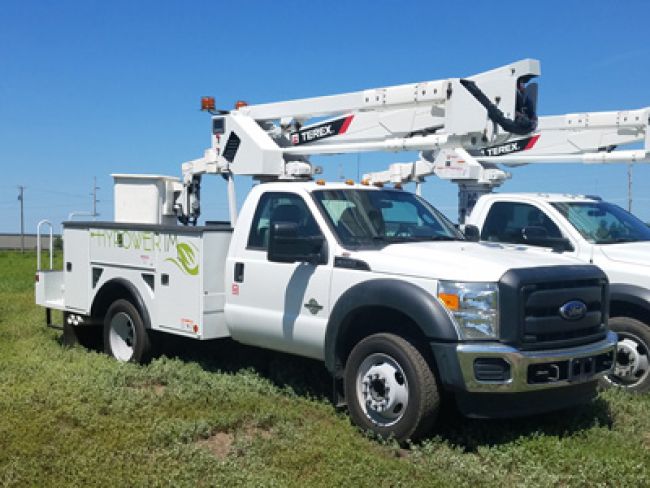
Bucket Trucks, Powered Up
New Jersey-based Public Service Electric and Gas Co. (PSE&G) has a little over 500 bucket trucks in its fleet. Of those, 327 have some degree of electrification. That might mean an original Bohlinger electric drive system from decades back, or perhaps a more current and elaborate work-up that operates the boom and provides climate control of the cab and exportable power for the crew.
“A lot of the technology [crews were] using, years ago, it would have been very hydraulically driven,” said Jay Marchitello, PSE&G transportation supervisor. “For instance, up at the pole top, they would use hydraulic tools to drill holes, screw conductors together and what have you. Now, however, that’s changed to battery-powered tools; they’re lighter, there’s less impact on the people, and less impact on the truck.”
The exportable power of the complete system, then, allows the crews to charge and use these battery-powered tools at the top.
It’s a long way from where they began.
Back in 2007, PSE&G became one of the first utilities in the U.S. to use hybrid aerial lifts, installing electric drive units in its traditional lifts. The lifts could operate on battery power, reducing idling time as well as carbon emissions. Even before that, though, the utility implemented the Bohlinger electric drive systems, powering hydraulic systems through batteries driving a DC motor pump combination. That early-generation option was “really just a forklift-style battery, a separate switch that turned the system on and let you use the bucket truck electrically,” Marchitello said. “But as hydraulic demand of the trucks became greater, more robust systems had to come out to support this.”
PSE&G was heavily into the movement for the electrification of booms and the use of electric power takeoff systems (ePTOs). Then anti-idling legislation spurred the utility to look for further options, moving more toward idle reduction as its emphasis.
Of course, needs vary among different utilities, and a variety of options have surfaced as batteries have gotten lighter and as chassis manufacturers are moving toward offering idle-mitigation solutions and engine-off cab comfort themselves.
At Terex Utilities (www.terex.com/utilities), for example, the conversation a decade ago was focused primarily on providing ePTOs for extended use, said Ted Barron, vertical market manager. The original HyPower Hybrid System, which came out in 2007, was a ready solution for lengthy work to be done while the vehicle was sitting still. The Terex HyPower system evolved and expanded across the product line over time. In 2017, Terex introduced HyPower IM.
“The ‘IM’ stands for ‘idle mitigation’ and offers a lighter-weight and lower-cost system that is made for trouble truck service work, where the aerial lift is deployed multiple times in a day for short periods of time,” Barron said.
What’s Needed?
As ePTO and anti-idling options abound, it begs the question: How are utility fleet professionals supposed to know what’s needed in their fleets?
Barron, who also is chairman of the Green Truck Association’s board of governors, said the first questions to ask when spec’ing an ePTO system have to revolve around the truck’s duty cycle.
Questions also must focus on reliability. Systems have improved over time, Barron said, but fleet professionals looking for solutions should still seek out other users for stories about their experiences. Despite customer desire for products that save fuel and are more environmentally friendly, such systems remain a small percentage of overall sales for Terex Utilities, at less than 10%.
Marchitello, meanwhile, said it’s important to know how quickly a system’s battery pack can replenish itself after being used in driving; the longevity of the battery can still be an Achilles’ heel.
“As battery technology has gotten better over the years, we’ve seen an increase in longevity, and that’s going to keep getting better, because batteries are becoming lighter and lighter,” Marchitello said. In years past, he noted, a large forklift battery might have weighed 2,000 pounds, chipping away at payload and fuel economy. “Now, the battery might weigh a few hundred pounds and have the same capacity as that 2,000-pound battery had. With some trucks, we now see three or four years before they need any kind of major maintenance on their battery systems.”
Fleet professionals also should ask about the infrastructure needed to charge the systems at their home bases.
One other consideration? There might be concern about what the operators will think. Marchitello, however, said he’s seen many come to enjoy the quiet environment electrification – at any level – can provide.
About the Author: Fiona Soltes is a longtime freelance writer based just outside Nashville, Tennessee. Her clients have represented a variety of sectors, including fleet, engineering, technology, logistics, business services, retail, disaster preparedness and material handling. Prior to her freelance career, Soltes worked as a staff writer at newspapers in Tennessee and Texas.
*****
By the Numbers
There’s no doubt that electrification during idling saves fuel. As for the environment? Jay Marchitello, transportation supervisor at PSE&G, estimated that his utility’s bucket trucks sit three hours per day running on battery power rather than fuel, “which equates to a lot.” With an average of 22.38 pounds of carbon dioxide emitted per gallon of diesel burned, that means a reduction of over 4.5 million pounds of carbon dioxide per year by PSE&G alone.
“You’ll always have your naysayers, the people who say that these things won’t work,” Marchitello said. “But then you see the confidence of the users, and how these trucks perform, and that doubt starts to shift on its own.”