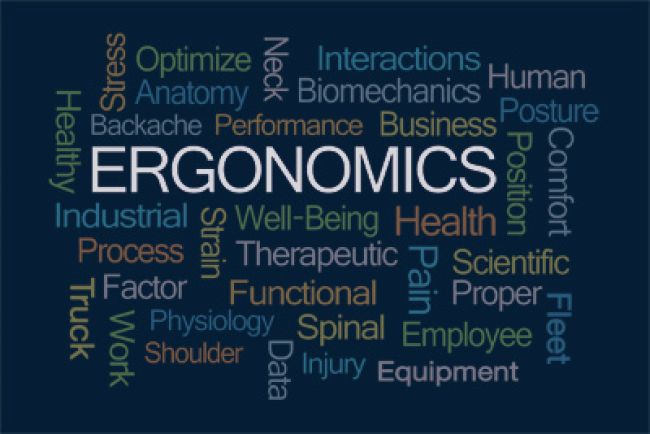
Utility Fleet Ergonomics: A Continuing Challenge
Workplace ergonomics have been on employers’ radar for 20 years, but even now, ergonomic-related injuries remain a costly expense – one that’s growing due to an aging workforce, current worker shortages and inexperienced industry newcomers.
“As the age composition of the workforce changes, that does affect industry,” said Eric Bauman, principal technical leader and program manager for the Occupational Health and Safety Program at the Electric Power Research Institute (www.epri.com). “Now that early Baby Boomers have retired and the middle Boomers are retiring, the industry has been hiring new workers who tend to be less experienced. We’ve seen an increase in injuries in this younger age group.”
The primary causes of employee accidents haven’t changed much in the past two decades. “It’s the slips, the falls, the trips,” said Mark Stumne, director of truck and upfit at Element Fleet Management (www.elementfleet.com).
Bauman agreed. “Sprains and strains showed up in the first year or two in our industry injury database as the largest single category of injuries,” he said. “It’s continued since 1999. Sprains and strains are something we can do something about, and this industry has supported ergonomic research since then.”
Despite the seeming intractability of these types of injuries, there are myriad products available in today’s marketplace designed to help alleviate them. Where is a fleet to start?
At Nebraska Public Power District, addressing ergonomics means navigating a balance between work truck needs and cabin comforts. “We let the work needs determine the lowest cost-trim level, then get all the comfort appointments available within that trim,” said Matt Gilliland, NPPD’s director of operations support.
It then comes down to options. Gilliland’s focus recently has turned to added equipment, with an eye toward how a utility worker accesses that equipment. “Often it is counter to what the industry can offer, historically has provided or can allow via regulations,” he said. “This has created an entirely new dialogue and has really changed how we spec trucks.”
NPPD has zeroed in on how workers enter and exit vehicles, as well as how equipment is placed so that the workers do not have to reach or strain. “These things have resulted in extra handholds, more steps, mobile and movable steps, the relocation of toolboxes, ladder fold-down brackets and so on,” Gilliland said.
Shaking Up Tradition
Today’s utility fleet vehicles are bigger and taller than in the past. And that, coupled with the lack of agility that comes with a worker’s age, is driving changes to traditional steps out of the vehicles, Stumne said. “A stirrup step might have been typical in the past. But that’s one area where we’ve encouraged our clients to add proper steps at the right height.”
Of course, not every potential ergonomic injury has an equipment solution – at least not a cost-effective one. But while no fleet has an unlimited budget, equipment costs should not necessarily always be an organization’s greatest concern. “There’s a reduced workforce to pull from and utility is a tough business,” Stumne said. “Employees work hard and it’s hard to pull people into the industry. You have to focus on giving those drivers the best equipment possible.”
The Electric Power Research Institute has developed a series of handbooks designed to help workers avoid injuries, including one on upfitting and purchasing vehicles. A study also is underway focusing on safety aspects of using augmented reality displays, including ergonomics and situational awareness. In addition, a forthcoming handbook focuses on work methods and tools to reduce injuries from awkward postures.
The EPRI handbooks include simple and cost-effective implementations, such as purchasing new hand tools. “In some cases, the cost to implement these is minor,” Bauman said. “When you replace a tool, you look for a more ergonomic tool, or when you order new fleet vehicles, you include ergonomic features from the beginning.”
Operator feedback may be the best and quickest way to evaluate the ergonomic solutions currently available. “Yes, it is qualitative,” Gilliland said. “But awaiting the passage of time to evaluate an ergonomic investment and quantify its impact on injuries will simply take too long. There should be specification discussions after the new truck is placed into service, just like there are conversations before it is purchased.”
*****
The High Cost of Ergonomic Injuries
OSHA tracks ergonomic injuries under its musculoskeletal disorders category. In 2013, the most recent year for which statistics are available, OSHA found ergonomic injuries:
- Accounted for 34 percent of all workplace injuries and illnesses requiring days away from work.
- Had an incidence rate of 38 cases per 10,000 full-time workers.
- Required an average of 12 days of recuperation.
The length of recuperation varied based on where on the body the injury occurred.
- Shoulder: 24 days
- Stomach: 21 days
- Wrist: 18 days
- Leg: 17 days
- Arm: 17 days
- Multiple body parts: 17 days
- Back: 7 days
Following are the most injured body parts:
- Back: 36%
- Shoulder: 13%
- Knee: 12%
- Ankle: 9%
- Multiple: 8%
- Arm: 4%
- Wrist: 3%
- Neck: 2%
- Hand(s): 2%
- Foot: 2%
The most common causes of ergonomic injuries are:
- Overexertion: 63%
- Falls, slips and trips: 23%
- Contact with object or equipment: 5%
- Violence and other injuries: 5%
- Transportation accidents: 4%