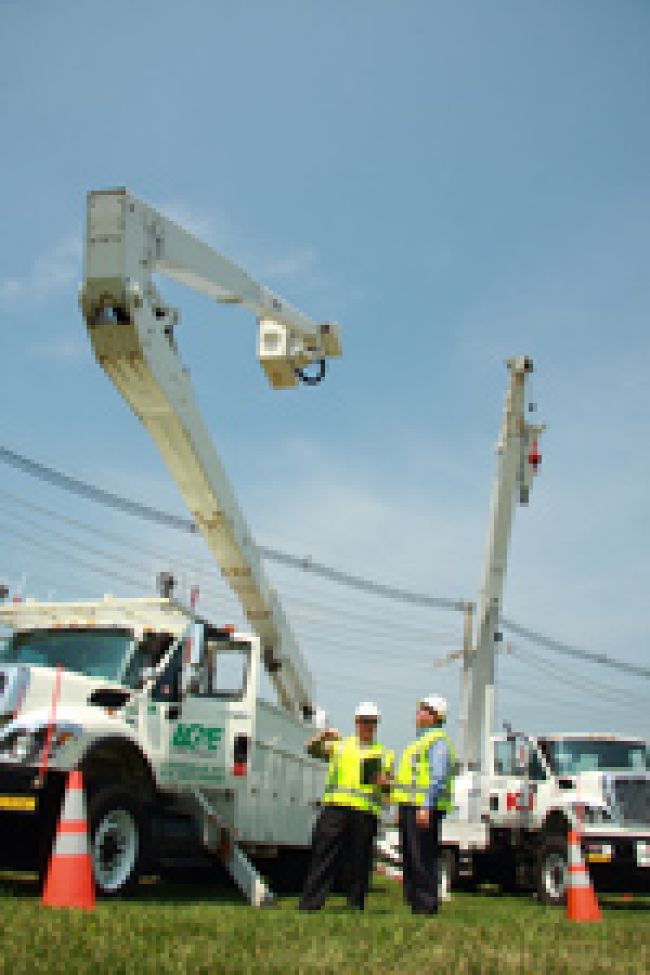
Continuous Improvement
Louisville Gas and Electric Company (LG&E) and Kentucky Utilities Company (KU) are well known in the industry for creative approaches to continuous improvement and outstanding performance in many respects – including the operation and maintenance of their vehicle and equipment fleet. The companies’ fleet is recognized as one of the most reliable and efficient in the industry. It consistently ranks in the top quartile in overall cost management, cost per mile, fuel costs and other components when benchmarked against other utilities. But that’s not good enough. Keeping with LG&E and KU’s style of being the best they can be, the companies continue to search for safety enhancements and operating efficiencies that will benefit their operators and customers.
The LG&E and KU fleet consists of about 1,600 units, including light- and heavy-duty vehicles, trailers, heavy-duty and power equipment, and a small number of hybrids. The fleet is managed by the Transportation Department in Energy Delivery (E.D.), the business unit that distributes natural gas and electricity and provides services to the company’s 1.2 million customers. The bulk of the fleet is utilized by E.D. employees who drive about 13 million miles per year across the Kentucky and Virginia service territory.
Ongoing Evaluation
“The key components of our business model are safety and service restoration,” says Bill Doggett, manager, transportation. “We want to ensure our equipment and employees can respond safely and quickly to customers’ needs, while operating cost-effectively, within all government regulations and in an environmentally friendly manner. That requires continuous re-evaluation of our needs and standards as well as manufacturers – all of which constantly change.”
Like many utilities, LG&E and KU’s diverse service territory challenges the companies’ ability to ensure DOT compliance, efficiently manage its fleet and balance customer service needs. It includes complex metro areas, rural backwoods, and the hollows and hilltops of the Appalachian Mountains, which make matching vehicle type and payloads with work needs daunting.
In the LG&E and KU service territory’s urban areas, patchworks of old and new infrastructures consist of different standards and equipment types. In rural and mountainous areas, terrain is a factor, so size and maneuverability become critical considerations when operating along tight mountain and country roads. Determining which parts and equipment to carry and how to optimize payload is also critical. Vehicles with lower weight allowances can impact service restoration timing because the number of tools, parts and other items they carry is restricted. Traveling many miles back to a service center for additional items isn’t an option in remote areas when working against service restoration deadlines.
Strategic Approach
To address these and other issues, last year LG&E and KU launched an aggressive, user-based fleet management strategic planning process that is streamlining its fleet and netting other benefits – particularly pertaining to employee awareness and safety.
The process began with teams, representing the transportation, safety and operations areas that developed and implemented fleet standards and controls for the heavy- and light-duty fleets. They ensured the companies’ “No Compromise” safety approach was incorporated into every initiative, optimized operational efficiency and assured regulatory compliance. The teams enlisted the recommendations of an outside contractor and, more importantly, the employees who use the vehicles and equipment. They included managers and frontline employees who formed additional heavy- and light-duty vehicle user teams, which inspected their vehicles, double-checked DOT compliance against standards, and reported questions and concerns.
“We gained a great deal of valuable information by including the individuals who actually drive the vehicles and use the equipment,” Doggett states. “They asked questions pertaining to situations that were job-specific and that aren’t in the manual, such as how to handle weight limits on roads and bridges in certain rural areas. It was a learning experience for us as well as them. The teams, as a combined working unit, had to develop solutions.”
Increased awareness among the workforce about DOT compliance was one of the greatest benefits of the process. The companies are recognized in the industry, nation and globally as safety leaders.
“This enabled us to close the circle of safety on yet another aspect of our operations,” says Ken Sheridan, manager, public and operational safety. “Our employees reaffirmed the company’s compliance with Department of Transportation regulations, which are specifically designed to ensure their safety as well as the public’s. Most importantly, they became better educated about how to manage compliance responsibilities and other safety requirements associated specifically with their vehicles or equipment. This is a huge perk for our companies.”
Business partners who support LG&E and KU’s purchasing, maintenance and repair work were also involved in and trained on the process. This is the same approach the company takes with safety initiatives, because the more people who are knowledgeable, the more who can support the achievement of goals. Business partners also must be in step with the changing needs of the business and, consequently, the final strategy’s content was critical to ensure they continued to support operating efficiency and safety.
“We believe in a top-led, employee-driven approach to safety,” says Sheridan. “Any time we give employees or our business partners responsibility for any aspect of operations or safety, they take charge. That’s why we have an outstanding safety culture.”
Improving Awareness
In addition to employee involvement, other measures helped to reinforce DOT compliance and safety awareness among the workforce at LG&E and KU. The companies tagged vehicles and trailers with decals listing the gross vehicle weight rating, gross combined weight rating and maximum allowable payload so drivers can accurately control payload and trailer towing capacity. They also purchased heavy-duty weight scales to:
• Validate the weight of newly ordered vehicles;
• Perform random weight audits as part of scheduled routine maintenance; and
• Perform weight checks following functional or driver changes.
Environmental concerns also play an important role in setting fleet standards, particularly at LG&E and KU, which are also recognized for environmental leadership. While the companies’ total fleet mileage has risen since 2007, carbon dioxide emissions have actually been reduced during that same time span. The challenge will be to sustain that success. As part of the fleet strategy, demands for larger construction equipment will have to be offset in other areas, especially the light-duty fleet. Including more hybrids in the fleet and other tactical initiatives, such as evaluating vehicle assignments, the take-home policy and the percentage of four-wheel drive vehicles, will all contribute to the success of this endeavor.
Never Ending
At LG&E and KU, the fleet strategic planning and evaluation process is never-ending. The companies continue to benchmark all aspects of their operations. Transportation policies are updated continually to reflect changes necessary for efficiencies and cost-effective measures. Additionally, other initiatives are underway to:
• Simplify and reduce the number of company vehicle standards by harmonizing business models, payload and equipment needs;
• Improve maintenance parameters, including extending preventive maintenance schedules and oil change cycles, enhancing tire management through the use of retreads and utilizing more advanced preventive maintenance technology;
• Reduce light-duty vehicle usage costs by right-sizing vehicles for the assignment and needs;
• Establish heavy-duty equipment/vehicle decision matrices for making cost-effective decisions about what unit is best suited for an operation and to support decision-making by managers when placing new orders; and
• Harmonize equipment pricing incentives with LG&E and KU’s parent company, PPL Corporation, based in Allentown, Pa. Both companies utilize Ford light-duty vehicles and Altec bucket trucks, creating a potential opportunity for lower costs at both companies.
Through a continuous and wide-ranging effort, LG&E and KU are finding new programs and practices that improve fleet performance.
Louisville Gas and Electric Company and Kentucky Utilities Company, part of the PPL Corporation (NYSE: PPL) family of companies, are regulated utilities that serve a total of 1.2 million customers. LG&E serves 321,000 natural gas and 397,000 electric customers in Louisville and 16 surrounding counties. Kentucky Utilities serves 546,000 customers in 77 Kentucky counties and five counties in Virginia. More information is available at www.lge-ku.com and www.pplweb.com.