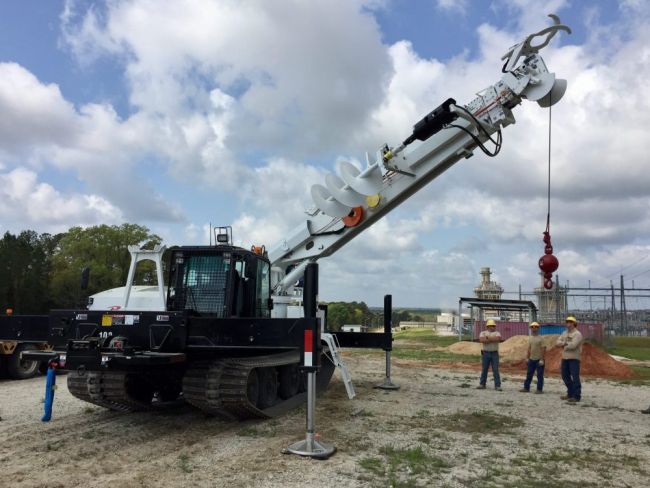
Maximizing ATUV Uptime: Essential Maintenance Practices for Utility Fleets
All-terrain utility vehicles (ATUVs) are critical assets for utility operations, often working in challenging environments where standard vehicles just can’t go. Maintaining these specialized machines is crucial for ensuring their reliability, longevity and optimal performance. With nearly three decades of experience in the ATUV industry, I’ve seen firsthand the importance of proper maintenance practices. The remainder of this article offers some key insights for utility fleet managers looking to maximize ATUV uptime and minimize costly downtime.
The Importance of Preventive Maintenance
One of the biggest mistakes in ATUV maintenance is neglecting regular, scheduled service. In utility operations, these vehicles often work in short bursts, remaining stationary for extended periods. This can create a false sense that they require less maintenance. However, adhering to a strict preventive maintenance schedule is necessary to avoid unexpected breakdowns and costly field repairs.
Prinoth, the company I work for, recommends maintenance every 500 engine running hours or at least once annually, whichever comes first. Even if a vehicle hasn’t reached the 500-hour threshold, annual maintenance is essential to ensure the integrity of oils and other fluids, which can degrade over time regardless of use.
Critical Inspection Points
Daily visual inspections are one of the most effective ways to catch potential issues before they become major problems. Key areas to focus on include the following:
- Undercarriage: This is the hardest-working part of an ATUV, and it takes a lot of abuse. Check for oil leaks, damage to tracks, and issues with sprockets or bogies.
- Electrical and hydraulic lines: Look for any signs of stress from excess concussive force and vibration. Check for areas where cables, wires and hoses might be rubbing against sharp metal edges, which can lead to corrosion and leaks.
- Frame: Inspect for any cracks or signs of stress.
- Vehicle-mounted equipment: Pay close attention to attachments and their connection points to the chassis. Follow the manufacturer’s recommendations on equipment-specific maintenance intervals.
Keeping the machine clean is vital for effective inspections. Pressure-washing the ATUV when possible – and always washing it when it returns to base – makes it much easier to spot potential issues.
Technician Training and Resources
Well-trained technicians are the backbone of any effective ATUV maintenance program. The company I work for offers comprehensive training programs, including on-site instruction, online courses and hands-on exercises. These programs often cover topics such as electrical systems, hydraulics and specific maintenance procedures for our different ATUV models. I suggest checking to see what training methods chassis manufacturers offer before you buy.
Additionally, ensure that maintenance teams have access to up-to-date manuals and resources.
Adapting to Extreme Conditions
ATUVs often operate in challenging environments, from arctic cold to desert heat to moist jungle conditions. Fleets should adapt maintenance practices – including the following – for those conditions unique to any particular vehicle or fleet:
Fluids: Use appropriate hydraulic fluids, lubricants and coolants for the operating environment. In areas with extreme temperature variations, seasonal fluid changes may be necessary.
Undercarriage: In muddy or icy conditions, pay extra attention to the undercarriage. Most ATUV designs feature walking-beam suspensions, which can accumulate debris that needs to be periodically removed.
Operator practices: Train operators to avoid unnecessary strain on the vehicle, such as running over avoidable obstacles like stumps, boulders and logs when possible.
Leveraging Technology for Maintenance
Modern ATUVs often come equipped with advanced telematics systems. These tools can provide real-time data on vehicle performance, maintenance needs and potential issues. Fleet managers can use this information to schedule preventive maintenance more effectively and address problems before they lead to breakdowns.
When selecting an ATUV, consider the comprehensiveness of its telematics system. Some systems only provide engine data while others offer a complete, real-time picture of the entire vehicle’s status.
Looking to the Future
The future of ATUV maintenance is likely to involve even closer collaboration between chassis manufacturers and equipment upfitters. These partnerships aim to create designs that facilitate easier maintenance access and streamline servicing procedures.
As ATUVs continue to evolve, we can expect to see more emphasis on easy-access panels, centralized filter locations and other design features that simplify maintenance tasks.
Don’t Forget
Maximizing ATUV uptime ultimately comes down to three key factors: thorough training, consistent maintenance and cleanliness. By focusing on those areas, fleet managers can ensure their ATUVs remain reliable, efficient and ready for the challenging work they face in their utility operations.
Remember, the cost of regular maintenance is always lower than the cost of unexpected downtime and emergency repairs in the field. Investing in maintenance protocols for your fleet’s ATUVs will pay dividends in improved performance, longevity and reliability.
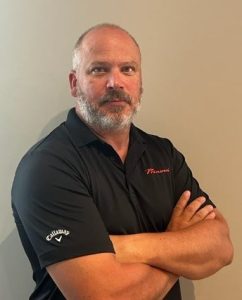
About the Author: Gerry Carriere is a service representative and tracked vehicle specialist for Prinoth (www.prinoth.com) with nearly 30 years of experience. His extensive career has included roles in manufacturing, engineering and field service prior to becoming a service representative 11 years ago.
Images courtesy of Prinoth
- The State of Self-Driving Trucks
- How Will AI Impact Your Fleet Operations?
- Keeping Your Best: Effective Strategies for Retaining Top Fleet Technicians
- SEMA Predicts Biggest Show in Five Years
- 8 ChatGPT Prompts to Boost Productivity, Improve Your Effectiveness
- The Future of Telematics: Top Trends to Watch
- Maximizing ATUV Uptime: Essential Maintenance Practices for Utility Fleets
- Best Practices for Developing an In-House Maintenance Policy for EVs