2010 and 2011 data, at a select group of 41 utilities that field approximately 90,000 utility-specific vehicles. In 2012, the entire Utilimarc database, comprised of state, county, city, utility and private fleets, will track more than 300,000 vehicles. Visit www.utilimarc.com.
RALEIGH POLICE DEPARTMENT SEES SIGNIFICANT FUEL SAVINGS FROM MOBILE POWER IDLE REDUCTION SYSTEMS
Earlier this year, the Raleigh (N.C.) Police Department installed mobile power idle reduction systems in 29 police vehicles. The project was funded by an Energy Efficiency and Conservation Block Grant. Since being installed, the systems have saved Raleigh more than 3,000 gallons of fuel, cut emissions of 59,326 pounds of CO2 and reduced engine use by 107,032 miles. The police department now projects an annual fuel savings from the systems of $63,000.
The Energy Xtreme mobile power idle reduction system is a smart power management device that provides power, without engine engagement, to vehicles with demanding electrical needs. In Raleigh, the system allows police cruiser electrical systems, including lights, onboard cameras, computers and radios, to operate without having to idle the vehicle’s engine for at least four continuous hours. The system automatically recharges while the vehicle is being driven. Visit www.energyxtreme.net.
HYBRID NEWS
Eaton Supports California Hybrid Incentives
The California Hybrid and Zero-Emission Truck and Bus Voucher Incentive Project (HVIP) is getting a boost from Eaton Corporation (www.eaton.com/roadranger). Designed to assist California-based fleets with the purchase of low-emission, fuel-efficient medium- and heavy-duty hybrid vehicles, HVIP aims to help speed the introduction of hybrid trucks with financial incentives ranging from $10,000 to $45,000 for eligible vehicles.
“The Hybrid Truck and Bus Voucher Incentive Project offsets about half of the incremental cost of eligible hybrid vehicles,” said Gerard Devito, engineering director, Eaton hybrid power systems. “The program strongly benefits the public and commercial truck industry by helping interested fleets save money while delivering more sustainable transportation. We applaud the state of California for its pioneering work and many investments to promote and support the use of hybrid vehicles and other clean technology vehicles.”
About 87 truck and bus chassis configurations from a variety of vehicle manufacturers that are equipped with Eaton hybrid systems are eligible for the incentives. Under HVIP, incentives are preset for each qualified vehicle. Eaton hybrid power systems have collectively accumulated more than 300 million miles of service. More than 6,000 of Eaton’s hybrid systems are in use today on trucks and buses. Visit www.californiahvip.com.
ALTE LAUNCHES ELECTRIC VEHICLE FLEET PURCHASING SYSTEM
A Commitment to Action as part of the Clinton Global Initiative America designed to spur adoption of hybrid electric technology in fleets has been announced by ALTe Powertrain Technologies. The developer of a range-extended plug-in electric hybrid powertrain for light commercial fleet vehicles has pledged to develop a first-of-its-kind electric vehicle fleet purchasing system, under which fleet customers can consolidate the entire electric vehicle decision-making process in one web-based interface.
The new website, www.electrifyyourfleet.com, will connect corporate and government vehicle purchasers with electric vehicle stakeholders, including utilities, charging station providers and finance companies, and notify customers of available incentives while offering the benefits of group-rate purchases and simplifying the order-to-delivery process.
“Our commitment to the CGI community is to help solve the greatest roadblocks to commercial adoption of electric and plug-in hybrid vehicles: eliminating the lack of affordability and simplifying the EV and charging station order fulfillment process,” said ALTe chief executive John Thomas. “We intend to take a crowdsourcing approach to generate a new industry buying platform that helps fleets better transition to a cleaner operation, offer financial benefits to customers and grow new jobs for the future of America.”
As an electric powertrain systems provider, ALTe will offer certified full-sized pickups and vans that have been retrofitted with electric or plug-in hybrid powertrains. Designed to replace a V-8 internal combustion engine powertrain, the system’s patented technology improves fuel economy, the company said. Visit www.altept.com.