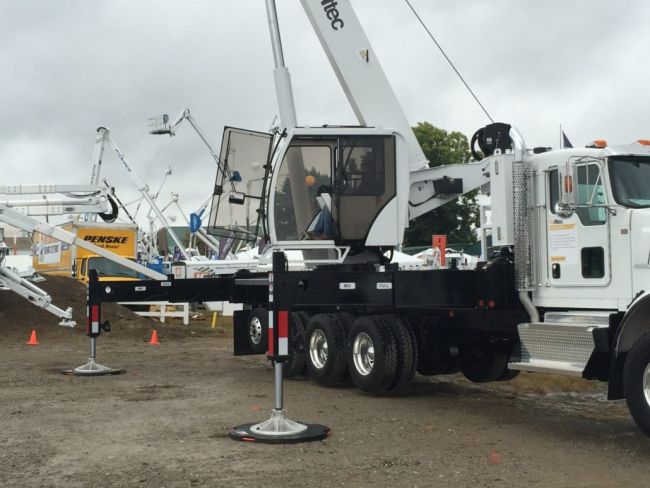
Using Supporting Materials with Stabilizers and Outriggers
Knowing the pressure the ground can withstand and how to use these materials is critical to job site safety.
When utility workers are tasked with setting up equipment, oftentimes it’s along roadsides with slopes, ditches or unstable surfaces. Unfortunately, equipment tip-overs continue to be one of the most common job site accidents, but they are generally preventable with proper planning, training and the use of outrigger pads, cribbing or blocking. Knowing when and how to use these types of products is essential in avoiding these types of accidents.
Truck-mounted equipment frequently used in utility applications – such as aerial devices and digger derricks – will usually be equipped with one of two types of stabilization gear: stabilizers or outriggers. Compact crawler lifts, which can be found in vegetation management applications, are not truck-mounted, but they also have outriggers that must be deployed correctly.
Utility companies should develop a comprehensive plan that establishes procedures for equipment setup. Product selection should be based on the loads and pressures generated by the equipment, the allowable ground-bearing pressure, and other common field needs, such as setting up on slopes or hillsides.
When selecting an outrigger pad, several criteria should be considered, including strength and stiffness of the pad’s material; its size, shape and features; and total cost of ownership.
An outrigger pad size and type can be determined once the minimum required bearing area is established. To establish the bearing area, outrigger or stabilizer loads must be known and the allowable ground-bearing pressure must be determined. The minimum bearing area required can be calculated by dividing the outrigger or stabilizer load by the allowable ground-bearing pressure.
Lastly, to support crews working in unlevel areas, cribbing products can be identified based on height requirements and other potential features, such as interlocking functionality.
Following is a short case study on the process one company followed to develop their equipment setup policy and procedures.
Case Study: Establishing a Safe Setup Policy
Over 20 years ago, EnergyUnited, an electric cooperative in North Carolina serving 19 counties across the state, realized that the wooden timbers they were using for outrigger pads created productivity and safety concerns.
Jimmy Brown, director of fleet services for the cooperative, said that for many years, electric utilities cut sections from wood timbers and bolted them together, then drilled a hole and used rope for a handle. The technique worked, but the final product was cumbersome to handle and transport.
“Pads were hard to keep clean, the edges would wear, and they’d get heavy when they got in the mud,” Brown said. “The wood also degrades when exposed to water and delivered inconsistent performance.”
So, Brown led an initiative to create a company policy that guides equipment purchases so they meet the needs of the crews and the applications. This initiative provided an opportunity for field personnel to provide input while standard specification requirements were being established. Creating standard spec documents for aerial devices and digger derricks is recommended by ANSI to streamline spec’ing and quoting.
Today, EnergyUnited has a policy that all of their bucket trucks, digger derricks and small crane trucks must be set up using outriggers pads. The cooperative specs their trucks to be upfitted with storage bins that accommodate the outrigger pads they want to store on each truck.
After researching various manufactured outrigger pads, EnergyUnited has standardized their trucks with DICA’s SafetyTech Outrigger Pads, Cavity Pads and SlotLock Cribbing Blocks.
“We worked with DICA to complete an assessment of our outrigger requirements, which included the weight of the trucks, boom and brand information, lift capacity and reach,” Brown explained. “We used the standard outrigger pads from DICA for years until the development of the cavity pads. These cavity pads work great to keep the outriggers from sliding off the pad, and they are lighter, which makes handling easier.”
Brown noted that cribbing blocks are used when additional height is needed due to unlevel terrain. When working on such terrain, crews will typically use cribbing blocks on one side of their truck to keep the truck stable.
“Safety is such a key issue for us, our employees, members and for the general public,” he said. “There is no shortage of outrigger pads or cribbing blocks available on the market, but we wanted to align with someone who builds a reliable product and who would be available to answer our questions. DICA was the answer to all those questions.”
Useful Reminders
There are a number of items to keep in mind when working with equipment that uses stabilizers or outriggers. For instance, pieces of equipment that have stabilizers do not lift themselves off the ground; the tires on the chassis are the main support for the equipment. Stabilizers, which extend from the chassis at an angle, provide balance and exert significantly less force on the ground because the tires remain in contact with the ground. Stabilizers are typically found on aerial devices and smaller digger derricks. In some cases, there will be only one set of stabilizers behind the truck cab; in other cases, there may be two sets: behind the cab and at the rear of the chassis.
Equipment that lifts itself off the ground, such as boom trucks and larger-capacity digger derricks, is equipped with outriggers. The outriggers extend out and down from the chassis and provide the only points of contact with the ground during operation. Outriggers will exert more ground-bearing pressure than stabilizers, and the amount of ground-bearing pressure may change as the boom of the aerial device or digger derrick rotates through its working range.
Both stabilizer- and outrigger-enabled equipment may also have an extra bumper outrigger, which is a hydraulic cylinder or manual jack located on the front bumper of the truck.
Regardless of the type of stabilization system a piece of equipment is fitted with, it is highly recommended to always use some kind of supporting materials between the equipment float, foot or pontoon and the ground.
The purpose of supporting materials is to spread concentrated pressures from equipment over a large enough area to levels the ground can withstand, specific requirements, or specified levels based on allowable ground-bearing pressure. Selection of supporting materials should be based on two primary criteria: They should be strong enough to withstand the exerted loads, and they should be stiff enough to distribute the loads over the intended area. The larger the load distribution area needed, the more rigid the supporting materials must be.
Operating within level tolerances is critical. If a slope is unavoidable, the bank of the slope may need to be cut away to establish a flat area, and cribbing should be used to fill the gap to help level the equipment. Keep in mind that when operating on a slope, there is always the potential for equipment to move.
Finally, additional products to help provide safety and support to your crews include wheel chocks and ground protection mats or temporary roads. A good safety and operational plan should include guidance about how to safely, quickly and easily maneuver in and out of job sites without leaving any indication you were there.
About the Author: Kris Koberg is the CEO of DICA (https://dicausa.com).
- The End of the Pin-On Man Basket
- Using Supporting Materials with Stabilizers and Outriggers
- What’s New in Utility Construction Equipment in 2023?
- 7 Ways Fleet Professionals Can Use ChatGPT to Boost Productivity
- The Best Specs for Cable Reel Trailers
- Tap into ‘The Wisdom of the Bullfrog’ for Career Growth
- Best Practices for Managing a Shared Vehicle Pool
- How to Make the Right Choice: Gas vs. Diesel for Medium-Duty Trucks
- The Utility Expo 2023: A Preview
- Establishing and Managing Service-Level Agreements